The ideal coating thickness depends on the type of coating, the application, and the desired performance. For powder coatings, manufacturers typically recommend a thickness range of 2 to 8 mils (50 to 200 microns) to ensure optimal durability, corrosion resistance, and aesthetic finish. However, for other types of coatings, such as thin-film coatings, the thickness can be much lower, ranging from 0.25 to 5 microns. The specific thickness required depends on factors like the substrate material, environmental conditions, and functional requirements of the coated item.
Key Points Explained:
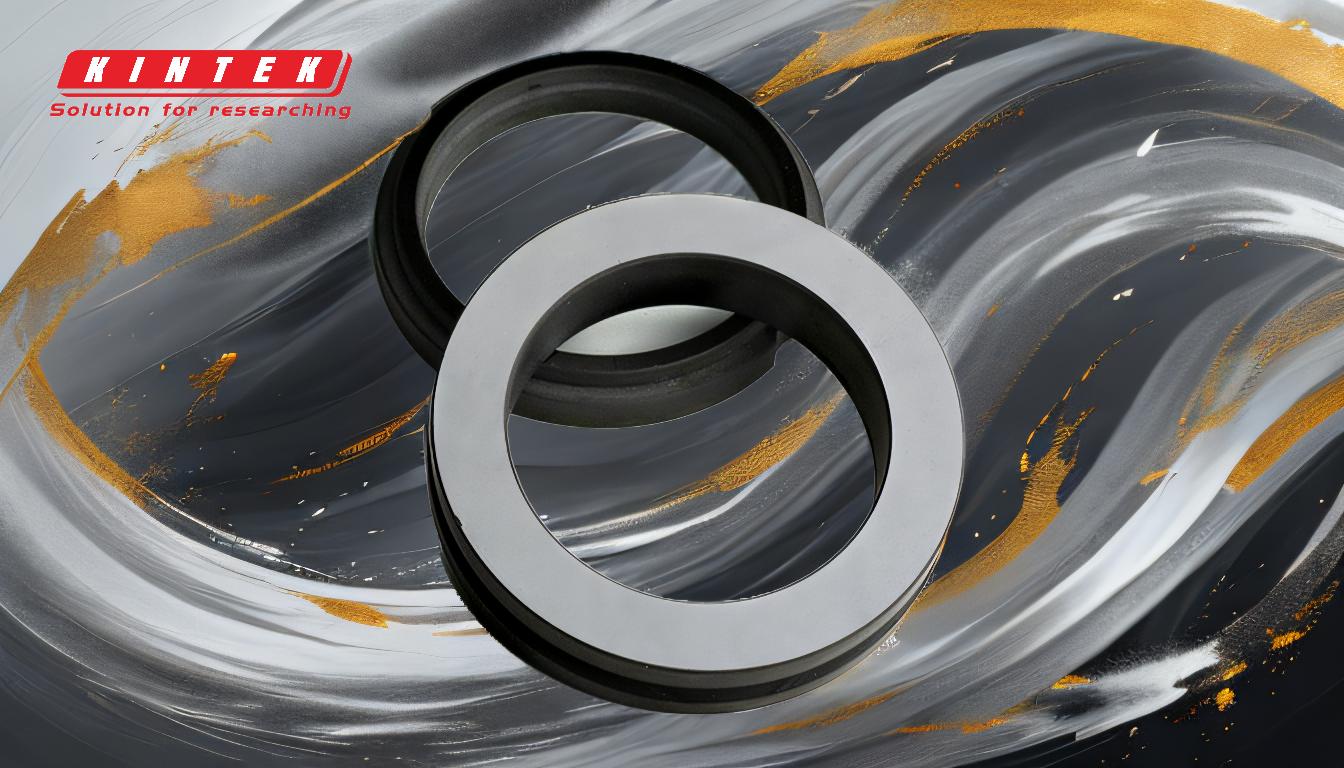
-
Powder Coating Thickness Recommendations:
- Powder coating manufacturers generally recommend a thickness range of 2 to 8 mils (50 to 200 microns) for optimal performance.
- This range ensures:
- Durability: Adequate thickness prevents chipping, cracking, and wear over time.
- Corrosion Resistance: Thicker coatings provide better protection against rust and environmental damage.
- Aesthetic Finish: Proper thickness ensures an even, smooth surface with no defects like orange peel or pinholes.
-
Thin-Film Coating Thickness:
- For thin-film coatings, such as those used in electronics or optical applications, the thickness is much lower, typically ranging from 0.25 to 5 microns.
- These coatings are designed for specific functions like:
- Electrical Insulation: Thin coatings can provide insulation without adding bulk.
- Optical Clarity: Ultra-thin coatings maintain transparency and light transmission.
- Wear Resistance: Even at low thicknesses, these coatings can enhance surface hardness and reduce friction.
-
Factors Influencing Coating Thickness:
- Substrate Material: Different materials (e.g., metal, plastic, wood) require different coating thicknesses to adhere properly and perform well.
- Environmental Conditions: Harsh environments (e.g., high humidity, UV exposure) may necessitate thicker coatings for added protection.
- Functional Requirements: The intended use of the coated item (e.g., decorative, structural, or functional) dictates the necessary thickness.
- Application Method: Techniques like spray coating, dip coating, or electrostatic deposition can influence the achievable thickness.
-
Importance of Adhering to Recommended Thickness:
- Too Thin: Coatings below the recommended range may fail to provide adequate protection, leading to premature failure, poor adhesion, or insufficient coverage.
- Too Thick: Excessive thickness can cause issues like cracking, peeling, or uneven curing, especially in powder coatings. It may also increase material costs unnecessarily.
-
Measuring Coating Thickness:
- Tools like coating thickness gauges (e.g., magnetic, eddy current, or ultrasonic) are used to ensure the coating meets specified requirements.
- Regular quality control checks during and after the coating process help maintain consistency and performance.
By understanding these key points, purchasers and applicators can make informed decisions about coating thickness to achieve the desired balance of performance, durability, and cost-effectiveness.
Summary Table:
Coating Type | Thickness Range | Key Benefits |
---|---|---|
Powder Coating | 2 to 8 mils (50-200 µm) | Durability, corrosion resistance, smooth finish, and aesthetic appeal. |
Thin-Film Coating | 0.25 to 5 microns | Electrical insulation, optical clarity, wear resistance, and reduced friction. |
Factors to Consider | Substrate material, environmental conditions, functional needs, application method. |
Need help determining the right coating thickness for your project? Contact our experts today!