Induction heating is indeed a fast and efficient method for heating conductive materials. Unlike traditional heating methods that rely on external heat sources and heat transfer mechanisms like convection and radiation, induction heating generates heat directly within the material through induced electrical currents. This internal generation of heat allows for rapid temperature increases, precise control, and minimal heat loss. The speed of induction heating is influenced by factors such as the material's properties, the frequency of the alternating current, and the design of the inductor coil. High-frequency induction heating, in particular, is known for its speed, making it suitable for applications requiring quick and localized heating.
Key Points Explained:
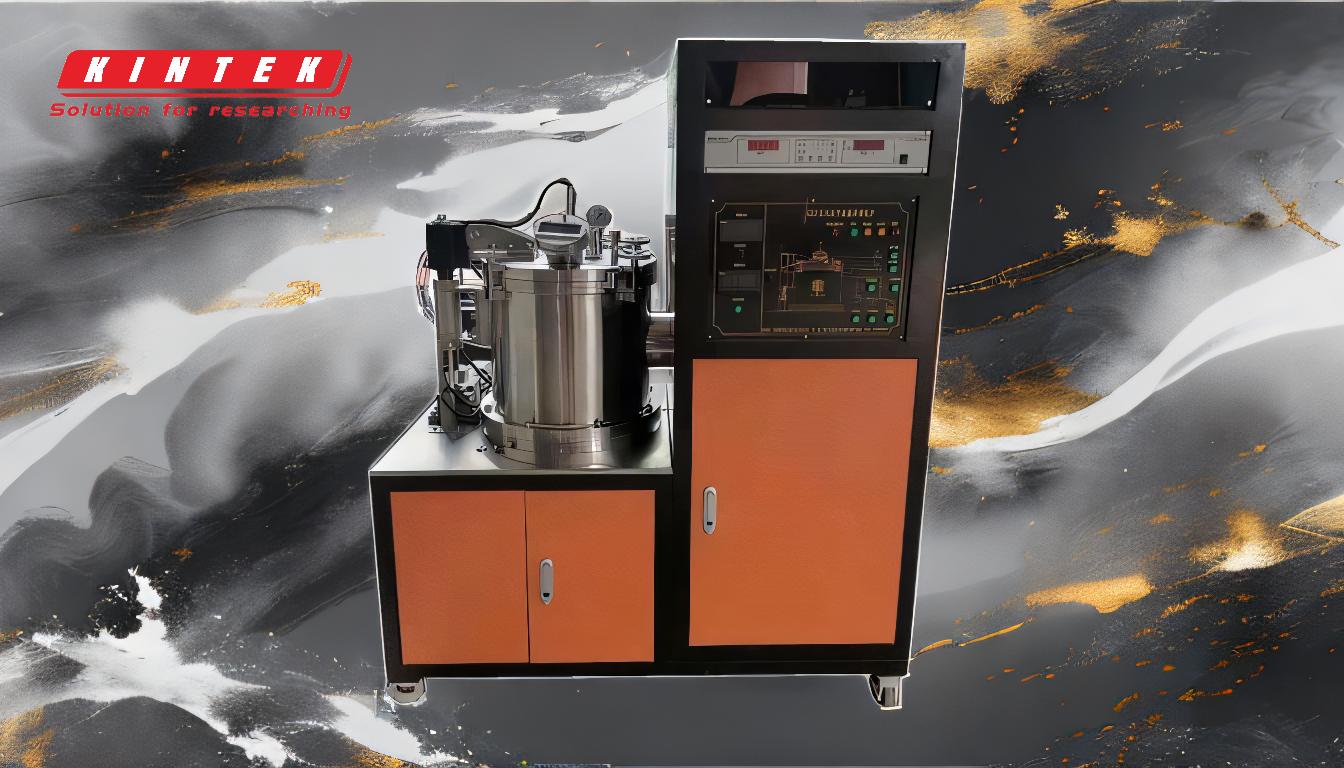
-
Internal Heat Generation:
- Induction heating generates heat directly within the material through induced electrical currents. This internal heat generation allows for rapid and efficient heating, as there is no need to wait for heat to transfer from an external source.
- The absence of an external heat source also reduces heat loss, making the process more energy-efficient.
-
Speed and Efficiency:
- Induction heating is characterized by its fast speed, especially in high-frequency applications. The ability to quickly reach the desired temperature makes it ideal for processes requiring rapid heating.
- The efficiency of induction heating is influenced by factors such as the material's resistivity, size, and thickness. Materials with higher resistivity and smaller, thinner profiles heat up faster.
-
Frequency and Heating Depth:
- The frequency of the alternating current used in induction heating plays a crucial role in determining the heating speed and depth. Higher frequencies result in lower heating depths, allowing for precise and localized heating.
- Intermediate and high-frequency induction heating are particularly noted for their fast heating speeds and high efficiency.
-
Material Properties:
- The type of material being heated significantly affects the speed of induction heating. Conductive materials like metals and semiconductors are ideal for this method.
- The material's specific heat, mass, and required temperature rise also impact the heating speed. Materials with lower specific heat and mass heat up faster.
-
Inductor Coil Design:
- The design of the inductor coil is critical in optimizing the heating process. A well-designed coil ensures efficient energy transfer and uniform heating.
- The coil's design must account for the material's size, shape, and the desired heating pattern to achieve rapid and effective heating.
-
Applications and Advantages:
- Induction heating is widely used in industrial, medical, and domestic applications due to its speed, precision, and efficiency.
- The method is particularly beneficial in situations where contamination is a concern, as it does not require external contact.
In summary, induction heating is a fast and efficient method for heating conductive materials. Its ability to generate heat internally, combined with the influence of material properties and inductor coil design, allows for rapid and precise temperature control. This makes induction heating an ideal choice for a wide range of applications requiring quick and localized heating.
Summary Table:
Key Factor | Impact on Induction Heating |
---|---|
Internal Heat Generation | Heat is generated directly within the material, reducing heat loss and enabling rapid heating. |
Frequency | Higher frequencies allow for precise, localized heating with faster speeds. |
Material Properties | Conductive materials with high resistivity and low mass heat up faster. |
Inductor Coil Design | Optimized coil design ensures efficient energy transfer and uniform heating. |
Applications | Ideal for industrial, medical, and domestic uses requiring quick, localized heating. |
Ready to harness the power of induction heating for your applications? Contact us today to learn more!