Extrusion is a manufacturing process where materials, typically metals, plastics, or food products, are forced through a die to create objects with a fixed cross-sectional profile. This process is widely used across industries due to its efficiency, versatility, and ability to produce complex shapes. Examples of extruded products include everyday items like pasta, pipes, window frames, and aluminum cans, as well as industrial components such as gears and railings. These examples highlight the adaptability of extrusion in creating both simple and intricate designs across various materials.
Key Points Explained:
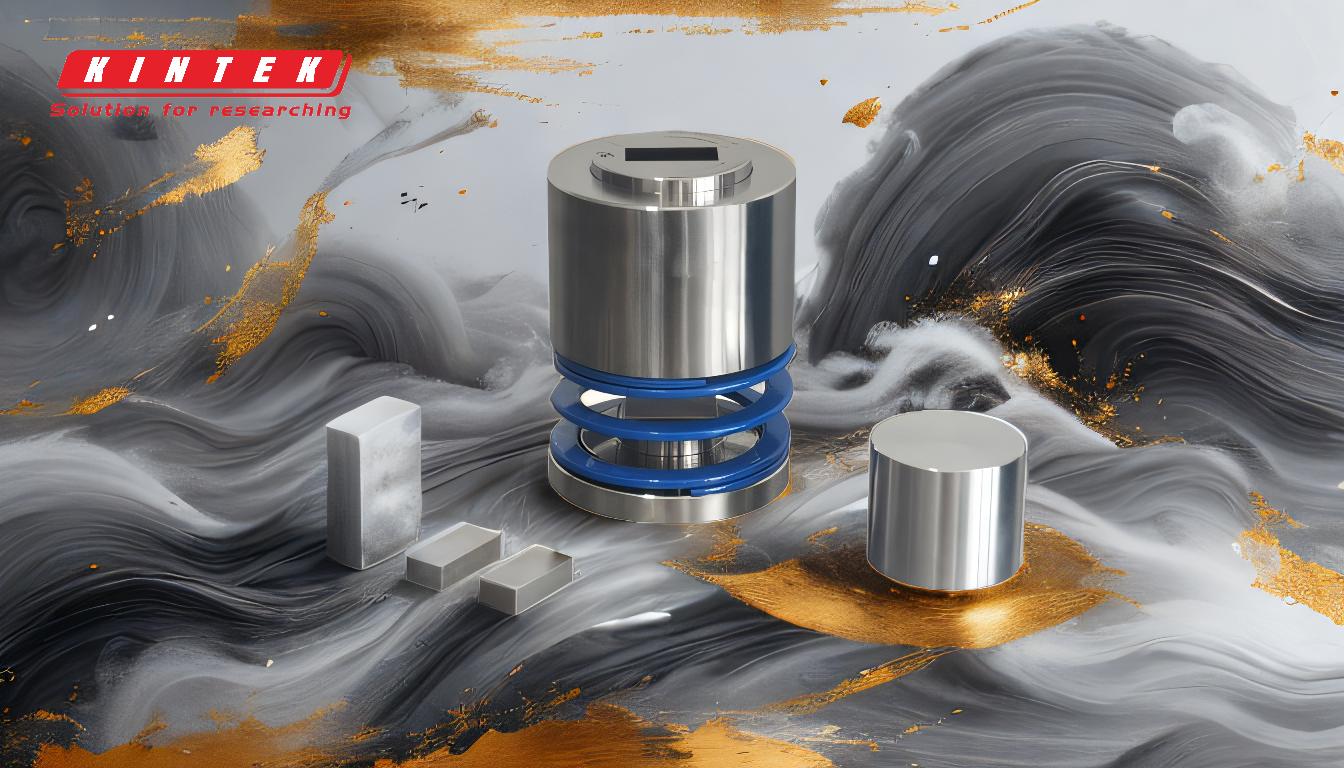
-
Definition of Extrusion:
- Extrusion is a process where material is pushed or drawn through a die to create objects with a specific cross-sectional shape.
- It is commonly used for metals, plastics, and food products due to its ability to produce consistent and complex shapes efficiently.
-
Examples of Extruded Products:
-
Food Products:
- Pasta: Extrusion is used to create various pasta shapes, from spaghetti to penne, by forcing dough through dies.
- Snack Foods: Many snacks, such as pretzels and cereal, are made using extrusion to achieve their unique shapes and textures.
-
Construction and Industrial Materials:
- Pipes: Plastic and metal pipes are often extruded to ensure uniformity and strength.
- Window Frames and Panes: Extrusion is used to create durable and precise profiles for windows.
- Railings: Metal railings for stairs and balconies are often extruded to achieve consistent and decorative designs.
-
Automotive and Consumer Goods:
- Aluminum Cans: Extrusion is used in the production of aluminum cans, ensuring lightweight and durable packaging.
- Windshield Wipers: The metal or plastic components of windshield wipers are often extruded for precision and durability.
- Shower Stalls: Plastic or metal shower enclosures are made using extrusion to ensure watertight and durable designs.
-
Mechanical Components:
- Gears: Extrusion is used to create gears with precise dimensions and consistent quality.
-
Food Products:
-
Advantages of Extrusion:
- Versatility: Extrusion can produce a wide range of shapes and sizes, from simple tubes to complex profiles.
- Efficiency: The process is highly efficient, allowing for continuous production with minimal waste.
- Material Flexibility: Extrusion works with various materials, including metals, plastics, and food products.
- Precision: Extrusion ensures consistent dimensions and high-quality finishes, making it ideal for applications requiring tight tolerances.
-
Applications Across Industries:
- Extrusion is used in industries such as construction, automotive, food production, and consumer goods due to its adaptability and cost-effectiveness.
- It enables the production of lightweight, durable, and aesthetically pleasing products.
By understanding the extrusion process and its applications, purchasers of equipment and consumables can make informed decisions about the materials and products they choose for their specific needs.
Summary Table:
Aspect | Details |
---|---|
Definition | Process of forcing material through a die to create fixed cross-sectional shapes. |
Materials | Metals, plastics, food products. |
Examples | Pasta, pipes, window frames, aluminum cans, gears, railings. |
Advantages | Versatility, efficiency, material flexibility, precision. |
Applications | Construction, automotive, food production, consumer goods. |
Interested in leveraging extrusion for your projects? Contact us today to learn more!