Graphite is indeed a good material for heating elements, particularly in high-temperature applications. It is cost-effective compared to metallic elements and exhibits unique properties such as a decrease in electrical resistance when heated, high thermal resistance, and excellent mechanical strength at elevated temperatures. Graphite heating elements are widely used in industries requiring uniform temperature distribution, longevity, and resistance to thermal shock. However, they require careful handling in vacuum environments and at very high temperatures to prevent issues like volatilization and vacuum discharge.
Key Points Explained:
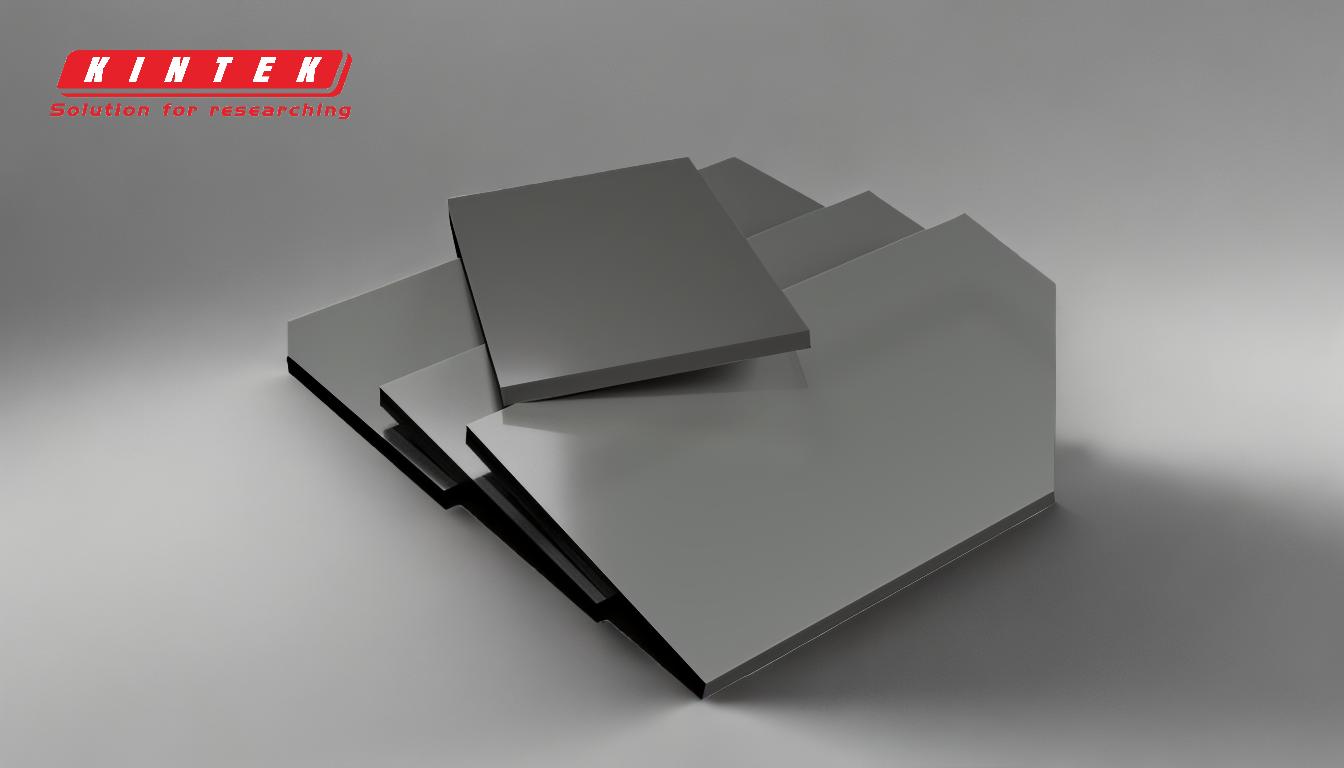
-
Cost-Effectiveness:
- Graphite is less expensive than metallic heating elements, making it a budget-friendly option for industrial applications.
- Its affordability does not compromise its performance, as it offers excellent thermal and electrical properties.
-
Electrical Resistance Behavior:
- Graphite exhibits a unique property where its electrical resistance decreases by approximately 20% when heated. This characteristic makes it highly efficient for heating applications, as it requires less energy to maintain high temperatures.
-
High-Temperature Resistance:
- Graphite heating elements are capable of withstanding extreme temperatures, making them suitable for high-temperature environments such as vacuum furnaces and industrial heating systems.
- They perform optimally at temperatures around 1700°C and can withstand temperatures up to 2500°C without significant degradation.
-
Thermal Properties:
- Graphite has excellent thermal shock resistance, meaning it can withstand rapid temperature changes without cracking or breaking.
- Its low thermal expansion ensures dimensional stability at high temperatures, which is crucial for maintaining the integrity of heating elements.
-
Mechanical Strength:
- The mechanical strength of graphite improves as temperatures rise, peaking at around 2500°C. This makes it highly durable and reliable in demanding industrial environments.
-
Chemical Resistance:
- Graphite is chemically inert and resistant to corrosion, making it suitable for use in environments with reactive gases or chemicals.
- It reacts with residual oxygen and water vapor in vacuum furnaces, creating a purification effect that simplifies the vacuum system and reduces operational costs.
-
Uniform Temperature Distribution:
- Graphite heating elements provide excellent temperature uniformity, ensuring consistent heating across the entire surface. This is critical for processes requiring precise temperature control.
-
Longevity and Repeatability:
- Due to its durability and resistance to wear, graphite heating elements have a long operational life. They also offer repeatable performance, making them reliable for continuous industrial use.
-
Limitations:
- Graphite is volatile at very high temperatures, which can lead to material loss over time. This requires careful management in vacuum environments.
- It is also susceptible to vacuum discharge at voltages above 100V, necessitating preventive measures in high-voltage applications.
-
Applications:
- Graphite heating elements are widely used in industries such as semiconductor manufacturing, metallurgy, and materials processing, where high temperatures and uniform heating are required.
- They are particularly favored in vacuum furnaces due to their ability to operate efficiently in low-pressure environments.
In summary, graphite is an excellent material for heating elements due to its cost-effectiveness, high-temperature resistance, thermal stability, and mechanical strength. However, its limitations, such as volatility at high temperatures and susceptibility to vacuum discharge, must be carefully managed to ensure optimal performance and longevity.
Summary Table:
Key Feature | Description |
---|---|
Cost-Effectiveness | Less expensive than metallic elements, budget-friendly for industrial use. |
Electrical Resistance | Resistance decreases by 20% when heated, improving energy efficiency. |
High-Temperature Use | Withstands up to 2500°C, ideal for vacuum furnaces and extreme environments. |
Thermal Shock Resistance | Resists cracking during rapid temperature changes, ensuring durability. |
Mechanical Strength | Strength increases with temperature, peaking at 2500°C. |
Chemical Resistance | Inert and corrosion-resistant, suitable for reactive environments. |
Uniform Heating | Provides consistent temperature distribution for precise processes. |
Longevity | Durable and wear-resistant, offering reliable repeatable performance. |
Limitations | Volatile at high temperatures; susceptible to vacuum discharge above 100V. |
Applications | Used in semiconductor manufacturing, metallurgy, and materials processing. |
Ready to optimize your heating processes with graphite elements? Contact our experts today for tailored solutions!