PVD (Physical Vapor Deposition) coatings are renowned for their hardness, wear resistance, and durability, making them highly resistant to scratches under many conditions. However, they are not entirely scratch-proof. The scratch resistance of PVD coatings depends on factors such as the type of coating material, the substrate it is applied to, and the environmental conditions. While PVD coatings significantly enhance the surface hardness and wear resistance of materials, they can still be scratched by harder substances or under extreme mechanical stress. Their thinness (0.5–5 microns) and high adhesion to the substrate contribute to their durability, but they are not impervious to all forms of abrasion or damage.
Key Points Explained:
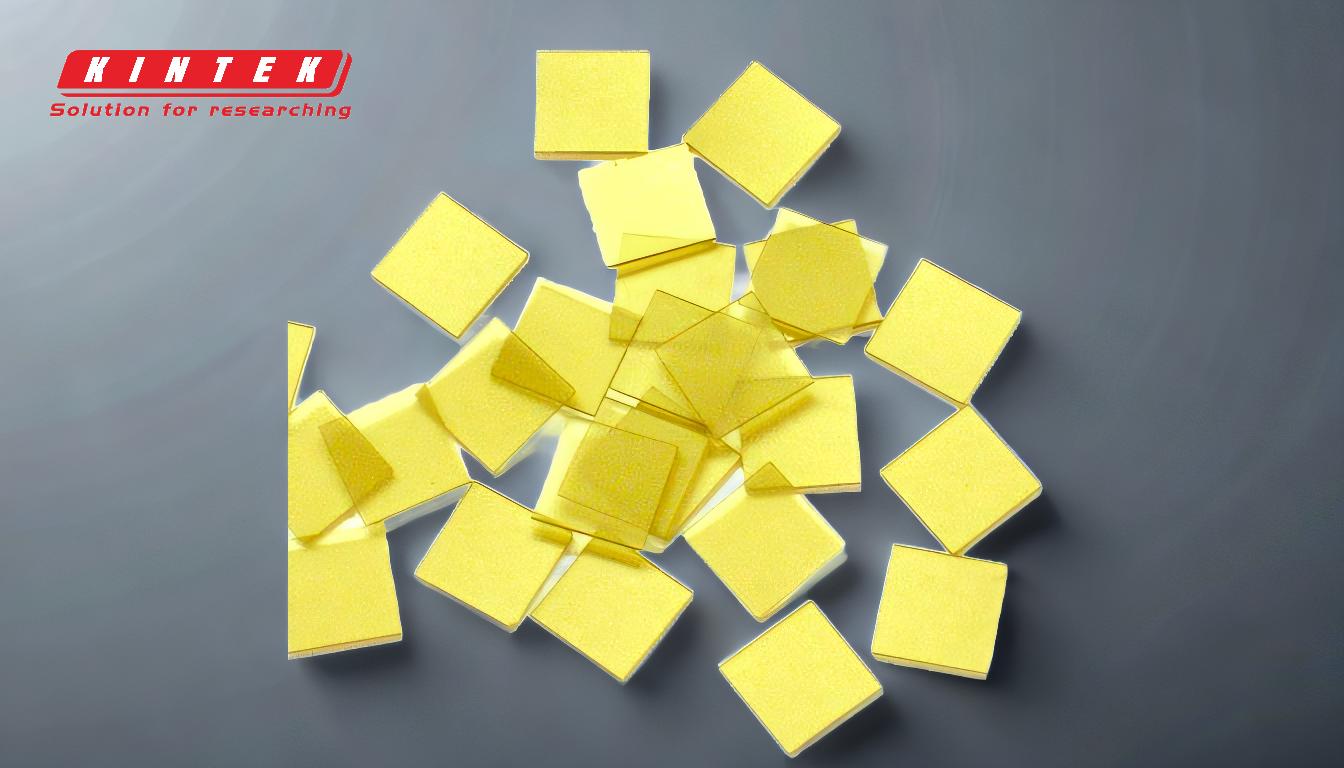
-
PVD Coatings Are Highly Scratch-Resistant but Not Scratch-Proof
- PVD coatings are known for their high hardness, which makes them resistant to scratches and wear. However, "scratch-proof" implies complete immunity to scratching, which is not the case.
