Sintering is a widely used process in manufacturing, particularly in metal and ceramic production, offering several advantages such as improved material properties, cost efficiency, and flexibility. However, it also has some disadvantages, including limitations in material selection and potential challenges in achieving uniform results. Below, we explore the key advantages and disadvantages of sintering, with a focus on the role of sintering furnaces in optimizing the process.
Key Points Explained:
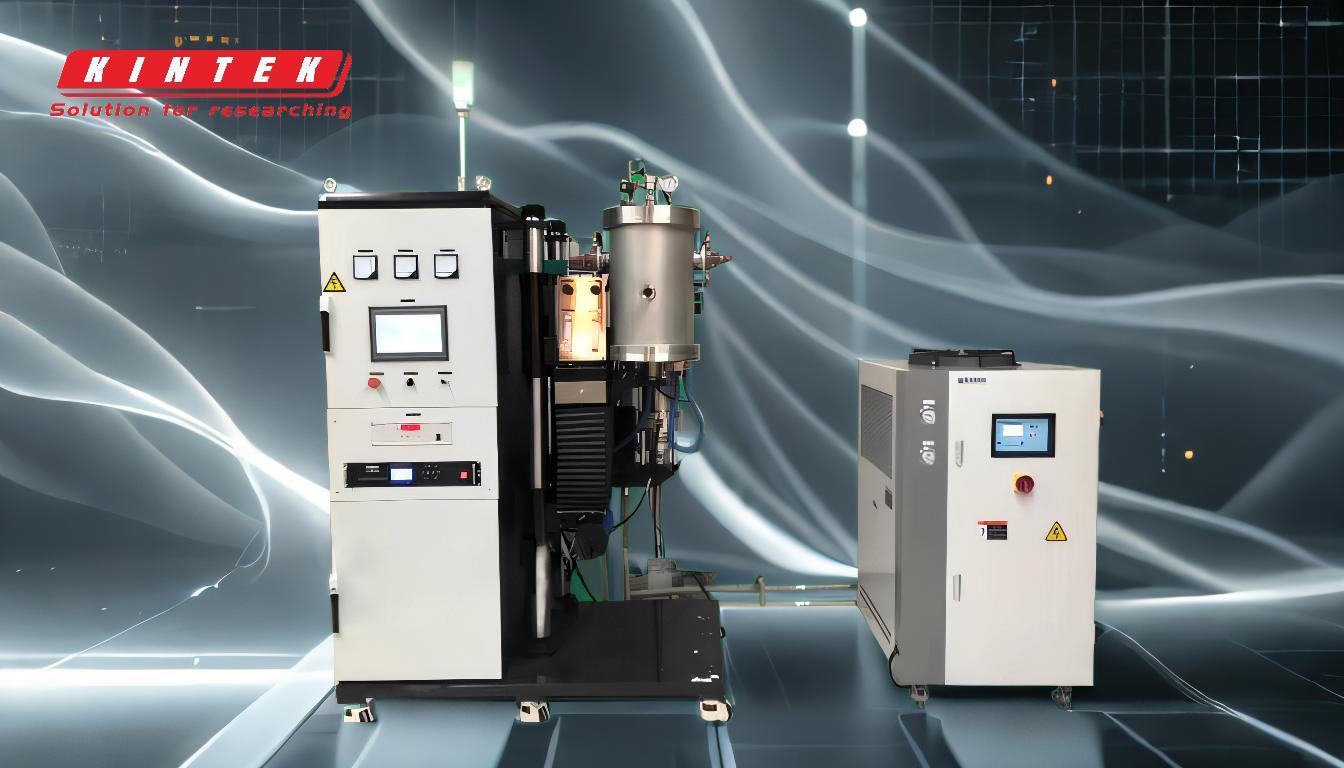
-
Advantages of Sintering:
-
Superior Material Properties:
- Sintering, especially in a sintering furnace, enhances material density, wear resistance, and strength. Vacuum sintering, for example, reduces contamination from atmospheric elements like oxygen and nitrogen, preventing adverse reactions such as oxidation and nitriding. This results in cleaner, brighter components with fewer imperfections.
-
Flexibility and Precision:
- Modern sintering furnaces offer high precision in temperature and pressure control, enabling consistent quality and adaptability to various materials. Programmable stages allow users to adjust parameters like temperature, ramp rates, and hold times, optimizing translucency and saving time during the sintering process.
-
Economic Benefits:
- Sintering reduces production cycles and labor costs by consolidating multiple steps into a single process. For instance, dental sintering furnaces can complete multiple steps simultaneously, improving efficiency and reducing operational expenses.
-
Versatility in Applications:
- Sintering is used in additive manufacturing with 3D metal printers and for forming refractory metals like tungsten and molybdenum, which have high melting temperatures and cannot be processed through traditional melting methods.
-
Superior Material Properties:
-
Disadvantages of Sintering:
-
Material Limitations:
- Sintering is not suitable for all materials. Some materials may not achieve the desired density or properties, limiting their applicability in certain industries.
-
Uniformity Challenges:
- Achieving uniform results can be difficult, especially for complex or porous structures. Variations in temperature or pressure within the sintering furnace can lead to inconsistencies in the final product.
-
High Initial Costs:
- The equipment required for sintering, such as advanced sintering furnaces, can be expensive. While the process offers long-term economic benefits, the initial investment may be a barrier for smaller manufacturers.
-
Energy Consumption:
- Sintering processes, particularly those requiring high temperatures or vacuum conditions, can be energy-intensive, increasing operational costs and environmental impact.
-
Material Limitations:
-
Role of Sintering Furnaces in Mitigating Disadvantages:
-
Optimized Design:
- Advanced sintering furnaces, such as hot press sintering furnaces, feature high working temperatures, large pressure forces, and effective cooling systems. These design elements help achieve better densification and uniformity, addressing some of the challenges associated with sintering.
-
Closed Environment Benefits:
- Hot press sintering furnaces operate in a closed environment, preventing oxidation and contamination. This not only improves product performance but also reduces the risk of defects caused by external factors.
-
Programmable Controls:
- The ability to program stages in sintering furnaces allows for precise control over the process, minimizing inconsistencies and improving efficiency. This is particularly beneficial for producing ceramic materials with complex structures.
-
Optimized Design:
In summary, sintering offers significant advantages in terms of material properties, cost efficiency, and versatility, but it also presents challenges related to material limitations, uniformity, and initial costs. The use of advanced sintering furnaces plays a crucial role in maximizing the benefits while addressing some of the disadvantages, making sintering a valuable process in modern manufacturing.
Summary Table:
Aspect | Advantages | Disadvantages |
---|---|---|
Material Properties | Enhanced density, wear resistance, and strength; reduced contamination. | Not suitable for all materials; limitations in density and properties. |
Flexibility & Precision | High precision in temperature/pressure control; programmable stages. | Challenges in achieving uniform results for complex structures. |
Economic Benefits | Reduced production cycles and labor costs; improved efficiency. | High initial costs for advanced sintering furnaces. |
Versatility | Used in additive manufacturing and refractory metal processing. | Energy-intensive processes; increased operational costs. |
Sintering Furnace Role | Optimized design, closed environments, and programmable controls mitigate challenges. |
Discover how sintering furnaces can enhance your manufacturing process—contact us today for expert guidance!