PVD (Physical Vapor Deposition) coatings are thin film coatings typically ranging from 0.25 microns to 5 microns in thickness. These coatings are applied at relatively low temperatures and require high cleaning standards to ensure optimal adhesion and performance. The thinness of PVD coatings allows them to enhance properties such as hardness, smoothness, and corrosion resistance without significantly altering the appearance or dimensions of the substrate. The thickness range ensures that the coatings do not interfere with the specifications of engineered parts while providing durability and resistance to wear, corrosion, and oxidation. The performance of PVD coatings is influenced by the substrate material, deposition method, and specific application requirements.
Key Points Explained:
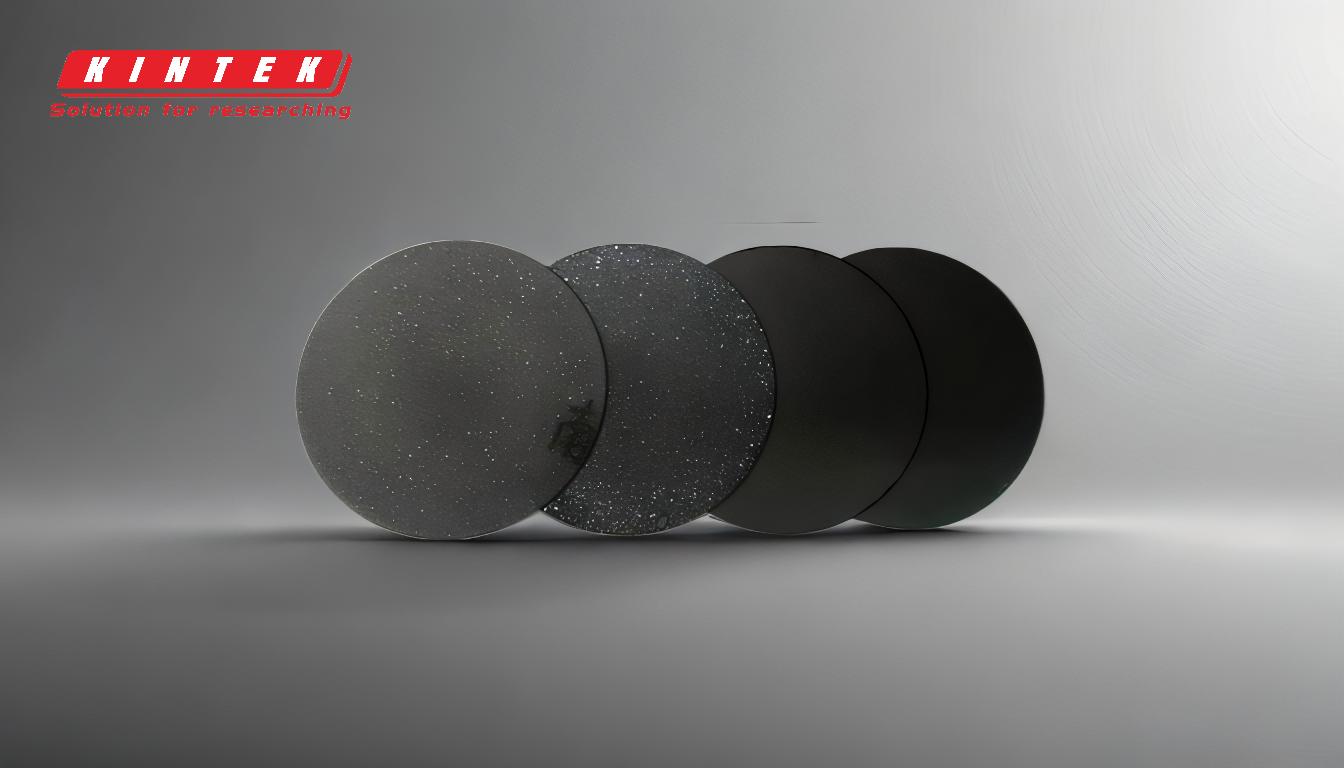
-
Typical Thickness Range of PVD Coatings:
- PVD coatings generally range from 0.25 microns to 5 microns in thickness.
- This thinness ensures that the coatings do not alter the dimensions or appearance of the substrate, making them ideal for precision-engineered parts.
-
Benefits of Thin PVD Coatings:
- Enhanced Surface Properties: The thin film improves hardness, smoothness, and corrosion resistance.
- Minimal Impact on Substrate: The coatings do not change the material's appearance or dimensions, making them suitable for applications requiring tight tolerances.
- Replication of Original Finish: PVD coatings can replicate the original surface finish of materials with minimal effort.
-
Factors Influencing Coating Thickness:
- Substrate Material: The properties of the underlying material, such as its composition and surface condition, influence the adhesion and performance of the coating.
- Deposition Method: The specific PVD process used (e.g., sputtering, evaporation) affects the coating's thickness, uniformity, and properties.
- Application Requirements: The desired performance characteristics (e.g., wear resistance, corrosion resistance) determine the optimal thickness.
-
Performance Characteristics of PVD Coatings:
- Hardness and Durability: PVD coatings are often harder and more durable than coatings applied by other methods, such as electroplating.
- Corrosion and Oxidation Resistance: The coatings provide excellent resistance to environmental degradation.
- Abrasion Resistance: PVD coatings are highly resistant to wear, making them suitable for high-stress applications.
-
Limitations of PVD Coatings:
- Thickness Constraints: The maximum thickness is typically limited to 5 microns, which may not be suitable for applications requiring thicker coatings.
- Uniformity Challenges: Achieving uniform coating thickness on complex geometries, such as the back and sides of tools, can be difficult due to the line-of-sight nature of PVD processes.
-
Applications of PVD Coatings:
- Tooling and Cutting Tools: PVD coatings enhance the performance and lifespan of tools by improving wear resistance and reducing friction.
- Aerospace and Automotive Components: The coatings provide corrosion resistance and durability for critical components.
- Decorative Finishes: PVD coatings are used to create aesthetically pleasing, durable finishes on consumer products.
In summary, PVD coatings are highly versatile and effective for enhancing the performance of various materials and components. Their thinness, combined with excellent adhesion and durability, makes them a preferred choice for applications requiring precision and reliability. However, their thickness limitations and challenges in coating complex geometries should be considered when selecting PVD for specific applications.
Summary Table:
Aspect | Details |
---|---|
Thickness Range | 0.25 to 5 microns |
Key Benefits | Improved hardness, smoothness, corrosion resistance, minimal substrate impact |
Influencing Factors | Substrate material, deposition method, application requirements |
Performance | High hardness, corrosion resistance, wear resistance |
Limitations | Max thickness of 5 microns, challenges with complex geometries |
Applications | Tooling, aerospace, automotive, decorative finishes |
Learn how PVD coatings can elevate your project's performance—contact our experts today!