Atomic Layer Deposition (ALD) is a specialized subset of Chemical Vapor Deposition (CVD). While both techniques involve chemical reactions to deposit thin films, ALD distinguishes itself through its unique self-limiting, layer-by-layer deposition process. This method allows for atomic-level precision in film thickness, uniformity, and conformality, making it ideal for applications requiring ultra-thin films (10-50 nm) and high-aspect ratio structures. CVD, on the other hand, is better suited for thicker films and higher deposition rates due to its continuous reaction process. ALD's sequential precursor introduction and precise control over deposition conditions set it apart as a distinct yet related technique within the broader CVD family.
Key Points Explained:
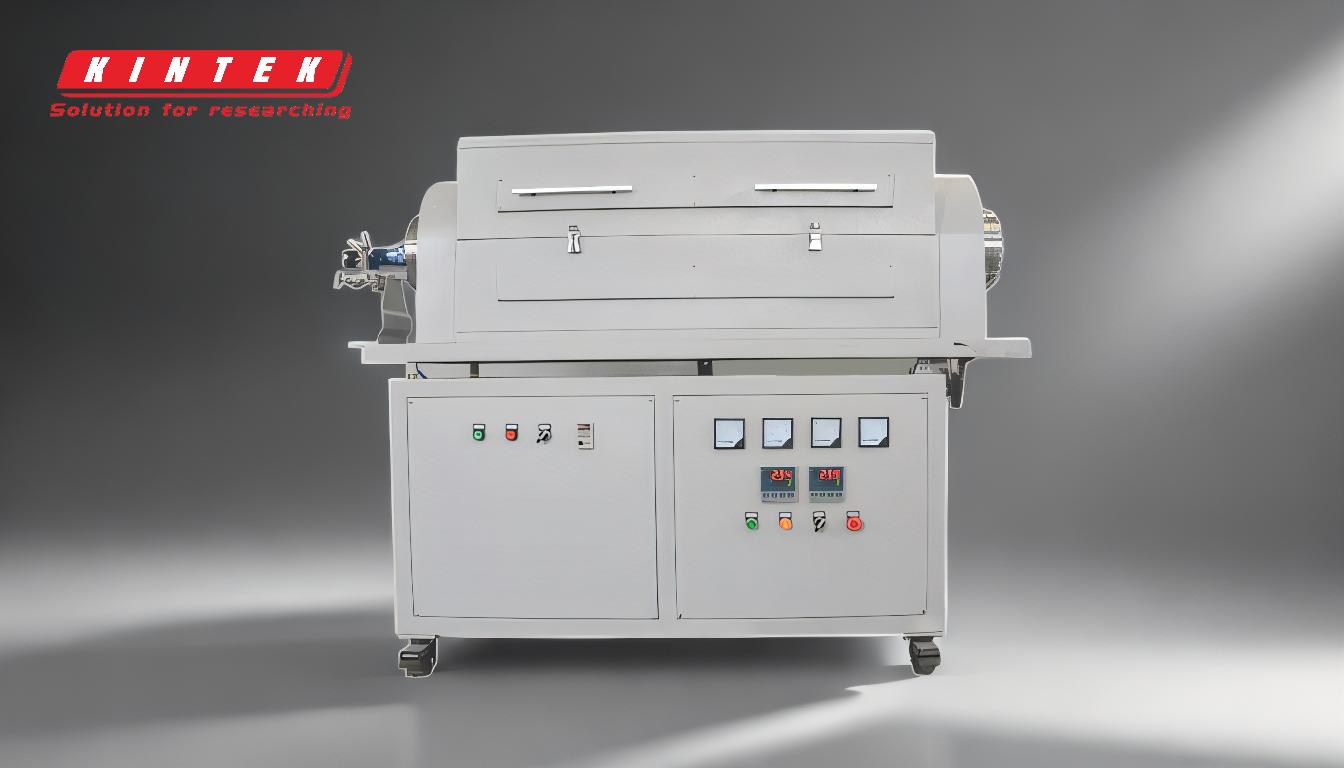
-
ALD as a Subset of CVD:
- ALD is a specialized form of CVD, sharing the fundamental principle of using chemical reactions to deposit thin films.
- Both techniques rely on precursor materials that react to form a solid film on a substrate.
- The key distinction lies in the process control and deposition mechanism, with ALD offering atomic-level precision.
-
Deposition Mechanism:
- CVD: Involves a continuous flow of precursor gases into the reaction chamber, where they react simultaneously to deposit a film. This process is less controlled and operates at higher temperatures.
- ALD: Uses a sequential, self-limiting process where two or more precursor gases are introduced one at a time. Each precursor reacts with the substrate surface in a controlled manner, ensuring atomic-level precision and uniformity.
-
Film Thickness and Conformality:
- ALD: Excels in depositing ultra-thin films (10-50 nm) with exceptional uniformity and conformality, even on high-aspect ratio structures. This makes it ideal for applications like semiconductor manufacturing and nanotechnology.
- CVD: Better suited for thicker films and higher deposition rates, making it more efficient for applications requiring bulk material deposition, such as coatings and protective layers.
-
Precursor Usage:
- CVD: Utilizes a wide range of precursors, often in a continuous flow, which can lead to less precise control over film properties.
- ALD: Employs a limited set of precursors introduced sequentially, ensuring precise control over film composition and thickness. The precursors are never present in the chamber simultaneously, reducing unwanted reactions.
-
Applications:
- ALD: Preferred for applications requiring high precision, such as microelectronics, MEMS, and advanced optics. Its ability to deposit pinhole-free, uniform films on complex geometries is unmatched.
- CVD: Used in industries requiring thicker, more robust coatings, such as aerospace, automotive, and energy. Its higher deposition rates make it more suitable for large-scale production.
-
Temperature and Process Control:
- CVD: Typically operates at higher temperatures, which can limit its use on temperature-sensitive substrates.
- ALD: Operates within a controlled temperature range, making it compatible with a broader range of materials and substrates, including those sensitive to high temperatures.
-
Advantages and Limitations:
- ALD: Offers superior control over film properties but at the cost of slower deposition rates and higher complexity in process setup.
- CVD: Provides faster deposition rates and greater versatility in precursor selection but with less precision in film thickness and conformality.
In summary, while ALD is a part of the broader CVD family, its unique process characteristics and superior control over film properties make it a distinct technique. Understanding the differences and applications of each method is crucial for selecting the right deposition technology for specific manufacturing needs.
Summary Table:
Aspect | ALD | CVD |
---|---|---|
Deposition Mechanism | Sequential, self-limiting process with atomic-level precision | Continuous flow of precursor gases with simultaneous reactions |
Film Thickness | Ultra-thin films (10-50 nm) with high uniformity and conformality | Thicker films with higher deposition rates |
Precursor Usage | Limited set introduced sequentially for precise control | Wide range of precursors in a continuous flow |
Applications | Microelectronics, MEMS, advanced optics | Aerospace, automotive, energy, and protective coatings |
Temperature Control | Operates at controlled temperatures for sensitive substrates | Higher temperatures, less suitable for sensitive materials |
Advantages | Superior control over film properties | Faster deposition rates and versatility in precursor selection |
Limitations | Slower deposition rates and higher complexity | Less precise control over film thickness and conformality |
Need help choosing the right deposition technology for your application? Contact our experts today!