- The hardness of PVD coatings, often measured on the Vickers scale, makes them more resistant to scratches than many untreated materials. For example, coatings like TiN (Titanium Nitride) and CrN (Chromium Nitride) are exceptionally hard and durable.
- Despite their hardness, PVD coatings can still be scratched by materials or objects that are harder than the coating itself, such as diamonds or certain ceramics.
-
Thinness and Adhesion Contribute to Durability
- PVD coatings are extremely thin, ranging from 0.5 to 5 microns. This thinness allows them to replicate the original finish of the substrate while providing a protective layer.
- The excellent adhesion of PVD coatings to the substrate ensures that the coating remains intact under normal wear and tear, reducing the likelihood of scratching.
- However, the thinness also means that the coating has limited depth, so repeated abrasion or high-impact forces can eventually wear through the coating.
-
Material and Substrate Influence Scratch Resistance
- The scratch resistance of a PVD coating is influenced by the material used for the coating and the substrate it is applied to. For example, TiN coatings are harder and more scratch-resistant than some other coatings.
- The substrate material also plays a role. A harder substrate will provide better support for the PVD coating, enhancing its overall scratch resistance.
- In some cases, the combination of a PVD coating with a specific substrate can significantly improve the material's fatigue limit and endurance, as seen with TiN coatings on Ti-6Al-4V alloy.
-
Environmental and Application Factors
- The environment in which the coated material is used affects its scratch resistance. For example, exposure to abrasive particles or harsh chemicals can reduce the coating's effectiveness over time.
- PVD coatings are ideal for applications in industries like automotive, aerospace, and medical, where wear resistance and durability are critical. However, in extreme conditions, even PVD coatings can be compromised.
- The coating's performance on complex geometries, such as the back and sides of tools, may be less effective due to limitations in the deposition process, which can affect scratch resistance in those areas.
-
Advantages and Limitations
-
Advantages:
- High hardness and wear resistance.
- Excellent adhesion to the substrate.
- Corrosion and oxidation resistance.
- Enhanced aesthetic appearance without the need for additional polishing.
-
Limitations:
- Not entirely scratch-proof, especially against harder materials.
- Thin coatings may wear through under extreme conditions.
- Performance may vary on complex geometries or uneven surfaces.
-
Advantages:
-
Applications Where Scratch Resistance Matters
- PVD coatings are widely used in industries where scratch resistance is critical, such as:
- Automotive: For components like piston rings and engine parts.
- Aerospace: For turbine blades and other high-stress components.
- Medical: For surgical instruments and implants.
- Consumer Goods: For watch cases, smartphone frames, and decorative items.
- In these applications, PVD coatings provide a balance of durability, aesthetics, and functionality, though they are not immune to all forms of damage.
- PVD coatings are widely used in industries where scratch resistance is critical, such as:
In conclusion, while PVD coatings are highly scratch-resistant due to their hardness, wear resistance, and excellent adhesion, they are not completely scratch-proof. Their performance depends on the coating material, substrate, and environmental conditions. For most practical applications, PVD coatings offer significant protection against scratches and wear, making them a valuable choice for enhancing the durability and longevity of various materials and components.
Summary Table:
Key Aspect | Details |
---|---|
Scratch Resistance | Highly resistant but not scratch-proof; depends on material and substrate. |
Coating Thickness | 0.5–5 microns, providing durability while maintaining substrate finish. |
Adhesion | Excellent adhesion ensures long-lasting protection under normal conditions. |
Material Influence | TiN and CrN coatings offer superior hardness and scratch resistance. |
Environmental Factors | Harsh conditions or abrasive particles can reduce effectiveness. |
Applications | Automotive, aerospace, medical, and consumer goods industries. |
Advantages | High hardness, wear resistance, corrosion resistance, and aesthetic appeal. |
Limitations | Not entirely scratch-proof; thin coatings may wear under extreme stress. |
Learn how PVD coatings can enhance your product's durability—contact our experts today!