Induction heating is a highly efficient and precise method of heating conductive materials, offering numerous advantages over traditional heating methods. It uses electromagnetic induction to generate heat directly within the material, ensuring uniform heating and reducing energy waste. This technology is widely used in industries such as manufacturing, metallurgy, and electronics due to its speed, precision, and ability to heat specific areas without affecting surrounding materials. Below, we explore the key advantages of induction heating in detail.
Key Points Explained:
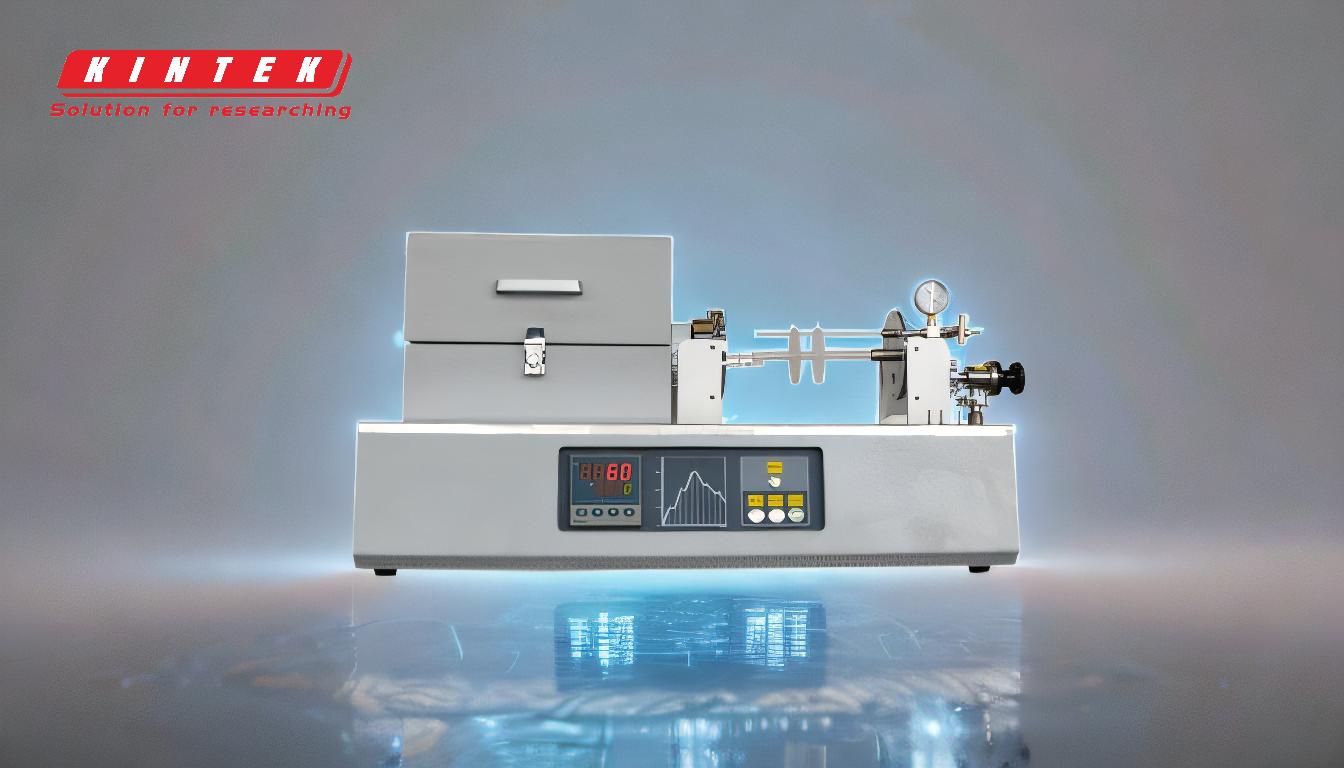
-
Energy Efficiency:
- Induction heating is highly energy-efficient because it generates heat directly within the material, minimizing heat loss to the surrounding environment.
- Unlike traditional heating methods that rely on external heat sources (e.g., flames or hot air), induction heating transfers energy directly to the workpiece, reducing energy consumption by up to 50%.
- This efficiency is particularly beneficial in industrial applications where large-scale heating is required.
-
Precision and Control:
- Induction heating allows for precise control over the heating process, including temperature and heating time.
- The ability to target specific areas of a workpiece ensures that only the intended part is heated, reducing the risk of damage to adjacent components.
- This precision is critical in applications such as hardening, brazing, and annealing, where consistent and accurate heating is essential.
-
Speed and Uniformity:
- Induction heating is significantly faster than traditional methods, as it heats materials almost instantly.
- The electromagnetic field ensures uniform heating throughout the material, eliminating hot spots and cold spots that can occur with other heating techniques.
- This uniformity is particularly important in processes like forging and melting, where consistent material properties are required.
-
Clean and Safe Operation:
- Induction heating is a clean process that does not produce open flames, fumes, or harmful emissions.
- Since the heat is generated internally within the material, there is no direct contact between the heating source and the workpiece, reducing the risk of contamination.
- This makes induction heating ideal for applications in the food, pharmaceutical, and electronics industries, where cleanliness and safety are paramount.
-
Versatility:
- Induction heating can be used with a wide range of conductive materials, including metals like steel, aluminum, and copper.
- It is suitable for various applications, such as hardening, tempering, brazing, soldering, and melting.
- The technology can be adapted to different shapes and sizes of workpieces, making it a versatile solution for diverse industrial needs.
-
Reduced Maintenance and Longevity:
- Induction heating systems have fewer moving parts compared to traditional furnaces, resulting in lower maintenance requirements and longer operational lifespans.
- The absence of open flames and high-temperature external heating elements reduces wear and tear on the equipment.
- This translates to cost savings over time, as fewer repairs and replacements are needed.
-
Environmental Benefits:
- Induction heating is an environmentally friendly technology due to its energy efficiency and lack of emissions.
- It reduces the carbon footprint of industrial processes by minimizing energy waste and eliminating the need for fossil fuels in many cases.
- This aligns with global sustainability goals and makes induction heating a preferred choice for eco-conscious industries.
-
Compact and Space-Saving Design:
- Induction heating systems are typically compact and require less space compared to traditional furnaces or ovens.
- Their modular design allows for easy integration into existing production lines, making them ideal for facilities with limited space.
- This compactness also contributes to faster setup and installation times.
In summary, induction heating offers a range of advantages, including energy efficiency, precision, speed, cleanliness, versatility, and environmental benefits. These features make it a superior choice for many industrial applications, ensuring high-quality results while reducing operational costs and environmental impact. Whether for small-scale or large-scale processes, induction heating provides a reliable and efficient solution for modern manufacturing needs.
Summary Table:
Advantage | Description |
---|---|
Energy Efficiency | Reduces energy consumption by up to 50% with direct heat generation. |
Precision and Control | Enables accurate temperature and heating time control for specific areas. |
Speed and Uniformity | Heats materials instantly with uniform distribution, eliminating hot/cold spots. |
Clean and Safe Operation | No open flames, fumes, or emissions; ideal for food, pharma, and electronics. |
Versatility | Works with various conductive materials and applications like hardening, melting. |
Reduced Maintenance | Fewer moving parts and longer lifespan compared to traditional heating systems. |
Environmental Benefits | Minimizes energy waste and carbon footprint, aligning with sustainability goals. |
Compact Design | Space-saving and modular, suitable for facilities with limited space. |
Ready to enhance your industrial processes with induction heating? Contact us today to learn more!