Chemical vapor deposition (CVD) is a versatile process used to deposit thin films of materials onto substrates through the reaction of gaseous precursors. The thickness of CVD coatings can vary significantly depending on the application, ranging from nanometers to micrometers. The process involves several key components, including gas delivery systems, reaction chambers, and energy sources, which work together to ensure precise control over the deposition process. CVD coatings are widely used to enhance the electrical, mechanical, optical, thermal, and corrosion resistance properties of substrates, making them essential in industries such as semiconductors, optics, and protective coatings.
Key Points Explained:
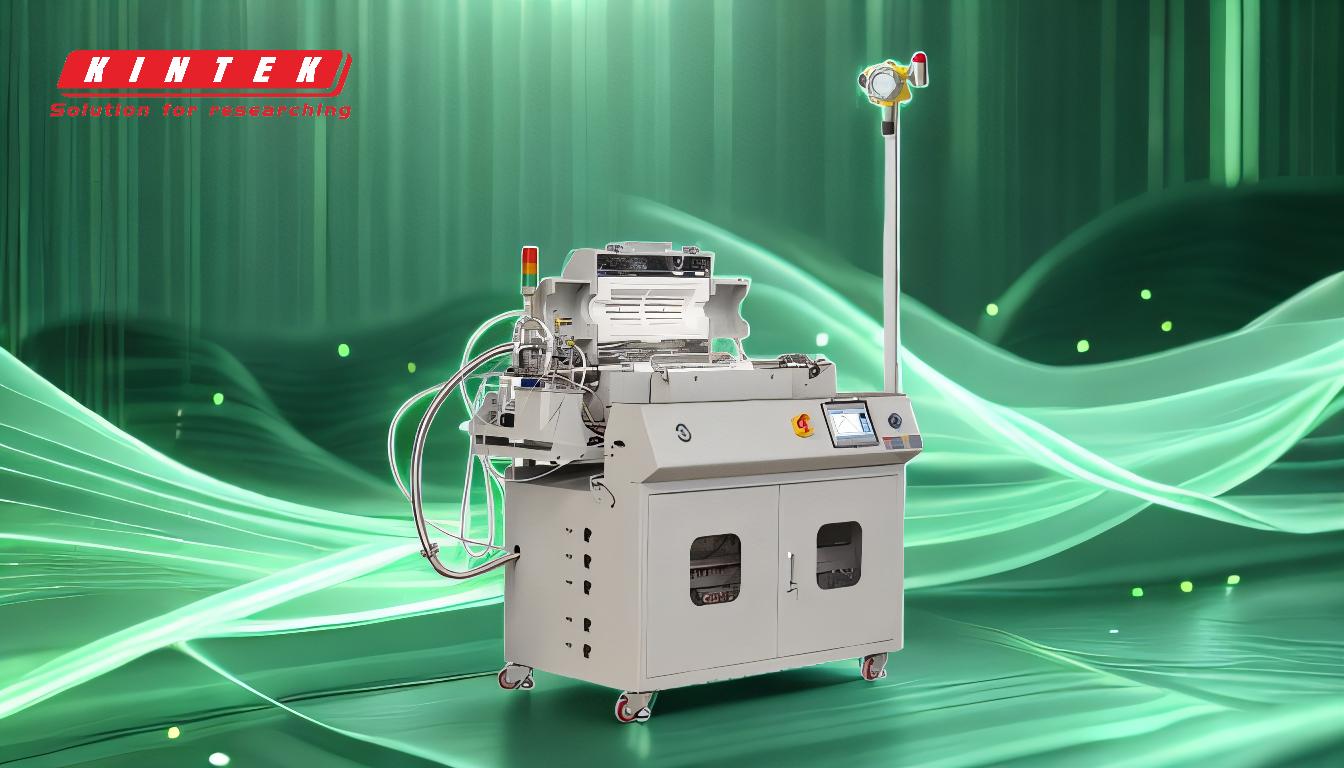
-
Definition and Purpose of CVD:
- Chemical vapor deposition (CVD) is a process where solid materials are deposited onto a substrate through the reaction of gaseous precursors. This method is used to create thin films with specific properties, such as improved electrical conductivity, mechanical strength, or corrosion resistance. The thickness of these films can range from a few nanometers to several micrometers, depending on the application.
