Sintering, a process that involves heating materials to high temperatures to form a solid mass, has both environmentally friendly and harmful aspects depending on the materials and processes used. While some forms of sintering, such as metal sintering, are considered green technologies due to minimal emissions, other processes involving metal and ceramic nanoparticles can release toxic fumes and require stringent safety measures. The environmental impact of sintering is also influenced by governmental regulations aimed at controlling emissions and ensuring safe handling of materials. Overall, the sustainability of sintering depends on the specific materials, processes, and adherence to environmental and safety standards.
Key Points Explained:
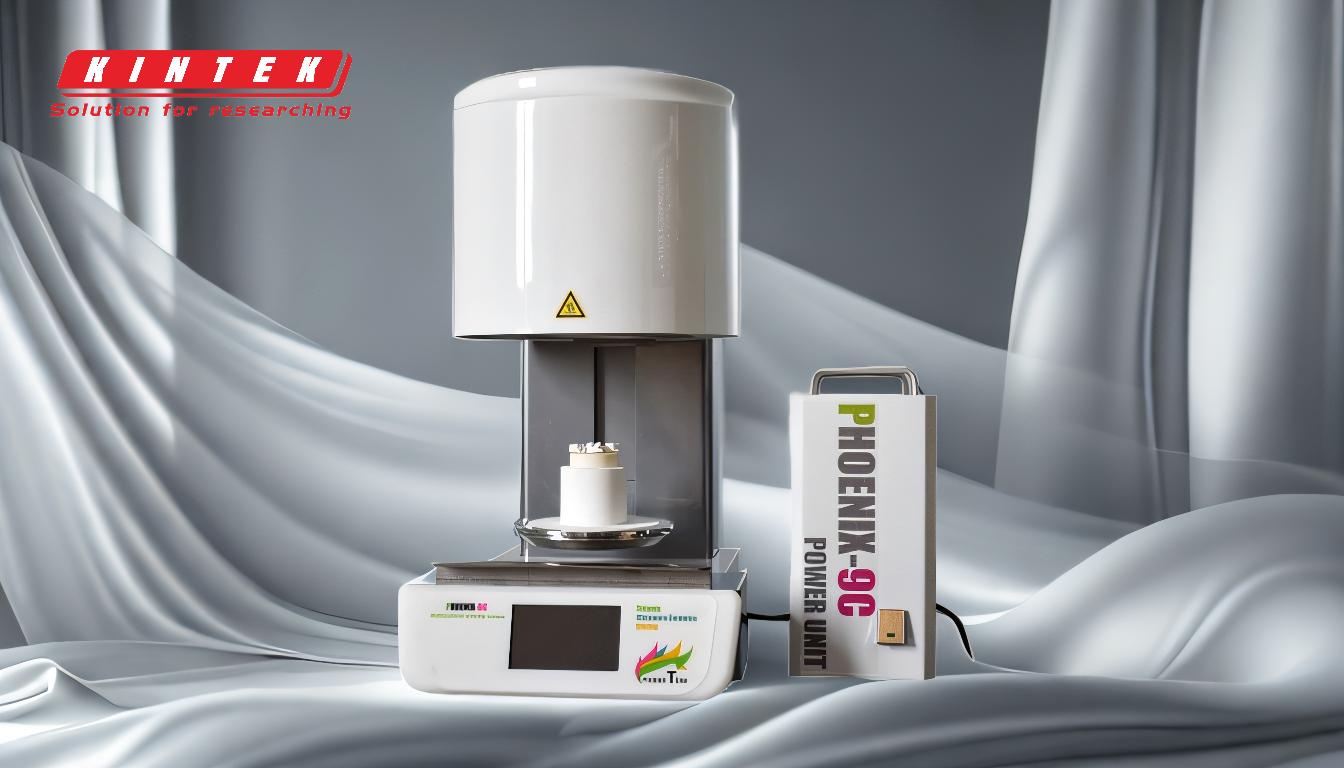
-
Environmental Impact of High-Temperature Processing:
- Sintering typically involves heating materials to high temperatures, which can release harmful emissions into the environment. These emissions may include toxic fumes, particulate matter, and greenhouse gases, depending on the materials being processed.
- The release of such emissions has led to increased scrutiny and the implementation of governmental norms and policies aimed at reducing environmental harm. These regulations can affect production rates and operational practices in the sintering industry.
-
Variability Based on Materials and Processes:
- The environmental friendliness of sintering varies significantly depending on the materials and specific processes used. For example:
- "Green" Processes: Some sintering processes, particularly those involving non-toxic materials, are considered environmentally friendly and do not produce harmful emissions.
- Metal and Ceramic Nanoparticles: These materials can pose medical and environmental risks if not handled properly. They may release toxic fumes during the sintering process, requiring advanced safety measures such as proper ventilation and protective equipment.
- The environmental friendliness of sintering varies significantly depending on the materials and specific processes used. For example:
-
Metal Sintering as a Green Technology:
- Metal sintering is often highlighted as an environmentally friendly option because it generally produces minimal harmful emissions. This makes it an attractive choice for companies aiming to reduce their environmental footprint.
- The lack of harmful emissions during metal sintering aligns with sustainability goals and can help companies comply with environmental regulations more easily.
-
Safety and Regulatory Compliance:
- The sintering process, especially when involving high temperatures and potentially hazardous materials, requires strict adherence to safety protocols. Proper ventilation, protective equipment, and waste management are essential to mitigate environmental and health risks.
- Compliance with governmental norms and policies is critical for maintaining environmentally friendly operations. These regulations often dictate emission limits, material handling procedures, and waste disposal methods, influencing the overall sustainability of sintering practices.
-
Balancing Production and Environmental Concerns:
- While sintering offers significant advantages in terms of material efficiency and product quality, its environmental impact must be carefully managed. Companies must balance production goals with the need to minimize emissions and comply with environmental regulations.
- Innovations in sintering technology, such as the development of cleaner processes and the use of less hazardous materials, can further enhance its environmental friendliness.
In conclusion, sintering can be environmentally friendly, but its impact depends on the materials, processes, and adherence to safety and environmental regulations. Metal sintering, in particular, stands out as a green technology, while other forms of sintering require careful management to mitigate environmental and health risks.
Summary Table:
Aspect | Details |
---|---|
Environmental Impact | High-temperature processing can release toxic fumes, particulate matter, and greenhouse gases. |
Green Processes | Metal sintering is eco-friendly with minimal emissions. |
Hazardous Materials | Metal and ceramic nanoparticles may release toxic fumes, requiring safety measures. |
Regulatory Compliance | Governmental norms control emissions, material handling, and waste disposal. |
Sustainability | Depends on materials, processes, and adherence to safety and environmental standards. |
Learn how to optimize sintering for sustainability—contact our experts today!