Brazing is indeed performed in a vacuum furnace, as it offers a controlled environment that ensures high consistency and low contamination. The vacuum environment is particularly beneficial for brazing because it prevents oxidation and allows for precise temperature control, which is crucial for achieving strong, clean, and reliable joints. This method is widely used in industries where high-quality brazing is required, such as aerospace, automotive, and electronics.
Key Points Explained:
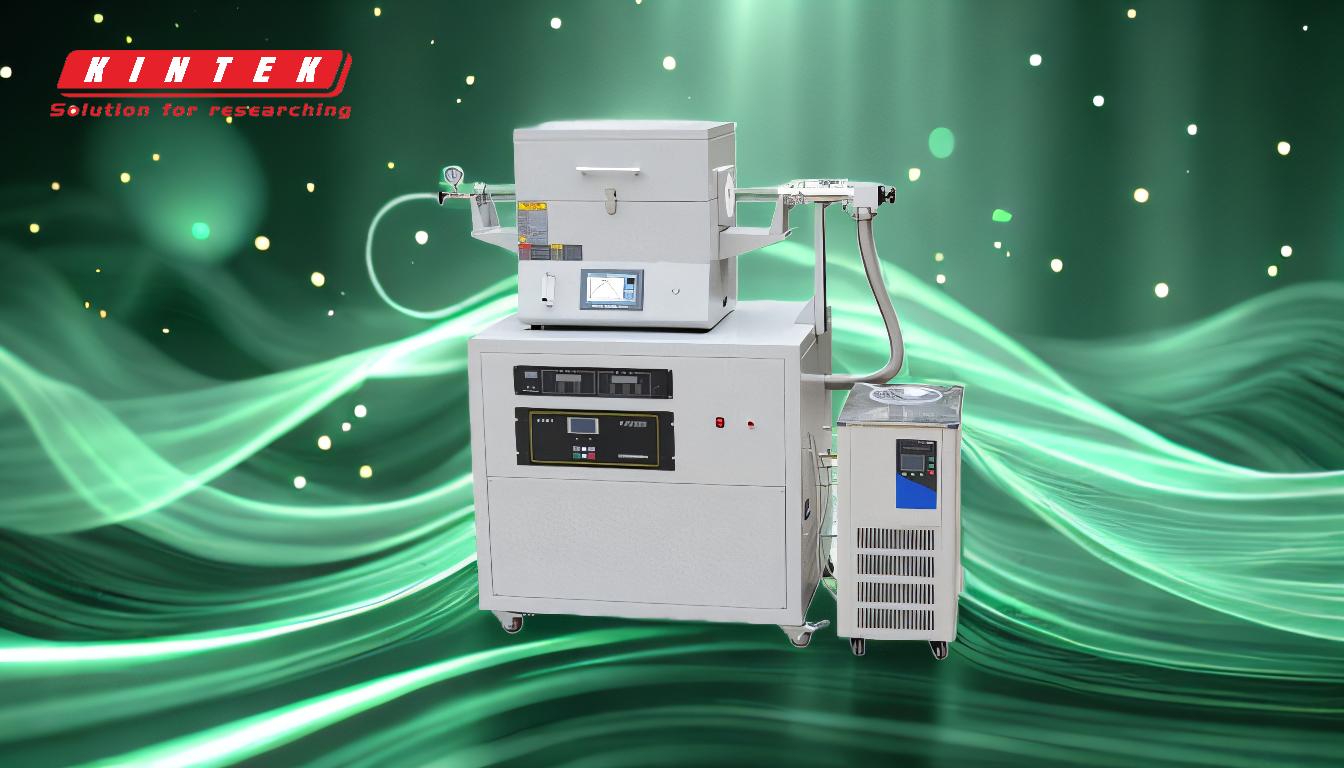
-
Brazing in a Vacuum Furnace:
- Brazing is a process where two or more metal items are joined together by melting and flowing a filler metal into the joint. The filler metal has a lower melting point than the adjoining metal.
- In a vacuum furnace, brazing is performed under a vacuum, which eliminates the presence of oxygen and other reactive gases. This prevents oxidation and contamination, resulting in cleaner and stronger joints.
-
Advantages of Vacuum Brazing:
- Oxidation Prevention: The absence of oxygen in a vacuum furnace prevents the formation of oxides on the metal surfaces, which can weaken the joint.
- Consistent Quality: The controlled environment ensures uniform heating and cooling, leading to consistent brazing results.
- Minimal Contamination: The vacuum environment minimizes the risk of contamination from external sources, which is critical for high-precision applications.
- Versatility: Vacuum brazing can be used with a wide range of materials, including those that are difficult to braze in air, such as titanium and certain stainless steels.
-
Applications of Vacuum Brazing:
- Aerospace: Components such as turbine blades and heat exchangers are often brazed in vacuum furnaces to ensure high strength and reliability.
- Automotive: Vacuum brazing is used for manufacturing parts like fuel injectors and transmission components, where precision and durability are essential.
- Electronics: In the electronics industry, vacuum brazing is used to create hermetic seals and join components that require high thermal and electrical conductivity.
-
Comparison with Other Brazing Methods:
- Atmospheric Brazing: Performed in air or with a protective gas, this method is less expensive but more prone to oxidation and contamination.
- Controlled Atmosphere Brazing: Uses inert gases like argon or nitrogen to reduce oxidation, but it may not be as effective as vacuum brazing in preventing contamination.
- Flux Brazing: Involves the use of a chemical flux to prevent oxidation, but the flux can leave residues that need to be cleaned, adding an extra step to the process.
-
Process Steps in Vacuum Brazing:
- Preparation: Clean the metal surfaces to remove any oils, oxides, or contaminants.
- Assembly: Position the components and the filler metal in the desired configuration.
- Heating: Place the assembly in the vacuum furnace and heat it to the brazing temperature, which is above the melting point of the filler metal but below the melting point of the base metals.
- Cooling: Allow the assembly to cool in the vacuum environment to ensure a strong, defect-free joint.
-
Materials Suitable for Vacuum Brazing:
- Stainless Steels: Commonly used in vacuum brazing due to their corrosion resistance and strength.
- Titanium Alloys: Ideal for aerospace applications because of their high strength-to-weight ratio.
- Nickel Alloys: Used in high-temperature applications due to their excellent thermal stability.
- Copper and Copper Alloys: Often used in electronics for their excellent electrical conductivity.
In summary, brazing in a vacuum furnace is a highly effective method for joining metals, offering numerous advantages over other brazing techniques. The controlled environment ensures high-quality, clean, and reliable joints, making it the preferred choice for many critical applications across various industries.
Summary Table:
Aspect | Details |
---|---|
Process | Brazing in a vacuum furnace prevents oxidation and contamination. |
Advantages | Oxidation prevention, consistent quality, minimal contamination, versatility. |
Applications | Aerospace, automotive, electronics. |
Materials | Stainless steels, titanium alloys, nickel alloys, copper and copper alloys. |
Comparison | Superior to atmospheric, controlled atmosphere, and flux brazing methods. |
Ready to achieve high-quality brazing results? Contact us today to learn more about vacuum furnace solutions!