Diffusion bonding and sintering are both solid-state joining processes used in materials science and engineering, but they are not the same. Diffusion bonding involves joining two materials by applying heat and pressure, allowing atoms to diffuse across the interface and form a strong bond. Sintering, on the other hand, is a process where powdered materials are compacted and heated to form a solid mass without melting. While both processes rely on atomic diffusion, their applications, mechanisms, and outcomes differ significantly.
Key Points Explained:
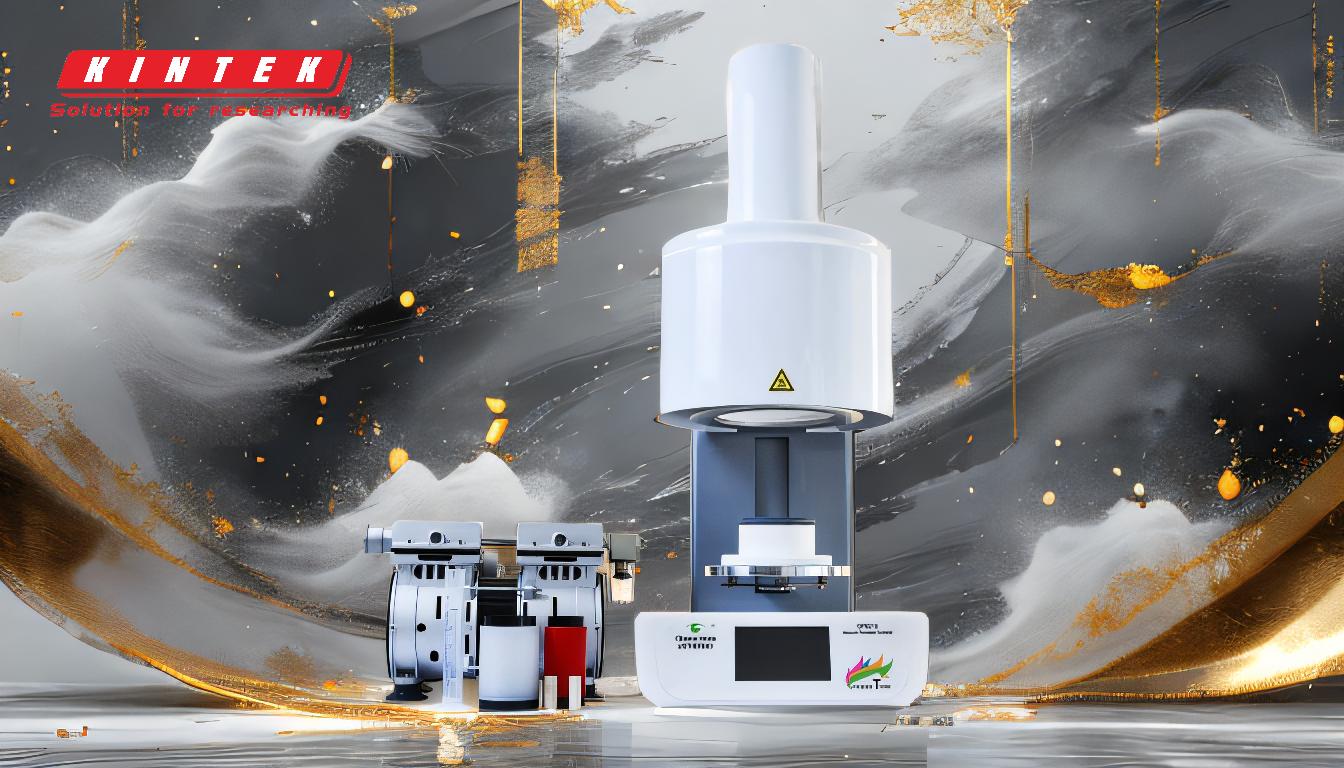
-
Definition and Mechanism:
- Diffusion Bonding: This process involves placing two materials in close contact under high pressure and elevated temperature. The atoms from the two surfaces diffuse across the interface, forming a solid bond. It is often used for joining dissimilar materials or creating complex geometries.
- Sintering: Sintering is a process where powdered materials are compacted and heated below their melting point. The particles bond together through atomic diffusion, reducing porosity and increasing density. It is commonly used in powder metallurgy and ceramics.
-
Temperature and Pressure Requirements:
- Diffusion Bonding: Typically requires higher pressures and precise temperature control to ensure proper atomic diffusion across the interface. The temperature is usually below the melting point of the materials.
- Sintering: Operates at lower pressures compared to diffusion bonding. The temperature is also below the melting point but is optimized to facilitate particle bonding and densification.
-
Applications:
- Diffusion Bonding: Used in aerospace, automotive, and electronics industries for joining dissimilar metals, creating complex parts, and ensuring high-strength bonds.
- Sintering: Widely used in manufacturing components from metal powders, ceramics, and composites. It is essential in producing parts with controlled porosity and mechanical properties.
-
Outcomes:
- Diffusion Bonding: Results in a joint with properties similar to the base materials, often with minimal distortion or residual stress.
- Sintering: Produces a solid mass with reduced porosity and improved mechanical properties, but the final product may still have some residual porosity.
-
Material Compatibility:
- Diffusion Bonding: Suitable for a wide range of materials, including metals, ceramics, and composites. It is particularly effective for joining dissimilar materials.
- Sintering: Primarily used for materials that can be powdered, such as metals and ceramics. It is less effective for joining dissimilar materials compared to diffusion bonding.
-
Process Complexity:
- Diffusion Bonding: Requires precise control of temperature, pressure, and time, making it a more complex and costly process.
- Sintering: Generally simpler and more cost-effective, especially for mass production of components.
In summary, while both diffusion bonding and sintering rely on atomic diffusion to achieve material bonding, they differ in their mechanisms, applications, and outcomes. Diffusion bonding is more suited for joining dissimilar materials and creating high-strength bonds, whereas sintering is ideal for producing solid components from powdered materials with controlled properties.
Summary Table:
Aspect | Diffusion Bonding | Sintering |
---|---|---|
Definition | Joins two materials under heat and pressure, allowing atomic diffusion across the interface. | Compacts and heats powdered materials to form a solid mass without melting. |
Temperature/Pressure | High pressure and precise temperature control, below melting point. | Lower pressure, temperature below melting point, optimized for particle bonding. |
Applications | Aerospace, automotive, electronics (joining dissimilar materials). | Powder metallurgy, ceramics, composites (manufacturing components). |
Outcomes | Strong bond with minimal distortion or residual stress. | Solid mass with reduced porosity, improved mechanical properties. |
Material Compatibility | Suitable for metals, ceramics, composites (effective for dissimilar materials). | Primarily for powdered metals and ceramics (less effective for dissimilar materials). |
Process Complexity | More complex and costly due to precise control requirements. | Simpler and cost-effective, ideal for mass production. |
Need help choosing the right process for your materials? Contact our experts today!