PVD (Physical Vapor Deposition) vacuum plating is renowned for its durability and longevity, often surpassing traditional plating methods like electroplating. The lifespan of PVD coatings can vary significantly depending on several factors, including the type of substrate, coating thickness, bond strength, and environmental conditions such as exposure to heat, wear, and moisture. In ideal conditions, such as in the jewelry industry, PVD coatings can last up to 10 years with proper application and maintenance. The durability of PVD coatings is attributed to their atomic-level bonding with the base material, which ensures exceptional adhesion and resistance to wear, corrosion, and scratching. Real-life examples, such as watch cases and bands, demonstrate that PVD-plated items can maintain their original appearance even after years of regular use, including exposure to moisture and daily wear. However, while PVD coatings are highly resistant to wear and weather, aggressive attacks can damage the color, which may not be repairable in some instances.
Key Points Explained:
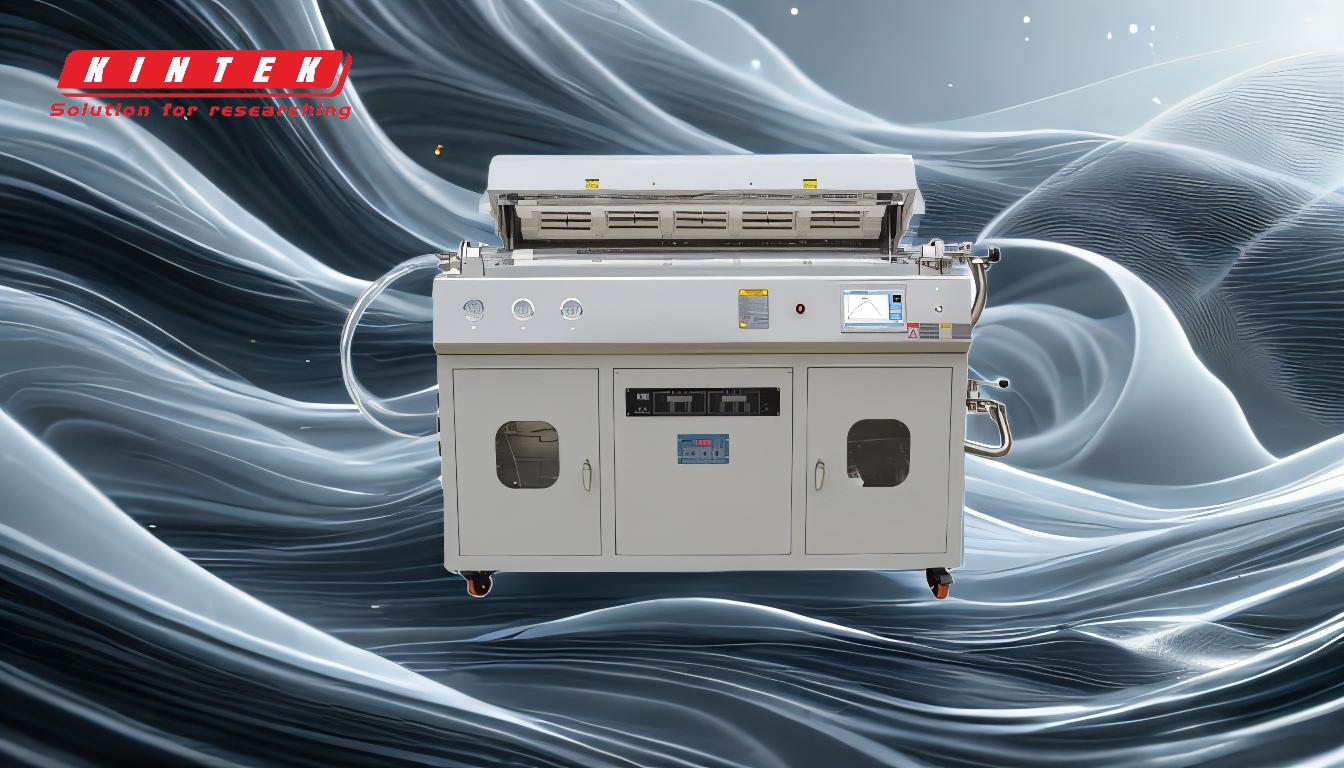
-
Durability and Longevity of PVD Coatings:
- PVD vacuum plating is more durable than traditional methods like electroplating due to its atomic-level bond with the base material, ensuring exceptional adhesion.
- The materials used in PVD plating, such as titanium nitride, have excellent hardness and wear resistance, contributing to the coating's longevity.
- In the jewelry industry, PVD coatings can last up to 10 years if applied correctly and maintained properly.
-
Factors Affecting PVD Coating Lifespan:
- Substrate Type: The material being coated can influence the durability of the PVD coating. For example, harder substrates may provide better support for the coating.
- Coating Thickness: Thicker coatings generally offer better protection and longer lifespan, though they may also affect the product's appearance and feel.
- Bond Strength: The strength of the bond between the coating and the substrate is crucial for long-term durability. PVD coatings form a strong bond due to the vacuum environment, which eliminates contamination.
- Environmental Exposure: Exposure to heat, wear, moisture, and other environmental factors can affect the lifespan of PVD coatings. Real-life examples, such as watch cases and bands, show that PVD-plated items can withstand regular use and exposure to moisture and sweat.
-
Resistance to Wear and Corrosion:
- PVD coatings provide superior resistance to corrosion and scratching due to the vacuum environment during application, which eliminates contamination and forms a stronger bond with the substrate.
- The vacuum environment also prevents oxidation and degradation caused by oxygen and moisture, further enhancing the coating's durability.
-
Real-Life Applications and Durability:
- Real-life examples, such as watch cases and bands, demonstrate that PVD-plated items can retain their original appearance even after years of regular use, including exposure to moisture, sweat, and daily wear.
- Despite their thinness, PVD coatings are strong, corrosion-resistant, and exhibit high levels of temperature and abrasion resistance, often eliminating the need for a top coating or additional support.
-
Limitations and Potential Damage:
- While PVD coatings are highly resistant to wear and weather, aggressive attacks can damage the color, which may not be repairable in some instances.
- The thinness of PVD coatings, while advantageous for retaining the product's original shape and providing a rich finish, may also make them more susceptible to damage under extreme conditions.
In summary, the lifespan of PVD vacuum plating can vary based on several factors, but with proper application and maintenance, it can last up to 10 years in some applications. The durability, resistance to wear and corrosion, and real-life performance of PVD coatings make them a superior choice for many industries, including jewelry and watchmaking. However, it's important to be aware of the potential limitations, such as the possibility of color damage under aggressive conditions.
Summary Table:
Aspect | Details |
---|---|
Lifespan | Up to 10 years with proper application and maintenance. |
Durability | Superior to traditional methods like electroplating due to atomic-level bonding. |
Resistance | High resistance to wear, corrosion, and scratching. |
Key Factors | Substrate type, coating thickness, bond strength, and environmental exposure. |
Real-Life Examples | Watch cases and bands retain appearance even after years of regular use. |
Limitations | Color damage may occur under aggressive conditions. |
Maximize the lifespan of your PVD coatings—contact our experts today for tailored solutions!