The energy consumption of a lab filter press depends on several factors, including its size, design, operating pressure, and the type of material being processed. Generally, filter presses are designed to be energy-efficient, as they rely on mechanical pressure rather than thermal energy for dewatering. The primary energy consumption comes from the hydraulic system or pneumatic system used to apply pressure, as well as the motor driving the pump for slurry feeding. Smaller lab-scale filter presses typically consume less energy compared to industrial-scale units, often ranging from 0.5 to 2 kW per cycle. However, exact energy usage varies based on operational parameters and the specific model.
Key Points Explained:
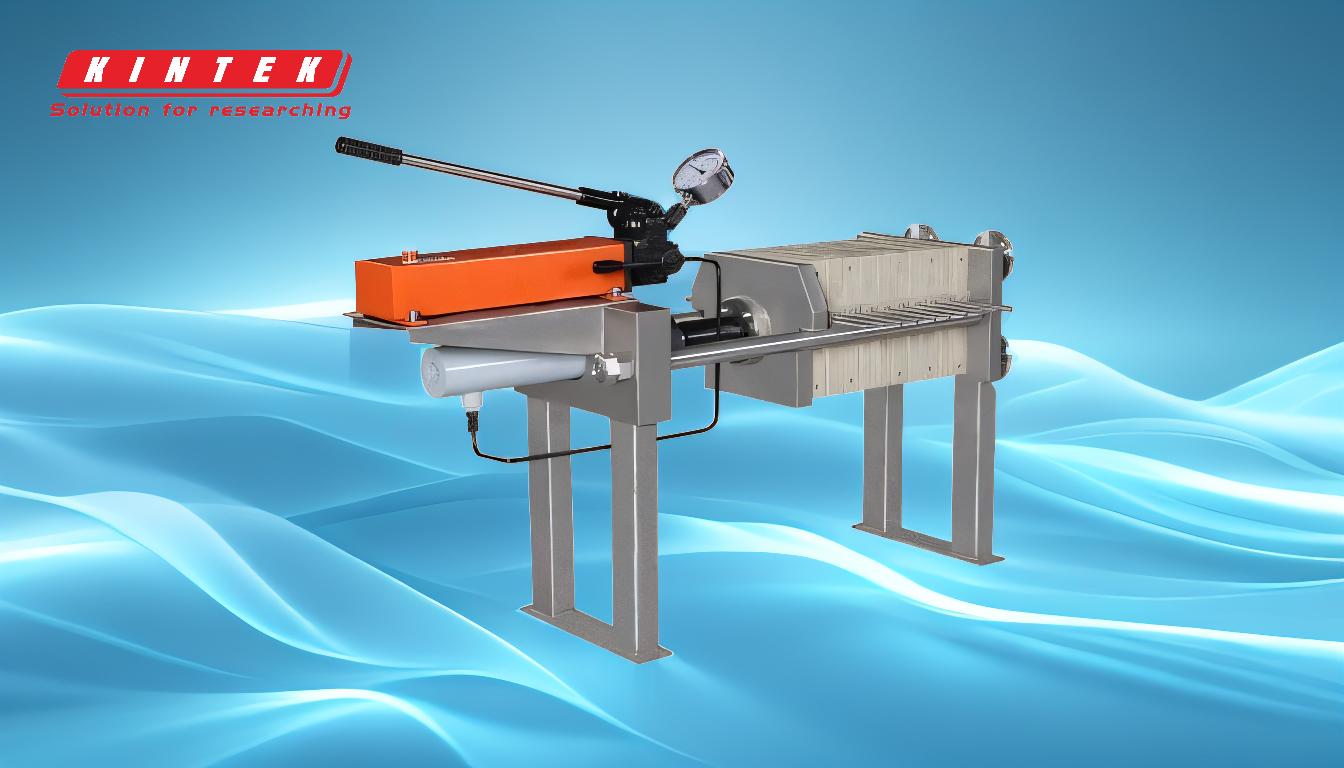
-
Energy Consumption Factors:
- Size and Scale: Lab-scale filter presses are smaller and consume significantly less energy compared to industrial units. A typical lab filter press may use between 0.5 to 2 kW per cycle, whereas industrial units can consume 10 kW or more.
- Operating Pressure: Higher operating pressures require more energy to maintain. Lab filter presses often operate at lower pressures (e.g., 7-15 bar) compared to industrial presses, which can operate at pressures up to 30 bar or higher.
- Hydraulic vs. Pneumatic Systems: Hydraulic systems are more common in larger units and tend to consume more energy due to the need for hydraulic fluid and pumps. Pneumatic systems, often used in smaller lab filter presses, are generally more energy-efficient.
-
Primary Energy Consumers:
- Hydraulic Pump: The hydraulic pump is the main energy consumer in a filter press, as it generates the pressure required for filtration. Energy usage depends on the pump's efficiency and the required pressure.
- Slurry Feed Pump: The motor driving the slurry feed pump also consumes energy, though typically less than the hydraulic system.
- Ancillary Equipment: Additional components like control panels, sensors, and automated plate shifters (if present) contribute marginally to overall energy consumption.
-
Energy Efficiency Features:
- Variable Frequency Drives (VFDs): Modern filter presses often incorporate VFDs to optimize motor speed and reduce energy consumption during low-demand phases.
- Automated Systems: Automated lab filter presses can reduce energy waste by precisely controlling pressure and cycle times, minimizing unnecessary energy use.
- Low-Pressure Operation: Lab-scale units are designed to operate at lower pressures, which inherently reduces energy consumption.
-
Comparative Energy Usage:
- Lab filter presses are generally more energy-efficient than industrial units due to their smaller size and lower operating pressures. For example, a lab filter press processing 10-20 liters of slurry per cycle may consume around 0.5-1 kWh, while an industrial unit processing thousands of liters may consume 10-20 kWh or more per cycle.
-
Operational Considerations:
- Cycle Time: Longer cycle times can increase energy consumption, especially if the hydraulic pump runs continuously. Optimizing cycle times can help reduce energy usage.
- Material Characteristics: The viscosity and solids content of the slurry affect the energy required for filtration. Thicker slurries with higher solids content may require more energy to process.
-
Environmental and Cost Impact:
- Lab filter presses are designed with energy efficiency in mind, making them suitable for environmentally conscious applications. Their lower energy consumption also translates to reduced operational costs, which is particularly beneficial for labs with high throughput requirements.
By understanding these factors, users can make informed decisions about the energy requirements of a lab filter press and optimize its operation for efficiency and cost-effectiveness.
Summary Table:
Factor | Impact on Energy Consumption |
---|---|
Size and Scale | Lab-scale units (0.5-2 kW/cycle) consume less energy than industrial units (10+ kW/cycle). |
Operating Pressure | Higher pressures (e.g., 30 bar) increase energy use; lab presses operate at lower pressures. |
Hydraulic vs. Pneumatic | Hydraulic systems consume more energy; pneumatic systems are more efficient for small units. |
Primary Consumers | Hydraulic pump (main consumer), slurry feed pump, and ancillary equipment contribute marginally. |
Efficiency Features | VFDs, automated systems, and low-pressure operation reduce energy waste. |
Cycle Time | Longer cycles increase energy use; optimizing cycle times improves efficiency. |
Material Characteristics | Thicker slurries with higher solids content require more energy to process. |
Want to optimize your lab filter press for energy efficiency? Contact our experts today for tailored solutions!