Sputtering tools are specialized equipment used in the sputtering process, a technique for depositing thin films of materials onto substrates. This process involves bombarding a target material with ions, causing atoms to be ejected and deposited onto a substrate, forming a thin film. Sputtering tools are widely used in industries such as semiconductors, optics, and jewelry due to their ability to deposit a wide variety of materials, including metals, ceramics, and compounds, with high precision. These tools operate in a vacuum environment, utilizing argon plasma to eject target atoms, making them ideal for materials with high melting points or complex compositions.
Key Points Explained:
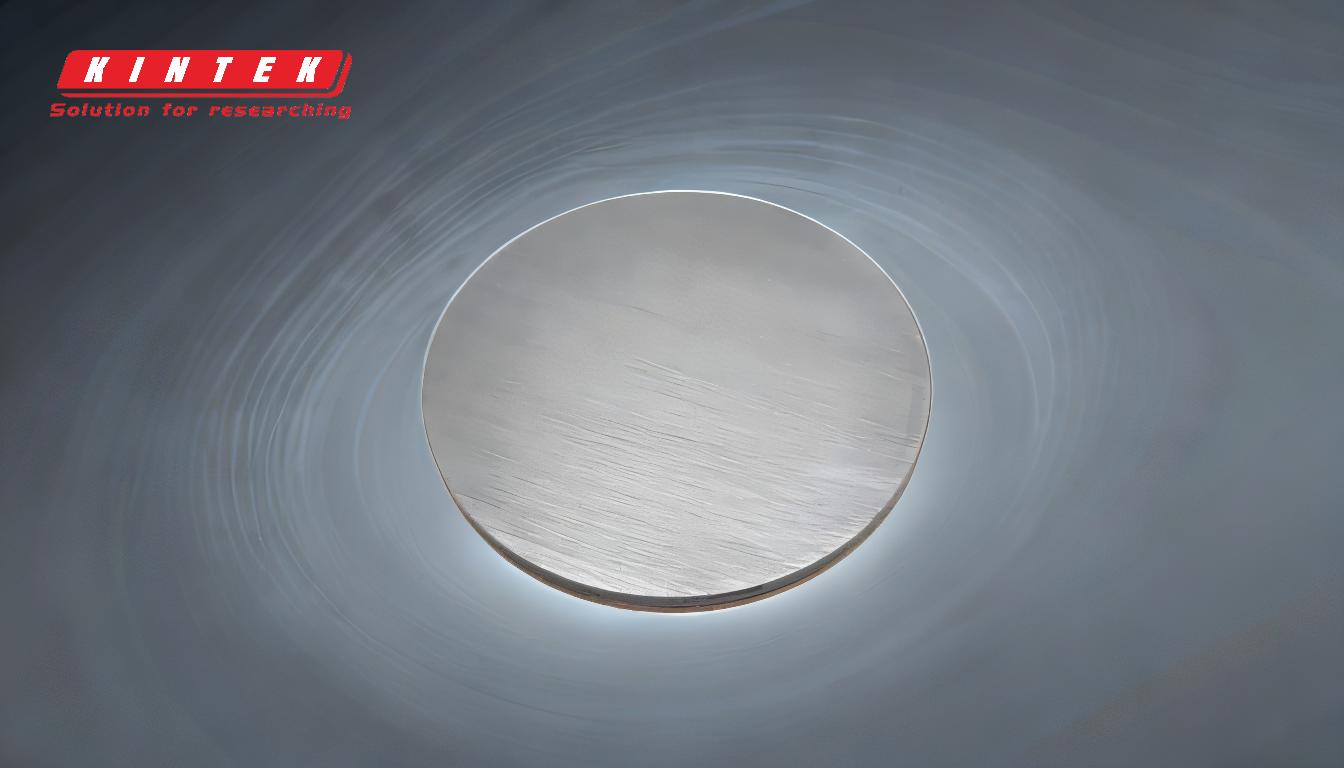
-
Definition and Purpose of Sputtering Tools:
- Sputtering tools are devices designed to perform the sputtering process, which is a physical vapor deposition (PVD) technique.
