To determine the deposition rate, it is essential to understand the relationship between the thickness of the deposited film and the time taken for deposition. The deposition rate is calculated as the thickness of the film divided by the deposition time (C = T/t). However, this simple formula is influenced by various factors, including the properties of the target material, deposition technique, process parameters (such as power, temperature, and target-substrate distance), and the characteristics of the plasma or precursor flux. Selecting the appropriate deposition method and optimizing process conditions are critical to achieving the desired deposition rate and film quality. Below, the key factors and considerations for determining and optimizing deposition rates are explained in detail.
Key Points Explained:
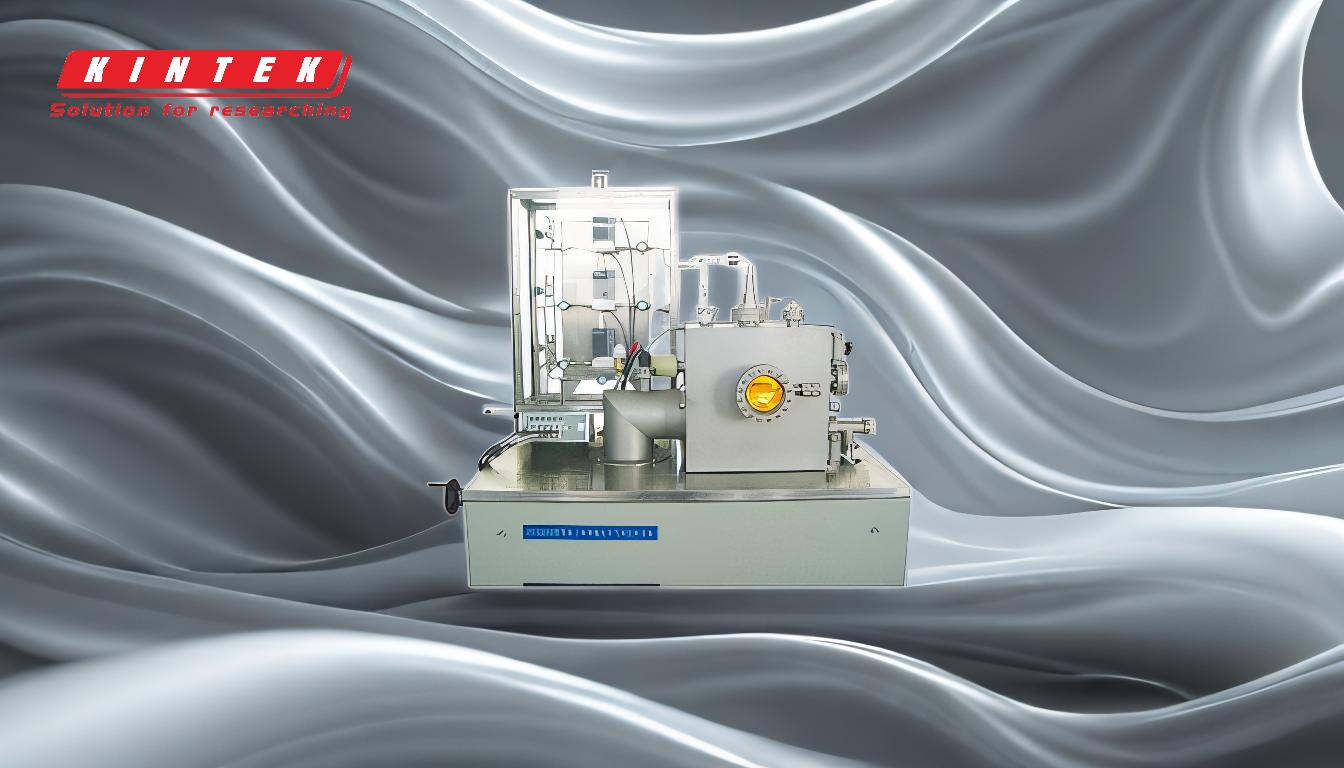
-
Basic Formula for Deposition Rate
- The deposition rate (C) is calculated using the formula:
[ C = \frac{T}{t} ]
where ( T ) is the thickness of the deposited film and ( t ) is the deposition time. - This formula provides a straightforward way to measure the rate at which material is deposited onto a substrate.
- Example: If a 100 nm film is deposited in 10 minutes, the deposition rate is 10 nm/min.
- The deposition rate (C) is calculated using the formula:
-
Factors Influencing Deposition Rate
- Target Material Properties: The physical and chemical properties of the target material, such as sputtering yield and melting point, significantly affect the deposition rate.
-
Process Parameters:
- Power and Temperature: Higher power and temperature generally increase the deposition rate by enhancing the energy of the sputtered particles or the reactivity of the precursor molecules.
- Target-Substrate Distance: A shorter distance between the target and substrate increases the deposition rate due to reduced scattering of particles.
- Plasma Characteristics: In plasma-based deposition methods, factors like plasma temperature, composition, and density influence the deposition rate.
- Precursor Flux: In chemical vapor deposition (CVD), the flux of precursor molecules to the substrate surface, controlled by fluid flow or diffusion, determines the deposition rate.
-
Importance of Deposition Technique
- The choice of deposition technique (e.g., physical vapor deposition (PVD) or chemical vapor deposition (CVD)) depends on the application, target material, and desired film properties.
- PVD techniques, such as sputtering, are suitable for producing high-purity films with precise thickness control.
- CVD techniques are ideal for depositing complex materials and achieving high conformality on intricate substrates.
-
Uniformity and Erosion Zone
- The size of the erosion zone on the target material affects the deposition rate and film uniformity.
- A larger erosion zone increases the deposition rate but may reduce thickness uniformity.
- Optimizing the target-substrate distance and erosion zone size is crucial for achieving a balance between deposition rate and film quality.
-
Monitoring and Control
- Monitoring the elemental composition in the deposition chamber ensures the desired material composition and prevents contamination.
- Controlling factors like substrate surface temperature, precursor flux, and the presence of impurities is essential for achieving consistent deposition rates and high-quality films.
-
Application-Specific Considerations
- The deposition rate must be selected based on the application requirements, such as the desired film thickness, substrate material, and intended use (e.g., corrosion resistance, thermal conductivity).
- Balancing deposition speed with precise thickness control is critical for applications requiring high-performance coatings.
By understanding these factors and optimizing the deposition process, one can accurately determine and control the deposition rate to meet specific application needs.
Summary Table:
Key Factor | Influence on Deposition Rate |
---|---|
Basic Formula | C = T/t (Thickness ÷ Deposition Time) |
Target Material Properties | Sputtering yield, melting point, and chemical properties affect deposition rate. |
Process Parameters | Power, temperature, and target-substrate distance impact particle energy and deposition speed. |
Deposition Technique | PVD (e.g., sputtering) for high-purity films; CVD for complex materials and conformality. |
Uniformity & Erosion Zone | Larger erosion zones increase rate but may reduce film uniformity. |
Monitoring & Control | Monitor elemental composition, substrate temperature, and precursor flux for consistent rates. |
Application-Specific Needs | Select rate based on film thickness, substrate material, and intended use. |
Need help optimizing your deposition process? Contact our experts today for tailored solutions!