Physical Vapor Deposition (PVD) is a bottom-up fabrication technique. It involves the deposition of thin films by physically transferring material from a source (target) to a substrate in a vacuum environment. Unlike top-down methods, which involve removing material to create structures, PVD builds up layers atom by atom or molecule by molecule. This process is widely used in industries such as semiconductors, optics, and coatings due to its precision and ability to produce high-quality, uniform films. The key steps in PVD include evaporation, transportation, and condensation of the material, which collectively ensure controlled and precise layer formation.
Key Points Explained:
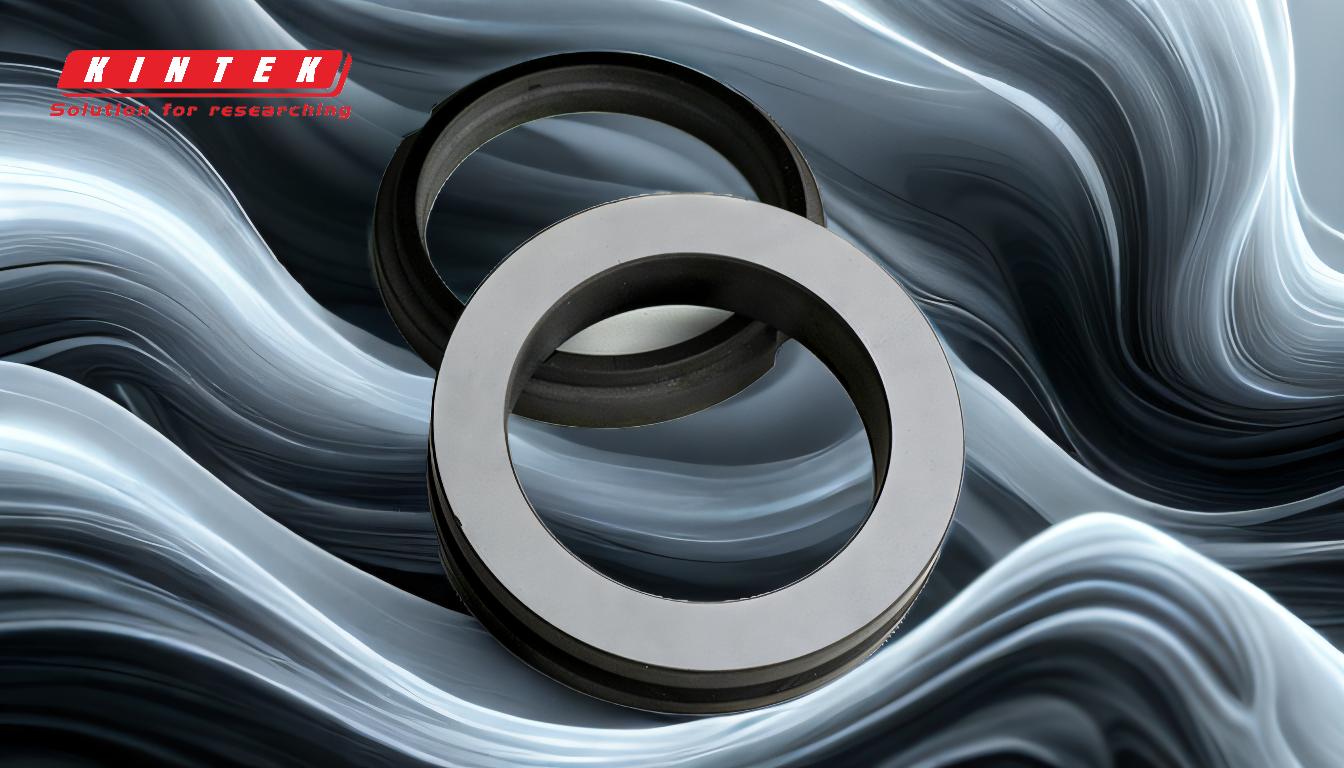
-
Definition of Physical Vapor Deposition (PVD):
- PVD is a vacuum-based process used to deposit thin films of material onto a substrate. It involves the physical transfer of material from a source (target) to the substrate through processes like sputtering or evaporation. This method is fundamentally a bottom-up approach because it builds structures by adding material layer by layer, rather than removing material as in top-down methods.
-
Bottom-Up vs. Top-Down Fabrication:
- Bottom-Up: In bottom-up fabrication, materials are assembled atom by atom or molecule by molecule to create structures. PVD falls under this category because it deposits material onto a substrate in a controlled manner, forming thin films or coatings.
- Top-Down: Top-down methods involve starting with a bulk material and removing parts of it to create the desired structure, such as in etching or machining processes. PVD does not involve material removal, so it is not a top-down technique.
-
Key Steps in PVD:
- Evaporation: The material to be deposited is heated in a vacuum until it evaporates or sublimates, turning into a vapor.
- Transportation: The vaporized material is transported through the vacuum environment to the substrate.
- Condensation: The vapor condenses on the substrate, forming a thin film. This step-by-step process ensures precise control over film thickness and uniformity.
-
Applications of PVD:
- PVD is widely used in industries such as semiconductors, optics, and coatings. It is particularly valued for its ability to produce high-quality, uniform films with excellent adhesion and durability. Examples include anti-reflective coatings on lenses, wear-resistant coatings on tools, and thin films in microelectronics.
-
Advantages of PVD as a Bottom-Up Technique:
- Precision: PVD allows for precise control over film thickness and composition, making it ideal for applications requiring high accuracy.
- Uniformity: The process produces highly uniform films, which are essential for applications in optics and electronics.
- Versatility: PVD can deposit a wide range of materials, including metals, ceramics, and composites, making it suitable for various industrial applications.
-
Comparison with Other Deposition Techniques:
- Unlike Chemical Vapor Deposition (CVD), which involves chemical reactions to deposit material, PVD relies on physical processes. This distinction makes PVD more suitable for materials that are sensitive to chemical reactions or require high purity.
In summary, Physical Vapor Deposition is a bottom-up fabrication technique that builds thin films by depositing material atom by atom or molecule by molecule. Its precision, uniformity, and versatility make it a preferred method in many high-tech industries.
Summary Table:
Aspect | Details |
---|---|
Fabrication Type | Bottom-Up (builds structures by adding material layer by layer) |
Key Steps | Evaporation, Transportation, Condensation |
Applications | Semiconductors, Optics, Coatings |
Advantages | Precision, Uniformity, Versatility, High-Quality Films |
Comparison with CVD | PVD relies on physical processes, not chemical reactions |
Discover how PVD can enhance your projects—contact our experts today for tailored solutions!