The time required for vacuum casting depends on several factors, including the complexity of the part, the type of material used, the size of the mold, and the specific vacuum casting process. Generally, vacuum casting can take anywhere from a few hours to several days. The process involves multiple steps, such as mold preparation, degassing, casting, curing, and post-processing. Each step contributes to the overall time, and the duration can vary based on the specific requirements of the project. For example, simpler parts with smaller molds may take less time, while complex geometries or larger molds may require additional time for curing and finishing.
Key Points Explained:
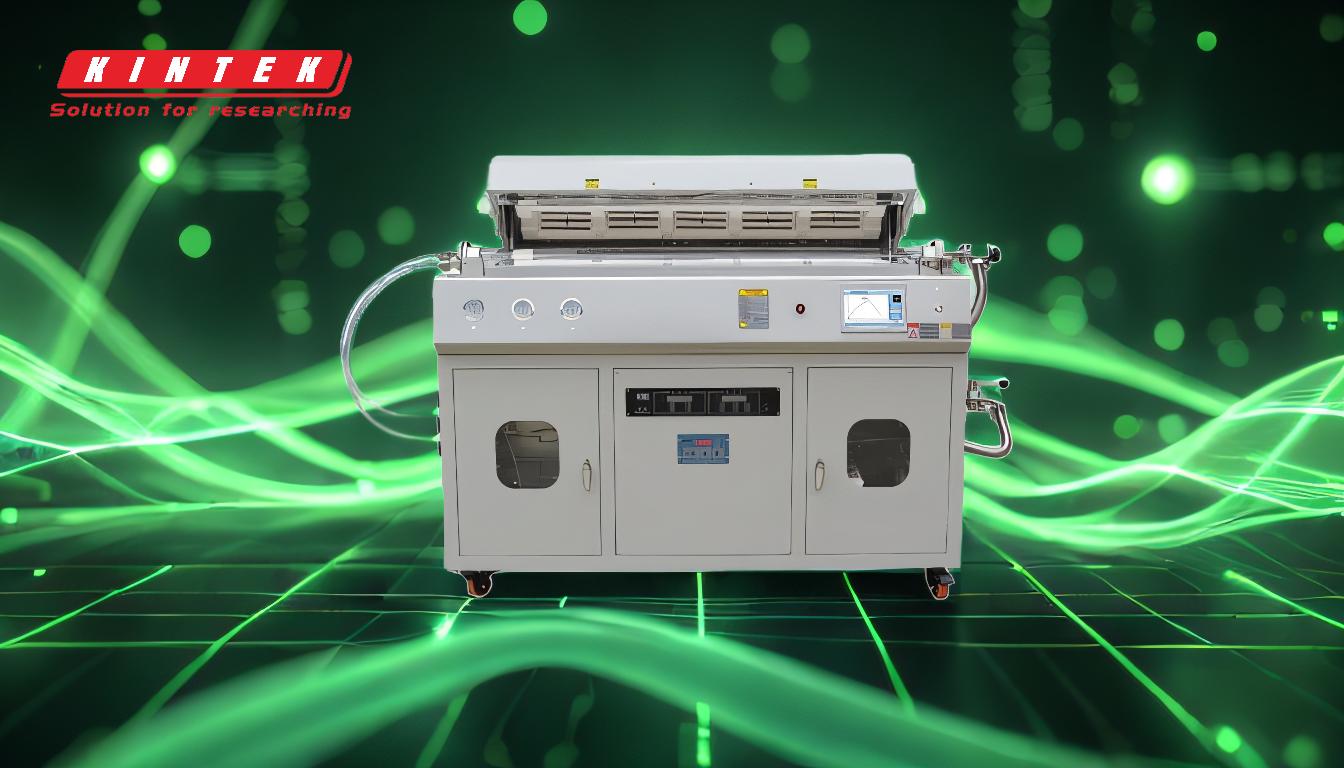
-
Mold Preparation:
- The first step in vacuum casting is preparing the silicone mold. This involves creating a master model, which is typically made using 3D printing or CNC machining. The master model is then used to create the silicone mold.
- The time required for mold preparation can vary depending on the complexity of the part and the quality of the master model. Simple molds may take a few hours, while more complex molds can take a day or more.
-
Degassing:
- Once the silicone mold is prepared, the next step is degassing. This involves placing the mold in a vacuum chamber to remove any air bubbles that could affect the quality of the final cast.
- Degassing typically takes around 30 minutes to an hour, depending on the size of the mold and the material being used.
-
Casting:
- After degassing, the casting material (usually a polyurethane resin) is poured into the mold. The vacuum casting machine is used to ensure that the material fills the mold completely and without air pockets.
- The casting process itself is relatively quick, usually taking only a few minutes. However, the time can vary depending on the size and complexity of the part.
-
Curing:
- Once the material is poured, it needs to cure. Curing times can vary significantly depending on the type of resin used and the size of the part. Some resins cure in as little as 30 minutes, while others may take several hours or even a full day.
- The curing process is critical to the strength and durability of the final part, so it’s important not to rush this step.
-
Demolding and Post-Processing:
- After the part has fully cured, it is removed from the mold. This step, known as demolding, usually takes only a few minutes.
- Post-processing may involve trimming excess material, sanding, painting, or other finishing touches. The time required for post-processing depends on the complexity of the part and the desired finish. Simple parts may require only a few minutes of post-processing, while more complex parts could take several hours.
-
Overall Timeframe:
- For a simple part, the entire vacuum casting process can be completed in as little as 4-6 hours, including mold preparation, degassing, casting, curing, and post-processing.
- For more complex parts, the process can take 24-48 hours or more, especially if multiple iterations or refinements are needed.
-
Factors Affecting Time:
- Part Complexity: More intricate designs with fine details or undercuts may require longer curing times and more careful post-processing.
- Material Choice: Different resins have different curing times, and some may require additional steps, such as heat curing, which can add to the overall time.
- Mold Size: Larger molds take longer to degas and cure, and they may also require more material, which can extend the casting time.
- Batch Size: If multiple parts are being cast in a single mold, the overall time will increase, but the time per part may decrease due to efficiencies in the process.
In summary, vacuum casting is a versatile and efficient method for producing high-quality parts, but the time required can vary widely depending on the specific requirements of the project. By understanding the factors that influence the process, you can better estimate the time needed for your particular application.
Summary Table:
Step | Time Required |
---|---|
Mold Preparation | Few hours to a day, depending on part complexity and master model quality. |
Degassing | 30 minutes to 1 hour, depending on mold size and material. |
Casting | A few minutes, varying with part size and complexity. |
Curing | 30 minutes to a full day, depending on resin type and part size. |
Post-Processing | A few minutes to several hours, depending on part complexity and finish required. |
Overall Timeframe | 4-6 hours for simple parts; 24-48 hours or more for complex parts. |
Need help estimating your vacuum casting timeline? Contact our experts today for personalized guidance!