The PVD (Physical Vapor Deposition) coating process is a sophisticated technique used to apply thin, durable coatings to various materials, primarily metals. The duration of the process can vary significantly, typically ranging from 30 minutes to 2 hours, depending on factors such as the desired coating thickness, the size of the workpiece, and the specific type of PVD process employed. The coating thickness usually ranges between 0.25 microns and 5 microns, and the process involves several key steps: Vaporization, Reaction, and Deposition. Each step plays a crucial role in determining the final properties of the coating, such as hardness, color, and resistance to corrosion and oxidation.
Key Points Explained:
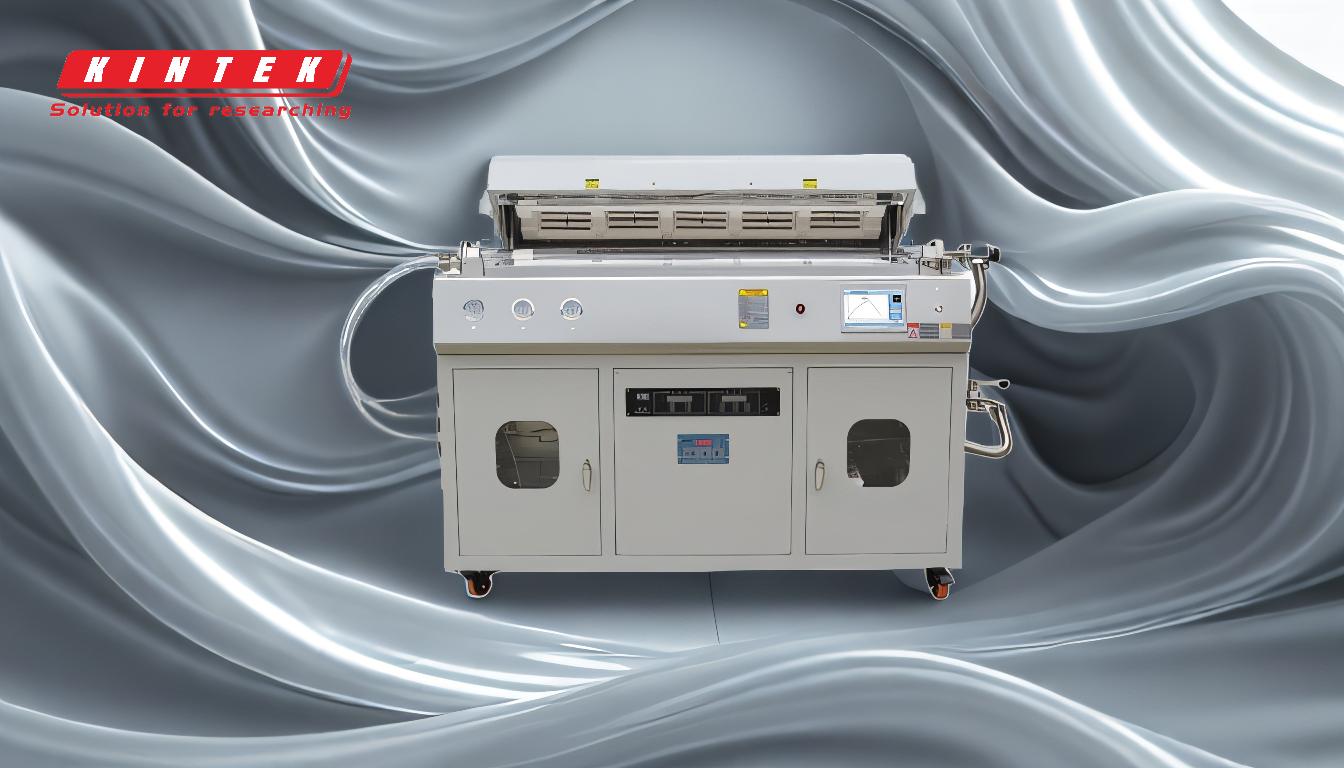
-
Duration of the PVD Coating Process:
- The PVD coating process generally takes between 30 minutes to 2 hours. Smaller or simpler pieces may require less time, while larger or more complex items may take longer.
- The time required can also depend on the desired coating thickness, with thicker coatings necessitating longer processing times.
-
Coating Thickness:
- PVD coatings are typically very thin, ranging from 0.25 microns to 5 microns. This thin layer is sufficient to provide significant improvements in properties such as hardness, corrosion resistance, and aesthetic appearance.
- The thickness of the coating is a critical factor in determining the overall durability and performance of the coated material.
-
Types of PVD Coating Processes:
- Sputter Coating: Involves bombarding a target material with high-energy ions to eject atoms, which then deposit onto the substrate.
- Thermal Evaporation: Uses heat to vaporize the coating material, which then condenses onto the substrate.
- Electron Beam Evaporation: Utilizes an electron beam to heat and vaporize the coating material.
- Ion Plating: Combines vaporization with ion bombardment to enhance the adhesion and density of the coating.
- Each process has unique characteristics and advantages, making them suitable for different applications and materials.
-
Steps in the PVD Coating Process:
- Vaporization: The target material is converted into vapor through various methods such as sputtering or evaporation.
- Reaction: The vaporized material reacts with gases in the chamber to form compounds that determine the coating's properties, such as hardness and color.
- Deposition: The vaporized and reacted material deposits onto the substrate, forming a thin, uniform coating.
-
Properties and Applications:
- PVD coatings are highly resistant to corrosion and oxidation, making them ideal for use in harsh environments.
- The hardness of the coating is a crucial factor in its durability, with materials like TiN (Titanium Nitride) significantly enhancing the fatigue limit and endurance of the substrate.
- PVD coatings are commonly applied to stainless steel, providing a variety of finishes such as polished, brushed, satin, or matte, depending on the surface preparation.
-
Surface Preparation:
- The substrate's surface condition is essential for achieving the desired finish. Polished or mirror surfaces are used for polished PVD finishes, while brushed or satin surfaces are used for satin or matte finishes.
- PVD coatings do not level or fill surface imperfections, so the substrate must be properly prepared before the coating process.
Understanding these key points can help in selecting the appropriate PVD coating process and parameters for specific applications, ensuring optimal performance and longevity of the coated materials.
Summary Table:
Aspect | Details |
---|---|
Duration | 30 minutes to 2 hours, depending on workpiece size and coating thickness. |
Coating Thickness | 0.25 microns to 5 microns, providing hardness, corrosion resistance, and more. |
Process Types | Sputter Coating, Thermal Evaporation, Electron Beam Evaporation, Ion Plating. |
Key Steps | Vaporization, Reaction, Deposition. |
Applications | Corrosion resistance, improved hardness, and aesthetic finishes for metals. |
Optimize your materials with PVD coatings—contact our experts today for tailored solutions!