- Their primary purpose is to deposit thin films of materials onto substrates, enabling the creation of precision products in various industries.
-
How Sputtering Tools Work:
- Vacuum Environment: Sputtering tools operate in a high-vacuum chamber to minimize contamination and ensure precise deposition.
- Argon Plasma Generation: The tool generates argon plasma, which ionizes argon gas to create positively charged argon ions.
- Target Bombardment: These ions are accelerated toward a target material (e.g., a metal ingot), ejecting atoms from the target's surface.
- Film Deposition: The ejected atoms travel through the vacuum and deposit onto a substrate, forming a thin, uniform film.
-
Materials Used in Sputtering:
- Metals: Commonly sputtered metals include gold, silver, copper, and titanium.
- Ceramics and Oxides: Materials like aluminum oxide, titanium oxide, and yttrium oxide are frequently used.
- Alloys and Compounds: Sputtering tools can deposit alloys (e.g., indium tin oxide) and compounds (e.g., tantalum nitride) with precise compositions.
- Specialized Applications: Materials like zirconium nitride and chromium oxide are used for coatings on jewelry, tableware, and industrial components.
-
Applications of Sputtering Tools:
- Semiconductor Industry: Sputtering is used to deposit conductive and insulating layers in microelectronics.
- Optics: Thin films for anti-reflective coatings and mirrors are produced using sputtering tools.
- Jewelry and Tableware: Precious metals like gold and silver are sputtered onto jewelry and cutlery for decorative and functional purposes.
- Industrial Coatings: Sputtering tools are used to apply wear-resistant and corrosion-resistant coatings on tools and machinery.
-
Advantages of Sputtering Tools:
- Precision: Sputtering allows for highly accurate and uniform film deposition, even on complex geometries.
- Versatility: A wide range of materials, including high-melting-point metals and alloys, can be deposited.
- Reactive Sputtering: By introducing reactive gases (e.g., oxygen or nitrogen), compounds like oxides and nitrides can be formed during the deposition process.
- Scalability: Sputtering tools are suitable for both small-scale (e.g., jewelry) and large-scale (e.g., flat glass) applications.
-
Comparison with Other Deposition Methods:
- Chemical Vapor Deposition (CVD): Unlike CVD, which relies on chemical reactions, sputtering is a physical process, making it ideal for materials that are difficult to deposit chemically.
- Vacuum Deposition: Sputtering requires a higher vacuum level than traditional vacuum deposition methods, ensuring cleaner and more precise films.
- Ease of Use: Sputtering tools are often preferred for their ability to handle complex materials and compositions with minimal contamination.
-
Components of a Sputtering Tool:
- Vacuum Chamber: Houses the target, substrate, and plasma generation system.
- Target Material: The source material from which atoms are ejected.
- Substrate Holder: Holds the object onto which the thin film is deposited.
- Plasma Generation System: Creates and controls the argon plasma used for ion bombardment.
- Power Supply: Provides the energy needed to generate and accelerate ions.
-
Future Trends in Sputtering Technology:
- Advanced Materials: Development of new target materials for emerging applications in electronics and renewable energy.
- Automation: Increased use of automation and robotics to enhance precision and reduce human error.
- Sustainability: Efforts to reduce energy consumption and waste in the sputtering process.
In summary, sputtering tools are essential for depositing thin films with high precision and versatility. They are widely used across industries for applications ranging from semiconductor manufacturing to decorative coatings, offering advantages over other deposition methods due to their ability to handle complex materials and produce uniform, high-quality films.
Summary Table:
Key Aspect | Details |
---|---|
Definition | Devices for physical vapor deposition (PVD) of thin films. |
How It Works | Uses argon plasma in a vacuum to eject target atoms onto substrates. |
Materials Used | Metals, ceramics, oxides, alloys, and compounds. |
Applications | Semiconductors, optics, jewelry, industrial coatings. |
Advantages | Precision, versatility, reactive sputtering, scalability. |
Components | Vacuum chamber, target material, substrate holder, plasma system, power. |
Future Trends | Advanced materials, automation, sustainability. |
Ready to enhance your thin-film deposition process? Contact us today to learn more about sputtering tools!