Thermal evaporation coating thickness typically ranges from a few nanometers to several micrometers, depending on the application and process parameters. The thickness is controlled by adjusting factors such as the temperature of the evaporant, the deposition rate, and the distance between the evaporant and the substrate. The process is influenced by the purity of the source material, vacuum conditions, and substrate preparation. Achieving the desired thickness and uniformity requires precise control over these variables to ensure high-quality thin films with optimal performance.
Key Points Explained:
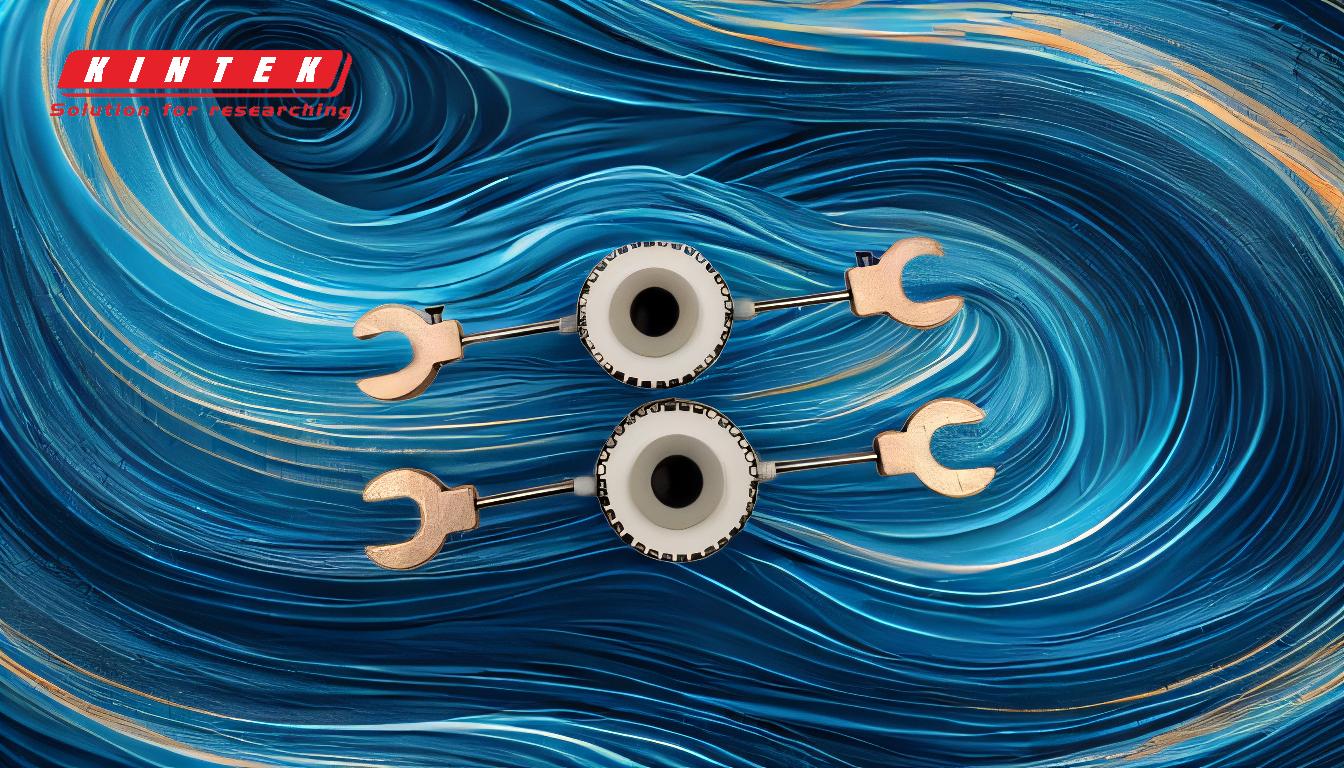
-
Typical Thickness Range:
- Thermal evaporation coatings generally range from a few nanometers to several micrometers.
- The exact thickness depends on the specific application and the desired properties of the thin film.
-
Factors Influencing Thickness:
- Temperature of the Evaporant: Higher temperatures increase the evaporation rate, potentially leading to thicker coatings.
- Deposition Rate: Controlling the rate at which material is deposited onto the substrate directly affects the final thickness.
- Distance Between Evaporant and Substrate: A shorter distance can result in a more uniform and potentially thicker coating.
-
Impact of Source Material Purity:
- The purity of the source material is crucial for achieving high-quality coatings.
- Impurities can affect the uniformity and properties of the thin film.
-
Vacuum Conditions:
- Higher vacuum levels improve the free path of source material molecules, reducing impurities and enhancing film quality.
- Proper vacuum conditions are essential for controlling the deposition process and achieving the desired thickness.
-
Substrate Preparation:
- The surface condition of the substrate plays a significant role in the uniformity and adhesion of the coating.
- A rough substrate surface may lead to non-uniform deposition, affecting the overall thickness and quality of the film.
-
Control of Process Parameters:
- Precise control over temperature, deposition rate, and distance is necessary to achieve the desired thickness and uniformity.
- Monitoring and adjusting these parameters during the deposition process ensures consistent and high-quality results.
-
Application-Specific Considerations:
- Different applications may require specific thicknesses to achieve optimal performance.
- Understanding the requirements of the application helps in selecting the appropriate process parameters and materials.
By carefully managing these factors, it is possible to produce thermal evaporation coatings with the desired thickness and properties, ensuring high performance and reliability in various applications.
Summary Table:
Key Factor | Impact on Coating Thickness |
---|---|
Typical Thickness Range | Few nanometers to several micrometers, depending on application and process parameters. |
Temperature of Evaporant | Higher temperatures increase evaporation rate, potentially leading to thicker coatings. |
Deposition Rate | Directly affects final thickness; controlled rate ensures desired coating thickness. |
Distance to Substrate | Shorter distance can result in more uniform and potentially thicker coatings. |
Source Material Purity | High purity ensures uniform and high-quality coatings; impurities can degrade film quality. |
Vacuum Conditions | Higher vacuum levels reduce impurities and enhance film quality, ensuring precise thickness. |
Substrate Preparation | Smooth surfaces improve uniformity and adhesion; rough surfaces may lead to non-uniform films. |
Process Control | Precise control of temperature, deposition rate, and distance ensures consistent results. |
Application Needs | Specific thicknesses are required for optimal performance in different applications. |
Need precise thermal evaporation coatings for your application? Contact us today to learn more!