The production and application of carbon nanotubes (CNTs) face several challenges, including concerns about material quality, environmental impact, and scalability. Emerging methods like producing CNTs from green feedstocks (e.g., carbon dioxide captured by electrolysis in molten salts or methane pyrolysis) aim to address sustainability concerns but still face hurdles in ensuring high-quality output and minimizing greenhouse gas emissions. Additionally, integrating CNTs into critical applications such as lithium-ion batteries, composites, and transparent conductive films requires overcoming technical and supply chain challenges. Innovations in production, functionalization, and hybrid material development are key to overcoming these barriers, alongside reducing energy consumption and ecotoxicity throughout the CNT lifecycle.
Key Points Explained:
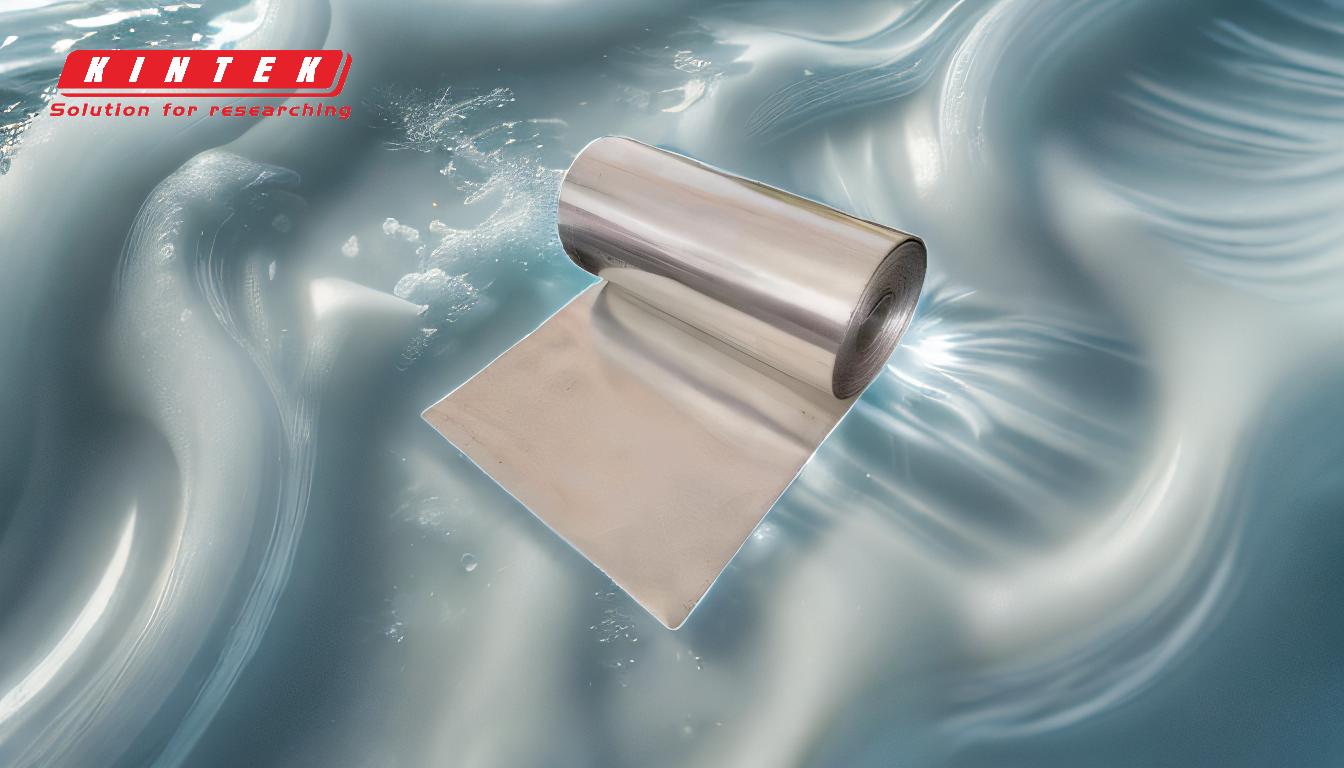
-
Challenges in Production from Green Feedstocks:
- Producing CNTs from green feedstocks, such as carbon dioxide captured by electrolysis in molten salts, is promising for sustainability but raises concerns about the quality of the material produced.
- Methane pyrolysis, which converts methane into hydrogen and solid carbon, is another method being explored. However, it requires careful handling to prevent greenhouse gas emissions, which could offset its environmental benefits.
-
Environmental and Cost Concerns in Traditional Methods:
- Traditional methods like laser ablation and arc discharge are less scalable and cost-effective compared to chemical vapor deposition (CVD), the dominant commercial process today.
- Catalytic chemical vapor deposition (CCVD) is widely used due to its structural controllability and cost-effectiveness. However, the synthesis process is a major contributor to potential ecotoxicity impacts, emphasizing the need to limit material and energy consumption and reduce greenhouse gas emissions.
-
Integration into Critical Applications:
- CNTs are increasingly used in lithium-ion batteries (both cathodes and anodes), composites (conductive polymers, fiber-reinforced polymer composites, concrete, asphalt, metal composites, and tires), and other areas like transparent conductive films, thermal interface materials, and sensors.
- Ensuring consistent quality and performance in these applications requires overcoming technical challenges, such as achieving uniform dispersion in composites and maintaining conductivity in hybrid materials.
-
Innovations in Production and Functionalization:
- Innovations focus on creating CNTs with a very high aspect ratio, forming hybrid products with other additives, and using alternative feedstocks to improve sustainability.
- Developing highly conductive continuous yarns and other advanced forms of CNTs is crucial for expanding their use in high-performance applications.
-
Overcoming Challenges:
- To address quality concerns, research is needed to optimize green feedstock processes and improve the consistency of CNT properties.
- Reducing the environmental impact of CNT production involves adopting energy-efficient methods, minimizing waste, and exploring circular economy approaches.
- Collaboration across the supply chain is essential to ensure the scalability and cost-effectiveness of CNTs in critical applications.
By addressing these challenges through innovation and sustainable practices, the production and application of carbon nanotubes can be significantly improved, unlocking their full potential in advanced technologies.
Summary Table:
Challenges | Solutions |
---|---|
Green feedstock production | Optimize processes for quality, minimize greenhouse gas emissions |
Environmental and cost concerns | Adopt energy-efficient methods, reduce ecotoxicity, and minimize waste |
Integration into critical applications | Improve dispersion in composites, maintain conductivity in hybrid materials |
Innovations in production | Develop high-aspect-ratio CNTs, hybrid materials, and advanced forms |
Overcoming challenges | Collaborate across supply chains, adopt circular economy approaches |
Discover how to overcome carbon nanotube challenges and unlock their potential—contact our experts today!