Biofuel production costs are influenced by a variety of factors, including feedstock costs, plant capacity, operational expenses, and the efficiency of upgrading processes. While the initial investment and operational costs can be high, strategies such as using inexpensive catalysts, optimizing plant size, and implementing heat integration and recycling techniques can significantly reduce expenses. The economic viability of biofuel production is highly context-dependent, with larger-scale operations and technological advancements playing a crucial role in lowering costs. Overall, while biofuel production can be expensive, it is possible to achieve cost-effectiveness through strategic planning and innovation.
Key Points Explained:
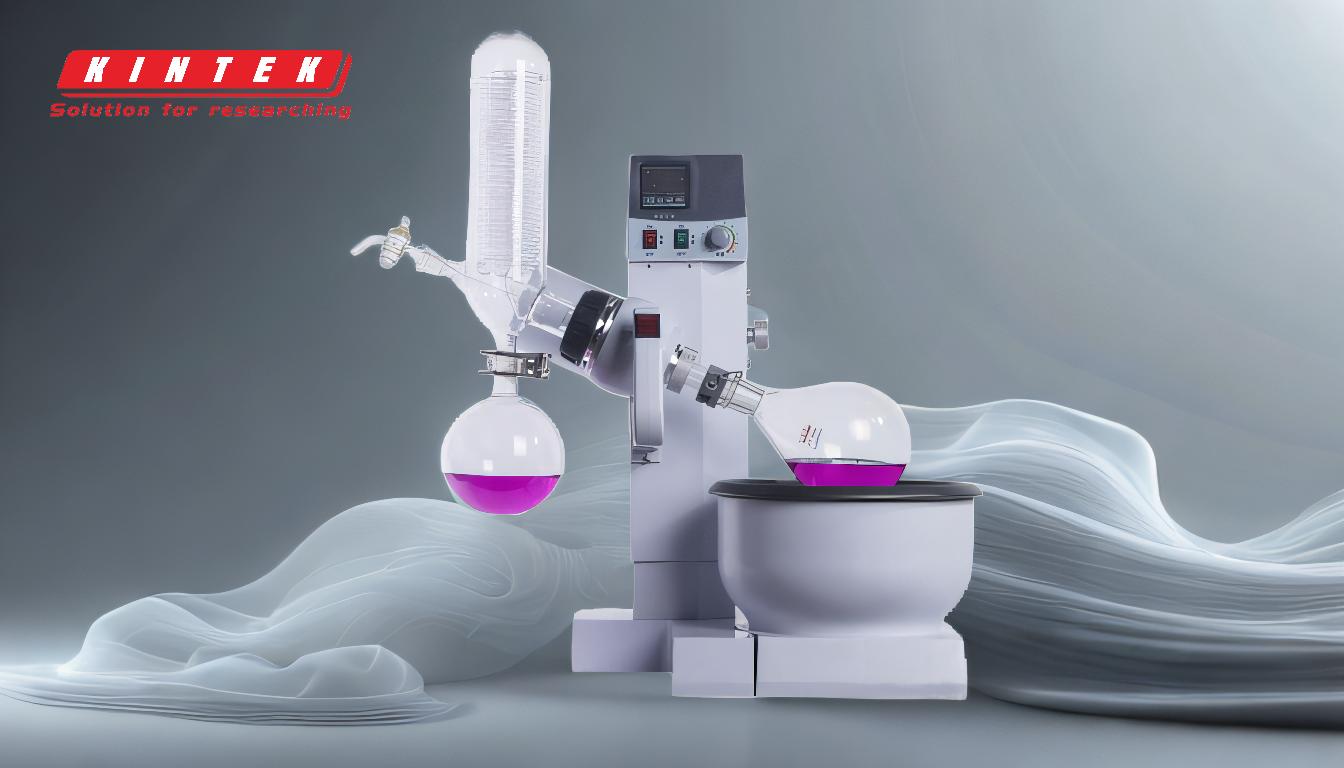
-
Feedstock Costs:
- The type and availability of feedstock significantly impact production costs. For example, using agricultural waste or non-food crops can be more cost-effective than using food crops.
- The cost of feedstock can vary widely depending on geographic location, seasonality, and market demand.
-
Plant Capacity:
- Larger plants generally benefit from economies of scale, reducing the per-unit cost of biofuel production. This is because fixed costs such as infrastructure and equipment are spread over a larger output.
- Smaller plants may have higher per-unit costs but can be more flexible and adaptable to local conditions.
-
Operational Costs:
- Operational expenses include labor, energy consumption, maintenance, and other day-to-day expenses. Efficient management and automation can help reduce these costs.
- Energy-intensive processes, such as those requiring high temperatures or pressures, can significantly increase operational costs.
-
Efficiency of Upgrading Processes:
- Upgrading processes, such as hydrotreating and catalytic cracking, are essential for converting raw bio-oil into usable biofuels. The efficiency and cost of these processes are critical factors in overall production costs.
- Inexpensive catalysts and optimized process conditions can reduce the cost and improve the efficiency of upgrading processes.
-
Heat Integration and Recycling:
- Heat integration involves capturing and reusing waste heat from various stages of the production process, thereby reducing energy consumption and costs.
- Recycling by-products and waste materials can further enhance sustainability and cost-effectiveness, as it reduces the need for new raw materials and minimizes waste disposal costs.
-
Technological Advancements:
- Continuous research and development in biofuel production technologies can lead to more efficient and cost-effective methods. For example, advancements in enzyme technology and genetic engineering can improve feedstock conversion rates.
- Innovations in process engineering, such as modular and mobile biofuel production units, can also reduce costs and increase flexibility.
-
Government Policies and Incentives:
- Government policies, subsidies, and incentives can play a significant role in reducing the financial burden of biofuel production. These can include tax credits, grants, and mandates for biofuel blending in transportation fuels.
- Regulatory support for renewable energy sources can create a more favorable market environment for biofuels, encouraging investment and innovation.
-
Market Dynamics:
- The price of biofuels is influenced by market dynamics, including the price of fossil fuels, demand for renewable energy, and competition from other renewable energy sources.
- Fluctuations in oil prices can impact the competitiveness of biofuels, as lower fossil fuel prices can make biofuels less economically attractive.
In summary, while biofuel production can be expensive due to high initial and operational costs, various strategies and factors can mitigate these expenses. Economies of scale, technological advancements, efficient process management, and supportive government policies are key to achieving cost-effective biofuel production. The overall economic viability of biofuel production is highly dependent on these factors, and continuous innovation and optimization are essential for reducing costs and enhancing sustainability.
Summary Table:
Factor | Impact on Costs |
---|---|
Feedstock Costs | Type, availability, and market demand significantly influence raw material expenses. |
Plant Capacity | Larger plants benefit from economies of scale, reducing per-unit production costs. |
Operational Costs | Labor, energy, and maintenance expenses can be reduced through efficient management. |
Upgrading Processes | Efficient processes and inexpensive catalysts lower conversion costs. |
Heat Integration | Reusing waste heat reduces energy consumption and operational expenses. |
Technological Advancements | Innovations improve efficiency and reduce costs over time. |
Government Policies | Subsidies and incentives can lower financial burdens. |
Market Dynamics | Fossil fuel prices and renewable energy demand affect biofuel competitiveness. |
Discover how to optimize your biofuel production costs—contact our experts today for tailored solutions!