Induction furnaces are a type of furnace widely used in manufacturing and foundries for melting metals. They operate on the principle of electromagnetic induction, where an alternating current generates a magnetic field that induces eddy currents in the metal, causing it to heat up and melt. Induction furnaces are highly efficient, precise, and environmentally friendly compared to other furnace types. They are commonly used for melting metals like iron, steel, copper, and aluminum. The main types of induction furnaces include coreless induction furnaces, channel induction furnaces, and vacuum induction furnaces, each suited for specific applications and metal types.
Key Points Explained:
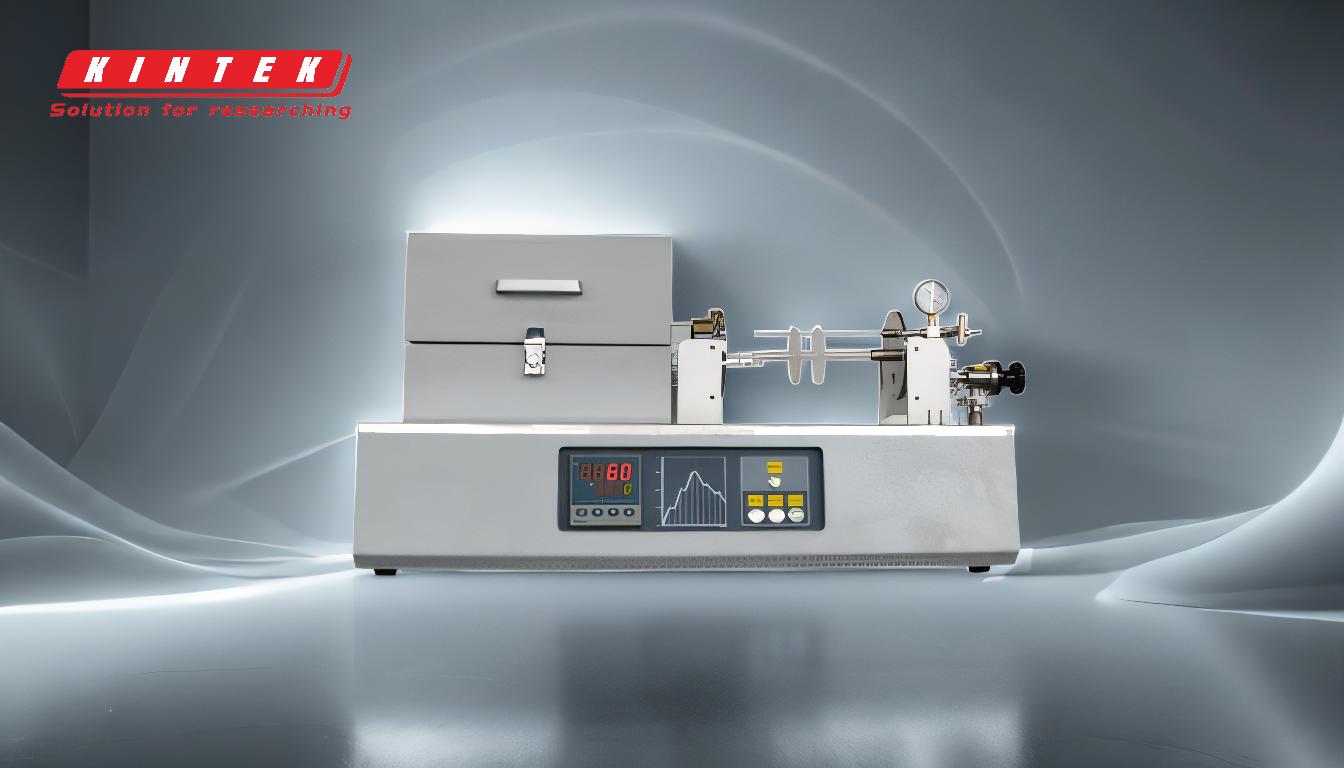
-
Coreless Induction Furnaces:
- Coreless induction furnaces are the most common type of induction furnace. They consist of a refractory-lined crucible surrounded by a water-cooled copper coil. The alternating current in the coil generates a magnetic field, which induces eddy currents in the metal, causing it to heat up and melt.
- These furnaces are highly versatile and can melt a wide range of metals, including iron, steel, copper, and aluminum.
- They are known for their rapid heating rates, precise temperature control, and ability to handle small to medium batch sizes.
- Coreless induction furnaces are widely used in foundries, metal casting, and recycling industries.
-
Channel Induction Furnaces:
- Channel induction furnaces are designed for continuous melting and holding of molten metal. They consist of a refractory-lined channel that contains the molten metal, surrounded by a primary coil that generates the magnetic field.
- These furnaces are particularly suited for applications requiring a constant supply of molten metal, such as in die-casting and continuous casting processes.
- Channel induction furnaces are highly energy-efficient and have a long lifespan due to the lower thermal stress on the refractory lining.
- They are commonly used for melting and holding non-ferrous metals like aluminum, zinc, and copper alloys.
-
Vacuum Induction Furnaces:
- Vacuum induction furnaces are specialized furnaces used for melting and refining high-purity metals and alloys under a vacuum or controlled atmosphere. They are essential for producing materials with stringent quality requirements, such as superalloys, titanium, and specialty steels.
- The vacuum environment prevents oxidation and contamination, ensuring the production of high-quality, defect-free metals.
- These furnaces are widely used in the aerospace, medical, and electronics industries, where material purity and performance are critical.
- Vacuum induction furnaces offer precise control over temperature and atmosphere, making them ideal for advanced metallurgical processes.
-
Advantages of Induction Furnaces:
- Energy Efficiency: Induction furnaces are highly energy-efficient, as they directly heat the metal without the need for a combustion process. This results in lower energy consumption and reduced operating costs.
- Precise Temperature Control: Induction furnaces offer excellent temperature control, allowing for precise melting and holding of metals at specific temperatures.
- Environmental Friendliness: Induction furnaces produce fewer emissions compared to traditional furnaces, making them more environmentally friendly.
- Versatility: Induction furnaces can melt a wide range of metals and alloys, making them suitable for various industrial applications.
- Compact Design: Induction furnaces have a compact design, requiring less space compared to other furnace types.
-
Applications of Induction Furnaces:
- Foundries: Induction furnaces are widely used in foundries for melting and casting metals like iron, steel, and aluminum.
- Metal Recycling: Induction furnaces are commonly used in the recycling industry to melt and refine scrap metal.
- Aerospace and Medical Industries: Vacuum induction furnaces are essential for producing high-purity metals and alloys used in aerospace and medical applications.
- Continuous Casting: Channel induction furnaces are used in continuous casting processes to maintain a constant supply of molten metal.
In conclusion, induction furnaces are a critical component in modern metallurgy and manufacturing, offering a range of types to suit different applications. Coreless induction furnaces are versatile and widely used, channel induction furnaces are ideal for continuous processes, and vacuum induction furnaces are essential for high-purity applications. Each type offers unique advantages, making induction furnaces a preferred choice for melting and refining metals in various industries.
Summary Table:
Type | Key Features | Applications |
---|---|---|
Coreless Induction | Rapid heating, precise temperature control, versatile for small to medium batches | Foundries, metal casting, recycling industries |
Channel Induction | Continuous melting, energy-efficient, long lifespan | Die-casting, continuous casting, non-ferrous metals (aluminum, zinc, copper) |
Vacuum Induction | High-purity melting, oxidation prevention, precise atmosphere control | Aerospace, medical, electronics industries (superalloys, titanium, specialty steels) |
Need the right induction furnace for your application? Contact our experts today!