Mixing rubber compounds is a critical step in rubber manufacturing, involving the blending of raw rubber with various compounding agents to achieve desired properties. The process can be performed using two primary methods: open-mill mixing and internal mixer mixing. Open-mill mixing is simple and suitable for small batches, while internal mixer mixing offers better control, efficiency, and scalability for larger batches. The internal mixer uses rotating rotors to shear and rub the material, increasing temperature and reducing viscosity, which ensures uniform dispersion of compounding agents. After mixing, additional processes like extrusion, rolling, and vulcanization are used to shape and cure the rubber into finished products.
Key Points Explained:
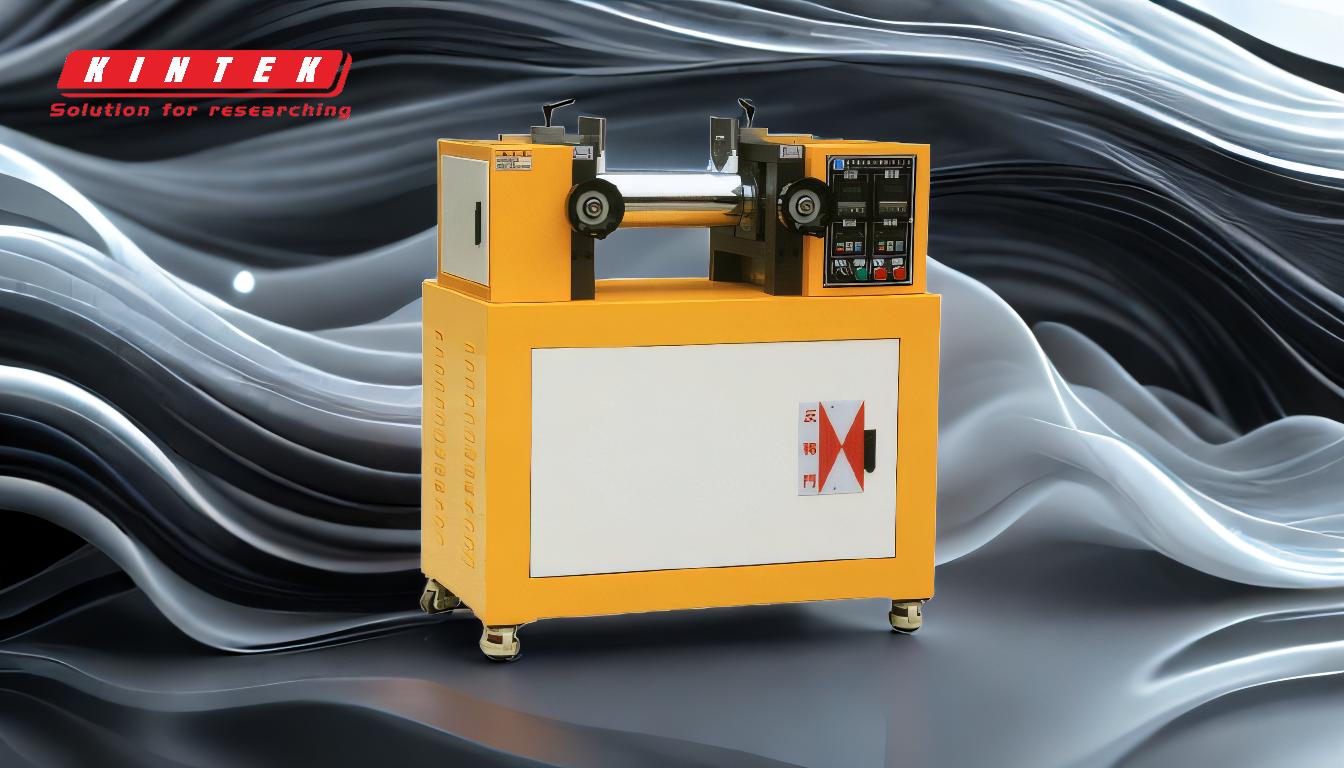
-
Methods of Mixing Rubber Compounds:
-
Open-Mill Mixing:
- This method uses a two-roll laboratory mill, where the rubber is passed through rotating rolls to mix and homogenize the material.
- It is simple, cost-effective, and ideal for small batch sizes or laboratory-scale operations.
- However, it requires manual intervention, is slower, and less efficient for large-scale production.
-
Internal Mixer Mixing:
- This method employs an internal mixer, such as a Banbury mixer, which uses rotating rotors to shear and mix the rubber and compounding agents.
- It is faster, more efficient, and suitable for large-scale production.
- The process generates heat, reducing the rubber's viscosity and improving the dispersion of additives.
-
Open-Mill Mixing:
-
Internal Mixer Mechanism:
- The internal mixer consists of two rotors that rotate in opposite directions, creating shear forces that mix the rubber and compounding agents.
- As the material is sheared, its temperature rises, which decreases viscosity and enhances the wettability of the rubber on the compounding agents.
- This ensures thorough contact and uniform dispersion of additives, resulting in a homogeneous rubber compound.
-
Temperature Control in Mixing:
- The rise in temperature during mixing is a critical factor. It softens the rubber, making it easier to mix and ensuring better incorporation of additives.
- However, excessive heat can degrade the rubber or cause premature vulcanization (scorch), so temperature control is essential.
-
Compounding Agents and Their Role:
- Compounding agents include fillers (e.g., carbon black), plasticizers, curing agents (e.g., sulfur), accelerators, and antioxidants.
- These agents modify the rubber's properties, such as strength, elasticity, durability, and resistance to heat, chemicals, and aging.
-
Post-Mixing Processes:
- After mixing, the rubber compound undergoes additional shaping and curing processes:
- Extrusion: The rubber is forced through a die to create specific shapes, such as tubes or profiles.
- Die-Cut Sheet Rolling: The rubber is rolled into sheets and cut into desired shapes.
- Open Vulcanization: The rubber is cured in open molds or presses to achieve its final properties.
- Continuous Vulcanization: The rubber is cured continuously, often used for products like cables or hoses.
- After mixing, the rubber compound undergoes additional shaping and curing processes:
-
Advantages of Internal Mixer Mixing:
- Efficiency: Faster mixing times and larger batch sizes compared to open-mill mixing.
- Consistency: Better control over temperature and mixing parameters ensures uniform dispersion of additives.
- Scalability: Suitable for industrial-scale production.
-
Considerations for Equipment Selection:
- Batch Size: Open-mill mixing is better for small batches, while internal mixers are ideal for large-scale production.
- Material Properties: Some rubber compounds may require specific mixing conditions, such as low-temperature mixing to avoid scorch.
- Cost and Maintenance: Internal mixers are more expensive and require regular maintenance, but they offer long-term efficiency gains.
-
Safety and Environmental Considerations:
- Proper ventilation and temperature control are necessary to prevent overheating and release of harmful fumes.
- Waste management and recycling of rubber scraps should be considered to minimize environmental impact.
By understanding these key points, manufacturers can choose the appropriate mixing method and optimize the process to produce high-quality rubber compounds tailored to specific applications.
Summary Table:
Aspect | Open-Mill Mixing | Internal Mixer Mixing |
---|---|---|
Batch Size | Small batches | Large-scale production |
Efficiency | Slower, manual intervention | Faster, automated |
Temperature Control | Less precise | Better control |
Cost | Lower initial cost | Higher initial cost |
Applications | Lab-scale or small production | Industrial-scale production |
Need help choosing the right rubber mixing method? Contact our experts today for tailored solutions!