PVD (Physical Vapor Deposition) vacuum plating is indeed a highly effective and beneficial coating method, particularly when compared to traditional electroplating. It offers superior durability, wear resistance, and environmental safety, making it an excellent choice for various applications, including jewelry, industrial tools, and decorative finishes. PVD coatings are known for their high hardness, corrosion resistance, and ability to withstand high temperatures. Additionally, the PVD process is eco-friendly, as it does not release harmful chemicals into the atmosphere. With proper care, PVD-coated items can retain their elegance and functionality for many years, making it a worthwhile investment for both consumers and industries.
Key Points Explained:
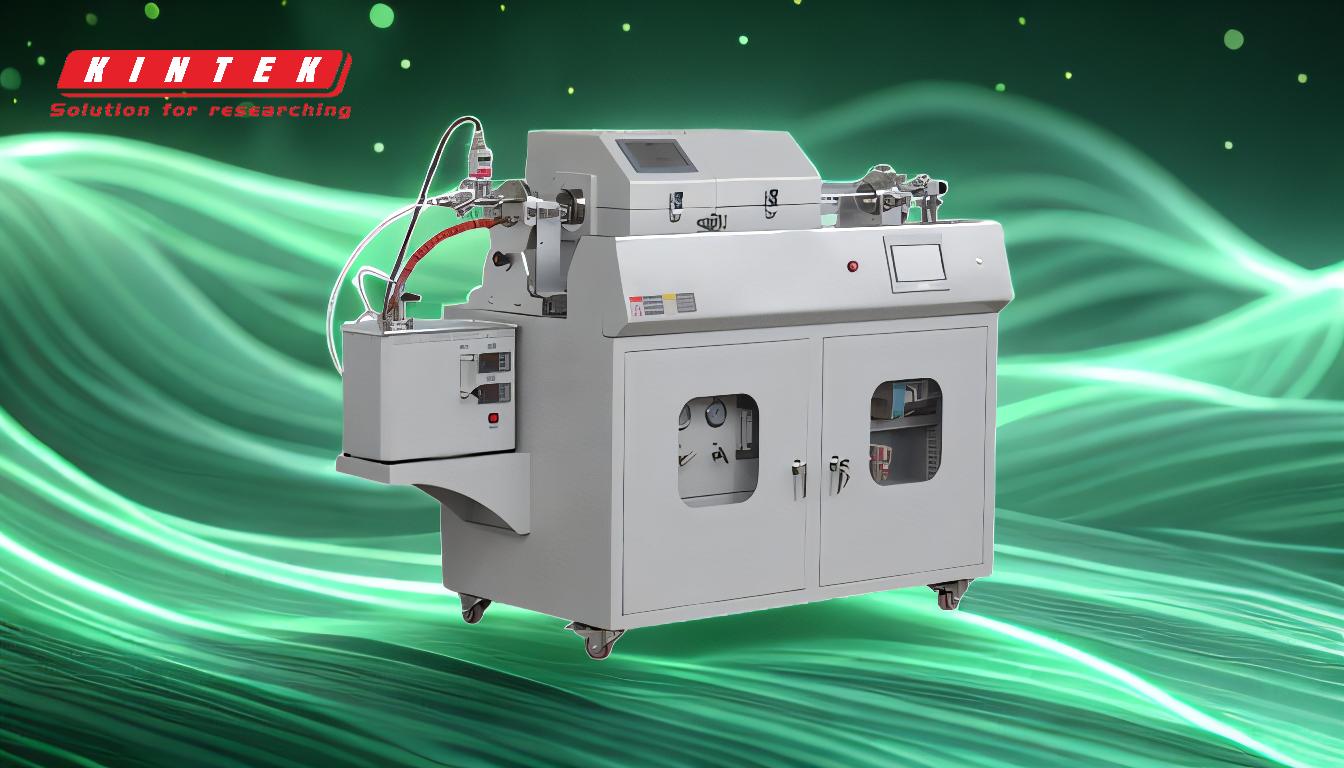
-
Durability and Longevity:
- PVD-coated items, such as jewelry, are significantly more durable than those coated with traditional electroplating. For instance, PVD-coated jewelry can last 3 years or more with everyday wear, whereas electroplated jewelry typically lasts only about 1 year.
- The durability of PVD coatings is attributed to the process of heating a target material until it vaporizes and then depositing the vapor onto the surface in a vacuum environment. This ensures the coating is free from impurities, making it more durable and long-lasting.
-
Superior Wear Resistance and Hardness:
- PVD coatings form a thin, ultra-hard film (3~5μm) with high hardness and wear resistance, which is difficult to achieve with other methods.
- The coatings operate at lower temperatures (around 500 °C), reducing the risk of thermal damage to the substrate. This makes PVD coatings ideal for applications that require interrupted cutting processes, such as milling.
-
Environmental Safety:
- PVD coating is more eco-friendly compared to traditional electroplating and even other coating methods like CVD (Chemical Vapor Deposition). The vacuum-tight chamber process ensures that no harmful chemicals are released into the atmosphere.
- This environmental safety is a significant advantage for industries looking to reduce their ecological footprint while maintaining high-quality finishes.
-
Resistance to Corrosion and Tarnishing:
- Unlike traditional electroplating, which often requires a clear coat that can degrade over time, PVD coatings do not need a clear top coat. This makes them more resistant to fading, tarnishing, and corrosion.
- PVD coatings are particularly beneficial for items exposed to harsh environments, as they maintain their appearance and functionality over time.
-
Operational Efficiency:
- PVD coating machines are computer-controlled, allowing operators to carry out other tasks simultaneously. This reduces production costs and turnaround time, making the process more efficient for various industries.
- The ability to automate and control the coating process with precision ensures consistent quality and reduces the likelihood of defects.
-
Aesthetic and Functional Longevity:
- PVD plating technology not only enhances the aesthetic appeal of items but also ensures their longevity. Proper care and maintenance can help PVD-plated items retain their elegance and attractiveness for many years.
- This combination of flair and durability makes PVD coatings a preferred choice for both decorative and functional applications.
In summary, PVD vacuum plating is a superior coating method that offers numerous advantages over traditional electroplating. Its durability, wear resistance, environmental safety, and aesthetic longevity make it an excellent choice for a wide range of applications. Whether for jewelry, industrial tools, or decorative finishes, PVD coatings provide a reliable and long-lasting solution that meets the needs of both consumers and industries.
Summary Table:
Key Benefits | Details |
---|---|
Durability and Longevity | PVD-coated items last 3+ years, outperforming electroplating (1 year). |
Wear Resistance and Hardness | Ultra-hard film (3~5μm) with high hardness, ideal for interrupted cutting. |
Environmental Safety | Eco-friendly process with no harmful chemical emissions. |
Corrosion Resistance | No clear top coat needed, resistant to fading, tarnishing, and corrosion. |
Operational Efficiency | Computer-controlled, reduces production costs and turnaround time. |
Aesthetic Longevity | Enhances appearance and ensures long-lasting elegance with proper care. |
Upgrade your products with PVD vacuum plating—contact us today to learn more!