Vacuum metalizing and chrome plating are two distinct surface finishing techniques, each with its own advantages and limitations. Vacuum metalizing involves depositing a thin layer of metal, such as aluminum, onto a substrate in a vacuum chamber, while chrome plating involves electroplating a layer of chromium onto a surface. The choice between the two depends on factors such as cost, durability, environmental impact, and application requirements. Vacuum metalizing is often more cost-effective, environmentally friendly, and suitable for non-conductive materials, but it may lack the durability and corrosion resistance of chrome plating. Chrome plating, on the other hand, offers superior hardness and wear resistance but is more expensive and involves hazardous chemicals.
Key Points Explained:
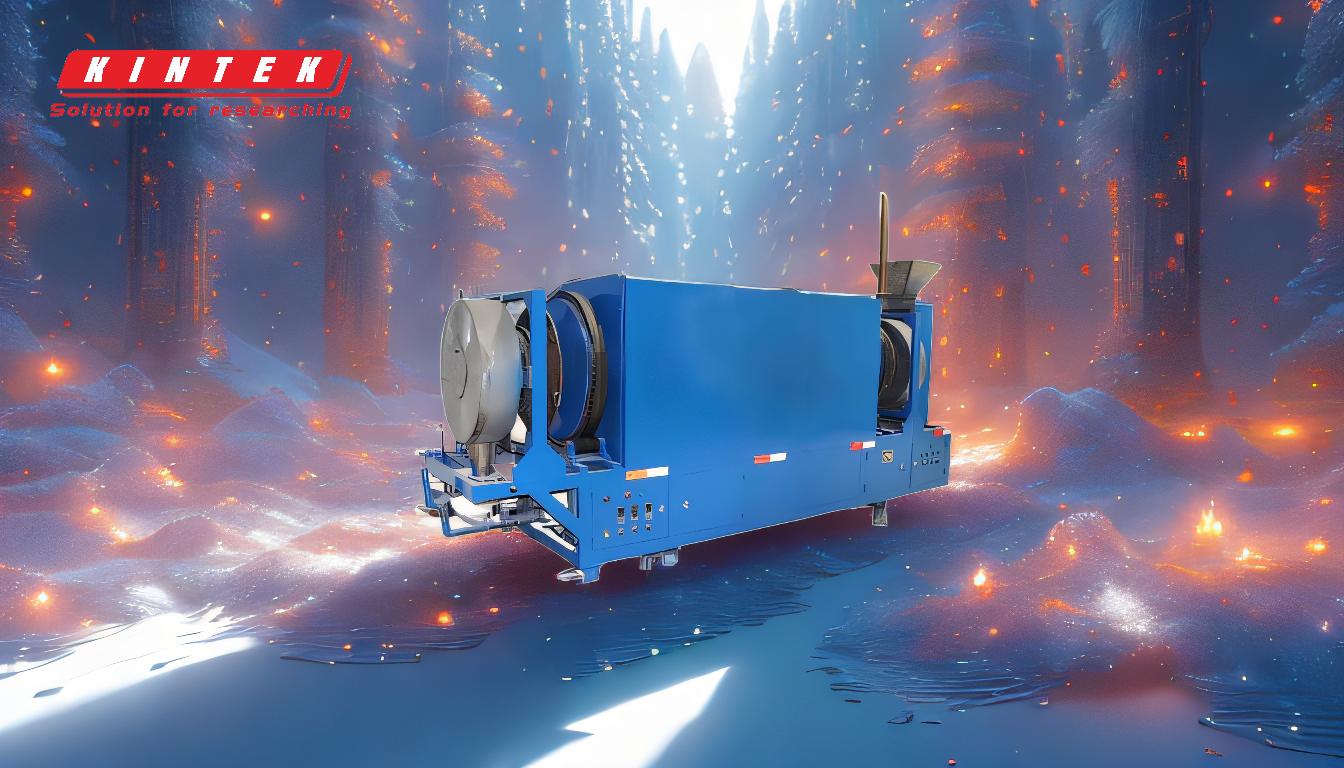
-
Process Overview:
- Vacuum Metalizing: This process involves placing the substrate in a vacuum chamber, heating the metal (typically aluminum) until it vaporizes, and then allowing the vapor to condense onto the substrate, forming a thin, uniform metal layer. It is commonly used for decorative finishes and reflective coatings.
- Chrome Plating: This is an electrochemical process where chromium is deposited onto a conductive surface through electrolysis. It is widely used for both decorative and functional purposes, such as improving wear resistance and corrosion protection.
