Compression molding and transfer molding are both widely used techniques in the manufacturing of rubber and plastic parts, but they differ significantly in their processes, equipment, and applications. Compression molding involves placing material directly into a mold cavity and applying pressure to shape it, while transfer molding preheats and pressurizes the material in a separate chamber before forcing it into the mold. These differences affect factors like material efficiency, complexity, and cost, making each method suitable for specific use cases.
Key Points Explained:
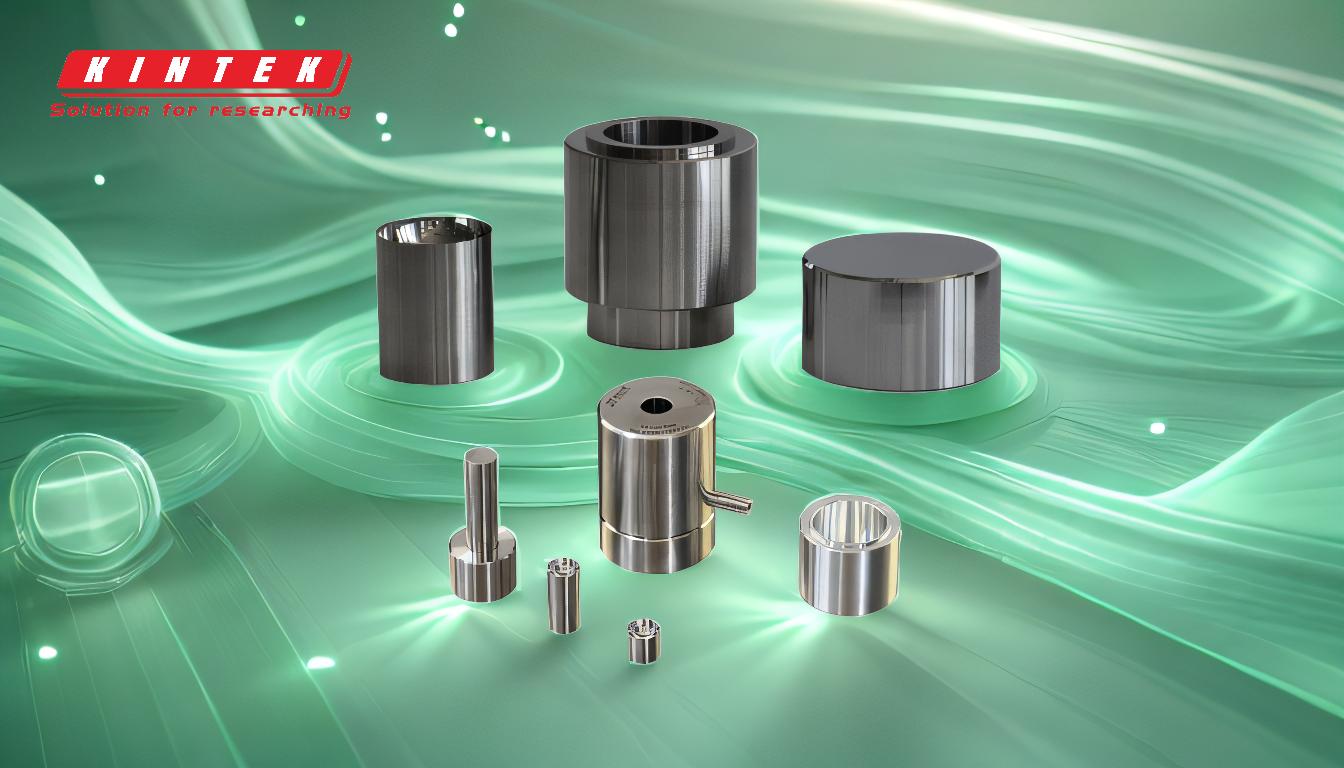
-
Process Differences:
-
Compression Molding:
- Material is placed directly into the mold cavity.
- The mold is closed, and pressure is applied to shape the material.
- Excess material, known as mold flash, flows out of special grooves.
- Simpler and more cost-effective due to fewer components and steps.
-
Transfer Molding:
- Material is preheated and pressurized in a separate chamber (pot).
- A piston forces the material through holes into the mold cavity.
- More complex due to the additional components (plunger, pot, and piston).
-
Compression Molding:
-
Equipment and Tooling:
-
Compression Molding:
- Requires a simpler setup with fewer components.
- Typically uses a platen press for applying pressure.
- Lower tooling costs and shorter lead times.
-
Transfer Molding:
- Involves a plunger, cylinder (pot), and mold cavity.
- More complex tooling and higher initial costs.
- Suitable for intricate designs and smaller parts.
-
Compression Molding:
-
Material Efficiency:
-
Compression Molding:
- Results in less material loss compared to injection molding.
- Excess material (mold flash) can be recycled or reused.
-
Transfer Molding:
- May result in higher material loss due to the transfer process.
- However, it allows for better control over material flow and placement.
-
Compression Molding:
-
Applications and Suitability:
-
Compression Molding:
- Ideal for simpler, larger parts with less intricate designs.
- Commonly used in laboratory settings and for cost-sensitive projects.
-
Transfer Molding:
- Better suited for complex, intricate parts with fine details.
- Often used in industries requiring high precision, such as electronics and automotive.
-
Compression Molding:
-
Cost and Efficiency:
-
Compression Molding:
- Generally more cost-effective due to simpler equipment and lower material loss.
- Faster production times for simpler parts.
-
Transfer Molding:
- Higher initial costs due to more complex tooling and equipment.
- May offer better efficiency for complex parts, reducing the need for secondary operations.
-
Compression Molding:
In summary, while both compression molding and transfer molding are effective techniques for shaping rubber and plastic materials, they serve different purposes and are suited to different types of projects. Compression molding is simpler and more cost-effective, making it ideal for larger, less intricate parts. Transfer molding, on the other hand, offers greater precision and control, making it better suited for complex, detailed components. Understanding these differences can help in selecting the appropriate method for specific manufacturing needs.
Summary Table:
Aspect | Compression Molding | Transfer Molding |
---|---|---|
Process | Material placed directly into mold cavity | Material preheated and pressurized in a pot |
Equipment | Simpler setup, platen press | Complex setup with plunger, pot, and piston |
Material Efficiency | Less material loss, excess material reusable | Higher material loss, better flow control |
Applications | Simpler, larger parts | Complex, intricate parts |
Cost | More cost-effective, lower tooling costs | Higher initial costs, better for precision |
Need help choosing the right molding technique for your project? Contact our experts today for personalized guidance!