The lifespan of a crucible depends on several factors, including the material it is made of, the operating conditions, and the specific application it is used for. Graphite crucibles, for example, are known for their long service life due to their excellent thermal stability, corrosion resistance, and ability to withstand high temperatures exceeding 2000°C. However, the actual lifespan can vary significantly based on the furnace type, the alloys being melted, temperature fluctuations, and maintenance practices. Proper selection and matching of the crucible to the furnace and application are critical to maximizing its lifespan.
Key Points Explained:
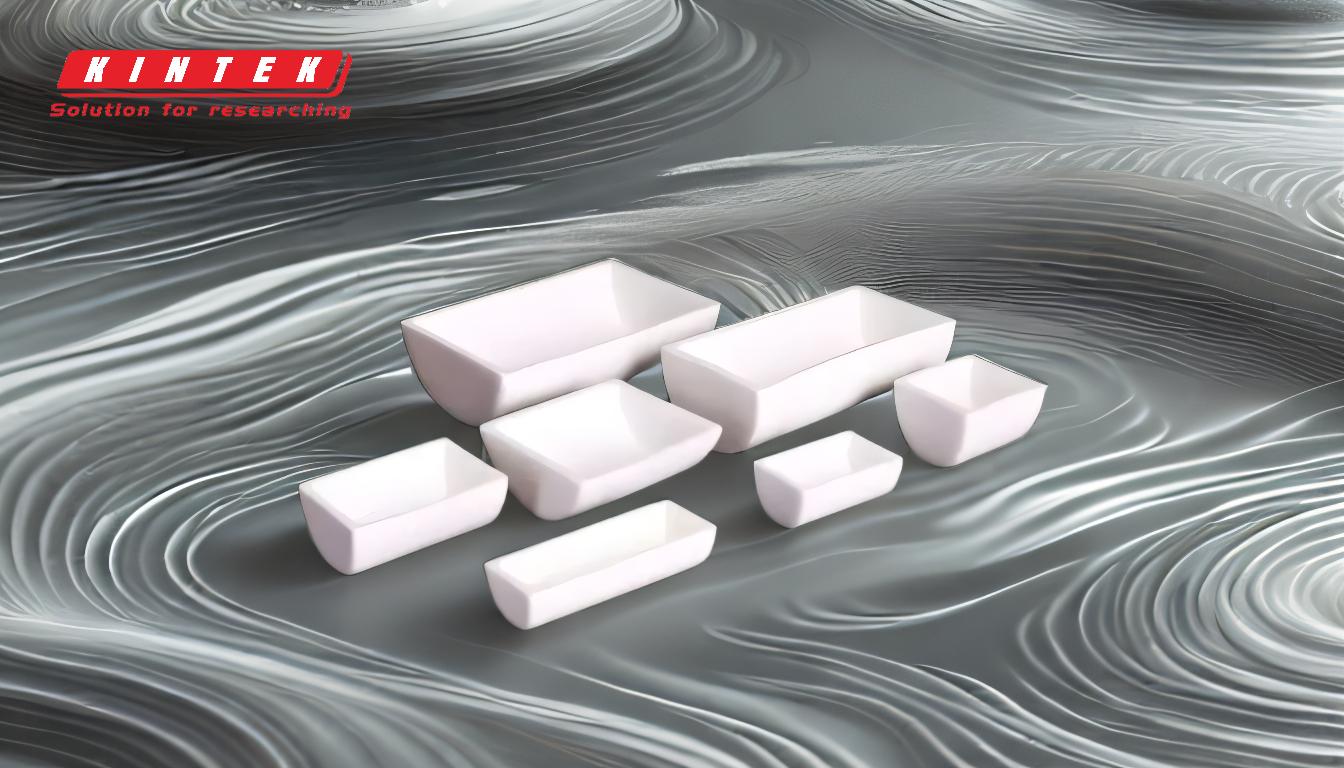
-
Material of the Crucible:
- Graphite Crucibles: These are known for their durability and long service life. They can endure extreme temperatures (exceeding 2000°C) and are resistant to thermal shock, corrosion, and impact. This makes them suitable for high-temperature applications.
- Silicon Carbide Crucibles: These are often used in induction furnaces and their lifespan is influenced by factors such as furnace atmosphere, watt density, and operating temperature. High silicon carbide content is preferred for lower frequency induction furnaces, while higher frequency furnaces may require crucibles with high clay content.
-
Operating Conditions:
- Temperature: The operating temperature and the rate of temperature changes significantly affect the lifespan of a crucible. Rapid heating and cooling can cause thermal shock, which may lead to cracking or other forms of damage.
- Furnace Type and Frequency: The electrical characteristics of the crucible must match the operating frequency of the furnace. Mismatched electrical resistivity can lead to overheating and reduced lifespan.
- Atmosphere: The furnace atmosphere (e.g., oxidizing, reducing, or inert) can affect the crucible's durability. Certain atmospheres may accelerate wear and corrosion.
-
Application-Specific Factors:
- Alloys Being Melted: The type of alloy or range of alloys being melted can influence the crucible's lifespan. Some alloys may be more corrosive or reactive, leading to faster degradation of the crucible.
- Melting and Holding Temperatures: Higher temperatures generally reduce the lifespan of a crucible, especially if the crucible is not designed to handle such extremes.
- Charging and Emptying Methods: How the crucible is charged (e.g., adding cold metal to a hot crucible) and emptied can cause thermal stress, impacting longevity.
- Use of Fluxes and Additives: Certain fluxes or metallurgical additions can be corrosive or reactive, leading to faster wear of the crucible.
-
Maintenance and Usage Patterns:
- Frequency of Maintenance: Regular maintenance, such as cleaning and inspection, can extend the lifespan of a crucible. Neglecting maintenance can lead to premature failure.
- Continuous vs. Intermittent Use: Crucibles used in continuous service may wear out faster than those used intermittently, depending on the operational conditions.
-
Selection and Customization:
- Tailored Selection: Each melting operation is unique, involving specific combinations of furnaces, alloys, and working practices. Therefore, selecting a crucible that is tailored to these specific conditions is crucial for maximizing its lifespan.
- Avoiding Cross-Contamination: In operations where multiple alloys are melted, ensuring that the crucible is not contaminated by previous melts can help maintain its integrity and extend its life.
In summary, the lifespan of a crucible is highly dependent on its material, the specific operating conditions, and how well it is matched to the application. Proper selection, maintenance, and operational practices are key to maximizing its service life.
Summary Table:
Factor | Impact on Crucible Lifespan |
---|---|
Material | - Graphite: High thermal stability, corrosion resistance, and durability. |
- Silicon Carbide: Influenced by furnace atmosphere, watt density, and temperature. | |
Operating Conditions | - Temperature fluctuations and rapid heating/cooling cause thermal shock. |
- Furnace type and frequency must match crucible's electrical resistivity. | |
- Furnace atmosphere (oxidizing, reducing, or inert) affects wear and corrosion. | |
Application-Specific | - Alloys melted: Corrosive or reactive alloys reduce lifespan. |
- Melting/holding temperatures: Higher temperatures shorten lifespan. | |
- Charging/emptying methods: Thermal stress impacts longevity. | |
- Fluxes/additives: Corrosive or reactive substances accelerate wear. | |
Maintenance | - Regular cleaning and inspection extend lifespan. |
- Continuous vs. intermittent use affects wear rate. | |
Selection | - Tailored crucibles for specific furnace and alloy combinations maximize lifespan. |
- Avoid cross-contamination in multi-alloy operations. |
Maximize your crucible's lifespan with expert guidance—contact us today for tailored solutions!