-
Factors Influencing CVD Thickness:
- Precursor Gases: The type and concentration of precursor gases used in the CVD process can significantly affect the thickness of the deposited film. Different gases react at varying rates, leading to differences in deposition rates.
- Temperature and Pressure: The temperature and pressure within the reaction chamber play a crucial role in determining the thickness of the CVD coating. Higher temperatures and pressures generally increase the deposition rate, resulting in thicker films.
- Reaction Time: The duration of the CVD process directly impacts the thickness of the coating. Longer reaction times allow more material to be deposited, increasing the overall thickness.
-
Applications and Thickness Requirements:
- Semiconductors: In the semiconductor industry, CVD is used to deposit thin films of materials like silicon dioxide and silicon nitride, typically ranging from a few nanometers to a few micrometers in thickness. These films are crucial for insulating layers, gate dielectrics, and passivation layers.
- Optical Coatings: CVD is also used to create optical coatings, such as anti-reflective coatings on lenses. These coatings are usually very thin, often in the range of tens to hundreds of nanometers, to achieve the desired optical properties.
- Protective Coatings: For protective coatings, such as those used to enhance corrosion resistance, the thickness can vary more widely. Depending on the substrate and the environment it will be exposed to, coatings can range from a few micrometers to tens of micrometers.
-
Equipment and Process Control:
- Gas Delivery System: The gas delivery system ensures that the precursor gases are introduced into the reaction chamber in a controlled manner. This system is critical for maintaining consistent deposition rates and, consequently, uniform film thickness.
- Reaction Chamber: The reaction chamber, or reactor, is where the actual deposition takes place. The design of the chamber, including its size and shape, can influence the uniformity and thickness of the deposited film.
- Energy Source: The energy source, often in the form of heat or plasma, provides the energy needed for the chemical reactions to occur. The intensity and distribution of this energy can affect the deposition rate and film thickness.
- Vacuum System: A vacuum system is used to control the pressure within the reaction chamber. Lower pressures can lead to thinner, more uniform films, while higher pressures may result in thicker, less uniform coatings.
- Process Automatic Control System: This system monitors and controls various parameters, such as temperature, pressure, and gas flow rates, to ensure consistent deposition and desired film thickness.
- Exhaust Gas Treatment System: After the deposition process, the exhaust gases are treated to remove any harmful byproducts, ensuring that the process is environmentally friendly.
-
Challenges and Considerations:
- Uniformity: Achieving uniform thickness across the entire substrate can be challenging, especially for large or complex shapes. Variations in gas flow, temperature, and pressure can lead to uneven deposition.
- Adhesion: The adhesion of the deposited film to the substrate is critical for the performance of the coating. Poor adhesion can lead to delamination and failure of the coating.
- Defects: Defects such as pinholes, cracks, or impurities can affect the quality and thickness of the CVD coating. Careful control of process parameters is necessary to minimize these defects.
In summary, the thickness of chemical vapor deposition coatings can vary widely depending on the application, with typical thicknesses ranging from nanometers to micrometers. The process involves precise control of various parameters, including precursor gases, temperature, pressure, and reaction time, to achieve the desired film properties. CVD is a critical technology in industries such as semiconductors, optics, and protective coatings, where it is used to enhance the performance of materials through the deposition of thin films.
Summary Table:
Aspect | Details |
---|---|
Typical Thickness | Nanometers to micrometers, depending on application. |
Key Influencing Factors | Precursor gases, temperature, pressure, and reaction time. |
Applications | Semiconductors, optical coatings, and protective coatings. |
Equipment | Gas delivery system, reaction chamber, energy source, and vacuum system. |
Challenges | Uniformity, adhesion, and defect control. |
Discover how CVD coatings can enhance your materials—contact our experts today for tailored solutions!