Vacuum deposition is a versatile technique used to deposit thin films or coatings on surfaces in a controlled environment, typically under vacuum conditions. The thickness of the deposited layer can vary significantly, ranging from a single atomic layer (nanometers) to several millimeters, depending on the specific process, materials, and parameters involved. Factors such as the duration of the process, energy levels, material properties, and environmental conditions (e.g., vacuum pressure, temperature) play critical roles in determining the final thickness and quality of the deposited film. This technique is widely used in industries requiring precise control over film properties, such as electronics, optics, and coatings.
Key Points Explained:
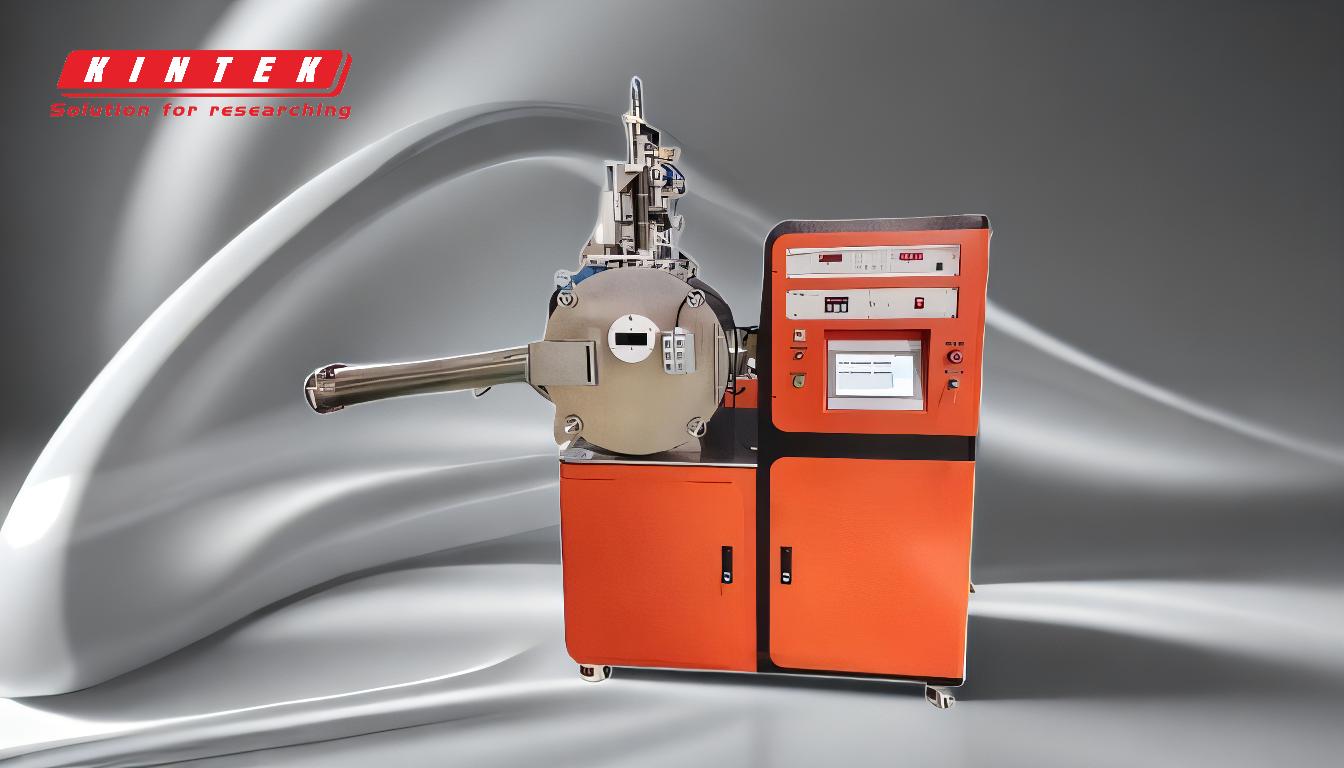
-
Range of Thickness in Vacuum Deposition:
- Vacuum deposition can produce films with thicknesses ranging from a single atomic layer (nanometer scale) to several millimeters.
- For example:
- Atomic/Molecular Scale: In processes like physical vapor deposition (PVD) or low-pressure chemical vapor deposition (LPCVD), layers are deposited atom-by-atom or molecule-by-molecule, resulting in extremely thin films (nanometers).
- Macroscopic Scale: In some applications, such as protective coatings or decorative finishes, thicker layers (micrometers to millimeters) may be deposited.
-
Factors Influencing Thickness:
- The thickness of the deposited film is influenced by several key factors:
- Process Duration: Longer deposition times generally result in thicker films.
- Energy Levels: Higher energy levels of coating particles (e.g., tens to thousands of electron volts in sputtering) can increase deposition rates and affect thickness.
- Material Properties: The mass and molecular weight of the source material influence how quickly it evaporates or sputters, impacting thickness.
- Vacuum Pressure: A higher degree of vacuum improves the free path of source material molecules, leading to more uniform and controlled deposition.
- Substrate Preparation: The surface roughness and cleanliness of the substrate can affect the uniformity and adhesion of the deposited film.
- The thickness of the deposited film is influenced by several key factors:
-
Process-Specific Considerations:
- Sputtering: The thickness of the deposited metal in sputtering depends on the cycle time and the power applied to the target. Higher power and longer cycles result in thicker films.
- Thermal Evaporation: In this process, the evaporation rate of the source material, along with vacuum pressure and substrate rotation speed, determines the thickness and uniformity of the film.
- Chemical Vapor Deposition (CVD): In LPCVD, the deposition rate and thickness are influenced by the chemical reactions occurring at the substrate surface, as well as temperature and pressure conditions.
-
Quality and Performance of Thin Films:
- The quality of the deposited film is critical for its performance in applications. Key factors affecting quality include:
- Purity of Source Material: Impurities can lead to defects in the film.
- Deposition Temperature and Pressure: Proper control ensures uniform and high-quality films.
- Substrate Surface Preparation: A smooth and clean substrate surface promotes uniform deposition and strong adhesion.
- The quality of the deposited film is critical for its performance in applications. Key factors affecting quality include:
-
Applications and Implications:
- Vacuum deposition is used in a wide range of industries, including:
- Electronics: For creating thin-film transistors, semiconductor devices, and conductive layers.
- Optics: For anti-reflective coatings, mirrors, and optical filters.
- Coatings: For wear-resistant, corrosion-resistant, and decorative finishes.
- The ability to control film thickness at the atomic level makes vacuum deposition a critical technology for advanced manufacturing and research.
- Vacuum deposition is used in a wide range of industries, including:
By understanding these key points, equipment and consumable purchasers can make informed decisions about the materials and processes needed to achieve specific film thicknesses and properties for their applications.
Summary Table:
Aspect | Details |
---|---|
Thickness Range | Nanometers (atomic scale) to millimeters (macroscopic scale) |
Key Factors | Process duration, energy levels, material properties, vacuum pressure, substrate preparation |
Process Examples | Sputtering, Thermal Evaporation, Chemical Vapor Deposition (CVD) |
Applications | Electronics (transistors, semiconductors), Optics (mirrors, filters), Coatings (wear-resistant, decorative) |
Need precise vacuum deposition solutions? Contact our experts today to discuss your requirements!