Graphite, whether natural or synthetic, is widely used in furnace applications due to its exceptional thermal and mechanical properties. Both types of graphite have unique advantages and disadvantages, making them suitable for different applications. Natural graphite is derived from mined sources and is often less expensive, while synthetic graphite is manufactured through high-temperature processing of carbon materials, offering higher purity and consistency. When selecting graphite for a graphite furnace, factors such as thermal conductivity, durability, cost, and specific application requirements must be considered. Below, we explore the key differences between natural and synthetic graphite to determine which is better for specific furnace applications.
Key Points Explained:
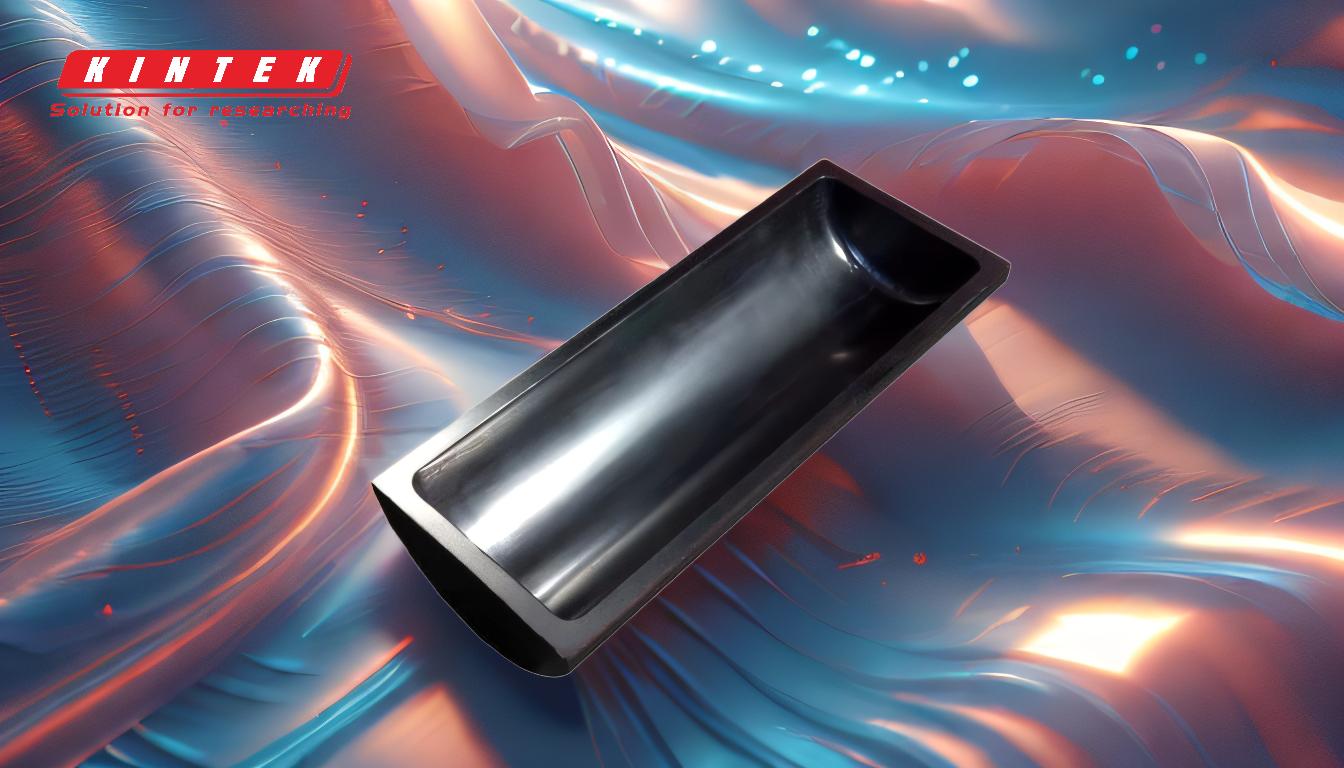
-
Thermal Properties:
- Both natural and synthetic graphite exhibit excellent thermal conductivity, making them ideal for furnace applications.
- Synthetic graphite often has a more uniform structure, which can lead to better heat distribution and stability in high-temperature environments.
- Natural graphite, while thermally efficient, may have impurities that affect its performance in extreme conditions.
-
Mechanical Strength and Durability:
- Synthetic graphite is generally stronger and more durable due to its controlled manufacturing process, which eliminates impurities and enhances structural integrity.
- Natural graphite, while robust, may have inconsistencies in its structure, leading to potential weaknesses under mechanical stress.
-
Cost Considerations:
- Natural graphite is typically less expensive than synthetic graphite, making it a cost-effective option for applications where high purity is not critical.
- Synthetic graphite, though more costly, offers superior performance and longevity, which can justify the higher initial investment in high-performance furnace applications.
-
Purity and Consistency:
- Synthetic graphite is known for its high purity and consistency, which is crucial for applications requiring precise thermal management and minimal contamination.
- Natural graphite may contain trace elements or impurities that could affect its performance in sensitive applications.
-
Repairability and Maintenance:
- Both types of graphite are repairable, but synthetic graphite often has a more uniform structure, making repairs easier and more effective.
- Natural graphite may require more frequent maintenance due to its potential for structural inconsistencies.
-
Application-Specific Suitability:
- For high-performance graphite furnaces requiring rapid heating and cooling cycles, synthetic graphite is often the preferred choice due to its superior thermal and mechanical properties.
- Natural graphite may be suitable for less demanding applications where cost is a primary concern.
In conclusion, the choice between natural and synthetic graphite depends on the specific requirements of the furnace application. Synthetic graphite is generally better for high-performance, high-temperature applications due to its purity, consistency, and durability. Natural graphite, on the other hand, may be a more economical choice for less demanding applications. Understanding the unique properties of each type of graphite will help in making an informed decision tailored to the needs of the furnace system.
Summary Table:
Property | Natural Graphite | Synthetic Graphite |
---|---|---|
Thermal Conductivity | Excellent, but may have impurities | Superior, uniform heat distribution |
Mechanical Strength | Robust, but may have inconsistencies | Stronger, more durable |
Cost | Less expensive | More expensive |
Purity & Consistency | May contain impurities | High purity, consistent structure |
Repairability | Requires more frequent maintenance | Easier to repair |
Suitability | Cost-effective for less demanding uses | Ideal for high-performance applications |
Need help choosing the right graphite for your furnace? Contact our experts today for personalized advice!