-
Cost Comparison:
- Vacuum Metalizing: Generally more cost-effective due to lower material costs and faster processing times. It is particularly economical for large-scale production runs.
- Chrome Plating: More expensive due to the cost of chromium, the complexity of the electroplating process, and the need for hazardous waste management.
-
Durability and Performance:
- Vacuum Metalizing: The metal layer is thin and may not be as durable as chrome plating. It is more prone to scratching and wear, making it less suitable for high-stress applications.
- Chrome Plating: Offers superior hardness, wear resistance, and corrosion protection. It is ideal for applications requiring long-term durability, such as automotive parts and industrial equipment.
-
Environmental Impact:
- Vacuum Metalizing: Considered more environmentally friendly as it does not involve hazardous chemicals and produces minimal waste. The process is also energy-efficient.
- Chrome Plating: Involves the use of toxic chemicals, such as hexavalent chromium, which pose significant environmental and health risks. Proper disposal and handling of these chemicals are required, adding to the overall cost and complexity.
-
Material Compatibility:
- Vacuum Metalizing: Can be applied to a wide range of materials, including plastics, glass, and ceramics, making it versatile for various industries.
- Chrome Plating: Limited to conductive materials, primarily metals. Non-conductive materials require an additional conductive coating before plating.
-
Aesthetic and Functional Applications:
- Vacuum Metalizing: Often used for decorative purposes, such as automotive trim, consumer electronics, and packaging. It provides a high-quality, reflective finish but may not be suitable for functional applications requiring high durability.
- Chrome Plating: Used for both decorative and functional applications. It provides a bright, mirror-like finish and is commonly used in automotive, aerospace, and industrial applications where durability is critical.
-
Thickness and Uniformity:
- Vacuum Metalizing: Produces a very thin and uniform metal layer, typically in the range of nanometers to micrometers. This makes it suitable for applications where weight and precision are important.
- Chrome Plating: Can achieve thicker coatings, which are necessary for applications requiring enhanced wear resistance and corrosion protection. However, achieving uniform thickness can be challenging, especially on complex geometries.
-
Maintenance and Repair:
- Vacuum Metalizing: Easier to repair or re-coat if the surface is damaged. The process can be repeated without significant material loss.
- Chrome Plating: Repairing chrome-plated surfaces can be more complex and costly, often requiring complete stripping and re-plating.
-
Industry Standards and Regulations:
- Vacuum Metalizing: Generally complies with environmental regulations due to its cleaner process. It is also easier to adapt to changing regulatory requirements.
- Chrome Plating: Subject to stringent environmental regulations due to the use of hazardous materials. Compliance can be costly and requires ongoing monitoring and reporting.
-
Conclusion:
- Vacuum Metalizing: Best suited for applications where cost, environmental impact, and versatility are primary concerns. It is ideal for decorative finishes and lightweight applications.
- Chrome Plating: Preferred for applications requiring high durability, wear resistance, and corrosion protection. Despite its higher cost and environmental impact, it remains the go-to choice for demanding industrial applications.
In summary, the choice between vacuum metalizing and chrome plating depends on the specific requirements of the application, including cost, durability, environmental considerations, and material compatibility. Each method has its strengths and limitations, making them suitable for different use cases.
Summary Table:
Aspect | Vacuum Metalizing | Chrome Plating |
---|---|---|
Process | Deposits metal (e.g., aluminum) in a vacuum chamber. | Electroplates chromium onto conductive surfaces. |
Cost | More cost-effective, especially for large-scale production. | More expensive due to material and hazardous waste management costs. |
Durability | Thin layer, less durable; prone to scratching and wear. | Superior hardness, wear resistance, and corrosion protection. |
Environmental Impact | Environmentally friendly; no hazardous chemicals, minimal waste. | Involves toxic chemicals (e.g., hexavalent chromium); strict regulations apply. |
Material Compatibility | Works on plastics, glass, ceramics, and more. | Limited to conductive materials; requires pre-treatment for non-conductive items. |
Applications | Decorative finishes (e.g., automotive trim, packaging). | Decorative and functional (e.g., automotive, aerospace, industrial). |
Thickness & Uniformity | Thin, uniform layers (nanometers to micrometers). | Thicker coatings; uniform thickness can be challenging. |
Maintenance & Repair | Easier to repair or re-coat. | Complex and costly to repair; often requires stripping and re-plating. |
Not sure which surface finish is best for your project? Contact our experts today for personalized advice!