High ash content is generally not considered good, as it often indicates lower quality in materials like coal, biomass, or other fuels. Ash is the non-combustible residue left after burning, and high ash content can lead to reduced energy efficiency, increased maintenance costs, and environmental concerns. However, the impact of ash content depends on the specific application. For example, in some industrial processes, certain types of ash might be beneficial. Overall, the desirability of high ash content is context-dependent, but in most cases, lower ash content is preferred for better performance and reduced operational challenges.
Key Points Explained:
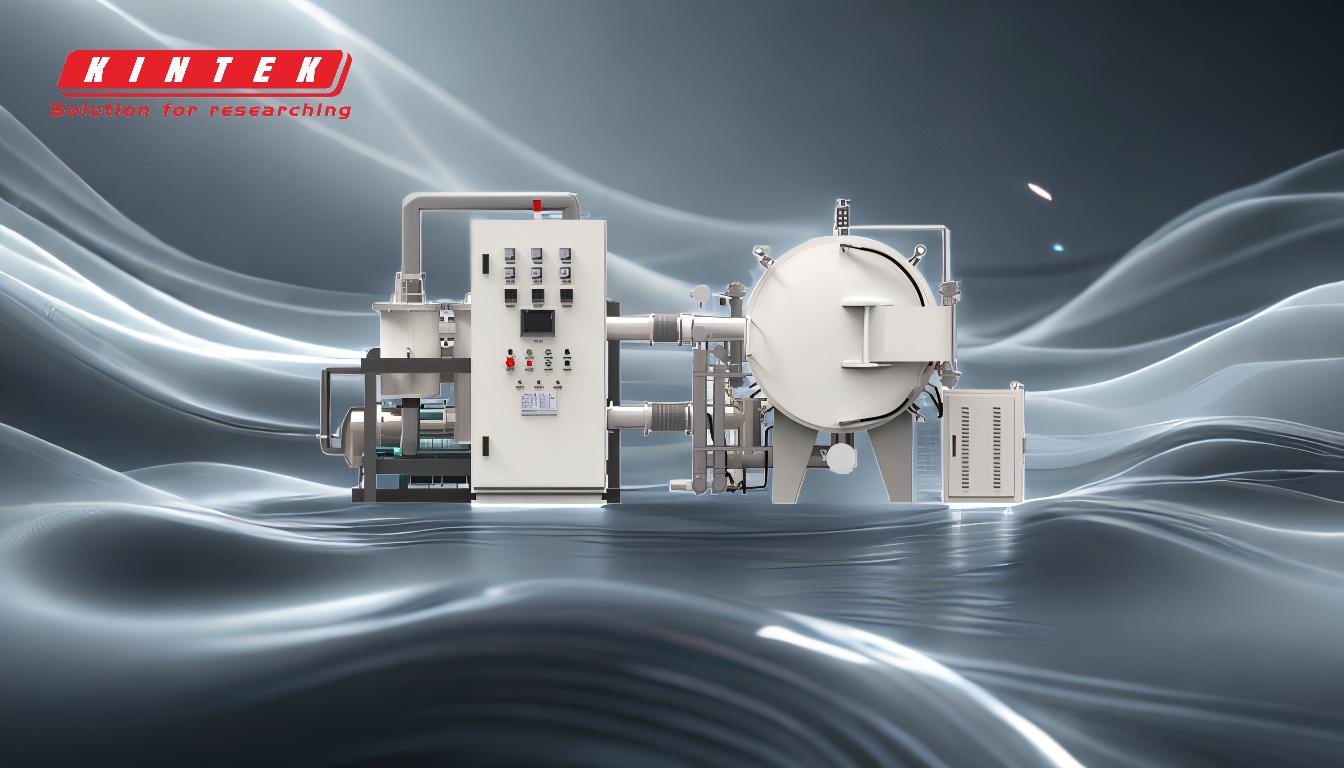
-
Definition of Ash Content:
- Ash content refers to the inorganic, non-combustible residue that remains after a material is burned. It is typically composed of minerals and impurities.
- In fuels like coal or biomass, ash content is a critical parameter that affects combustion efficiency and environmental impact.
-
Negative Effects of High Ash Content:
- Reduced Energy Efficiency: High ash content means less combustible material, leading to lower calorific value and reduced energy output.
- Increased Maintenance Costs: Ash can cause wear and tear on equipment, clogging systems, and requiring frequent cleaning and repairs.
- Environmental Concerns: High ash content can lead to higher emissions of particulate matter and other pollutants, contributing to air quality issues.
- Waste Management Challenges: Disposal of ash can be costly and environmentally problematic, especially if it contains toxic substances.
-
Context-Dependent Considerations:
- In some industrial processes, such as cement production, certain types of ash (e.g., fly ash) can be used as a raw material, making it beneficial.
- For agricultural applications, ash might be used as a soil amendment to improve fertility, though this depends on its composition.
- The specific type of ash and its chemical composition play a significant role in determining whether it is useful or detrimental.
-
Comparison with Low Ash Content:
- Low ash content is generally preferred for fuels and materials because it ensures higher energy efficiency and fewer operational issues.
- Materials with low ash content are often more expensive but can lead to cost savings in the long run due to reduced maintenance and better performance.
-
Practical Implications for Equipment and Consumables Purchasers:
- When purchasing fuels or materials, buyers should prioritize low ash content to minimize operational challenges and environmental impact.
- For specific applications where ash can be repurposed, buyers should evaluate the ash composition to determine its potential benefits.
- Regular testing and quality control are essential to ensure that materials meet the required ash content specifications.
In conclusion, while high ash content is generally undesirable, its impact depends on the application and the specific characteristics of the ash. For most scenarios, especially in fuel and energy production, lower ash content is preferable for better performance and sustainability.
Summary Table:
Aspect | High Ash Content | Low Ash Content |
---|---|---|
Energy Efficiency | Reduced calorific value, lower energy output | Higher calorific value, better energy output |
Maintenance Costs | Increased wear and tear, frequent cleaning, and repairs | Reduced maintenance needs, longer equipment lifespan |
Environmental Impact | Higher emissions, air quality issues, and waste management challenges | Lower emissions, reduced environmental concerns |
Application Suitability | Beneficial in specific industries (e.g., cement production, agriculture) | Preferred for most fuel and energy applications |
Cost | Lower upfront cost but higher operational expenses | Higher upfront cost but long-term savings due to efficiency |
Need help selecting the right fuel or material for your needs? Contact our experts today for tailored advice!