Sintering is a critical process in materials science and manufacturing, used to bond particles together and reduce porosity, thereby enhancing the material's mechanical and physical properties. The three principal sintering processes are solid-state sintering, liquid phase sintering, and viscous sintering. Each process has distinct mechanisms, applications, and advantages, making them suitable for different industrial needs. Understanding these processes is essential for selecting the right sintering method for specific materials and applications. This explanation will delve into the key characteristics, mechanisms, and uses of these sintering processes, providing a comprehensive overview for equipment and consumable purchasers.
Key Points Explained:
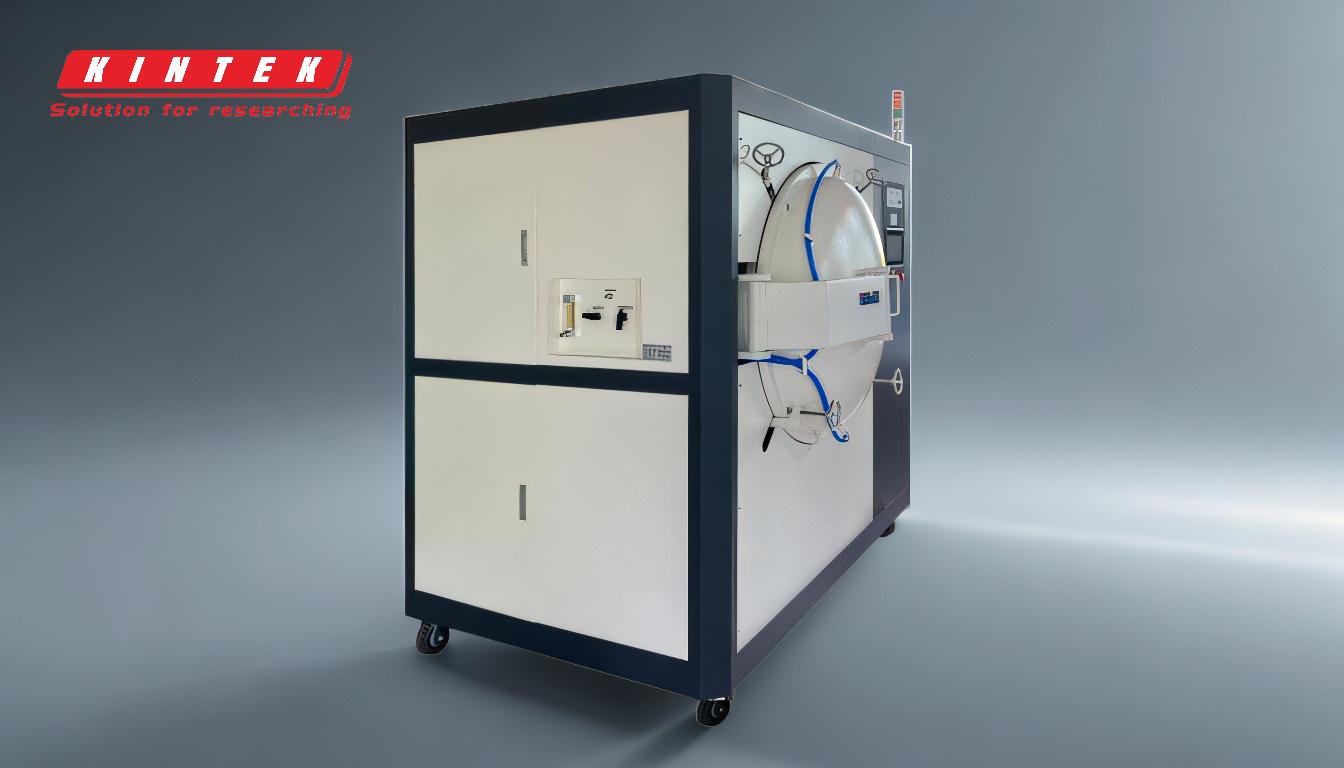
-
Solid-State Sintering:
- Mechanism: Solid-state sintering occurs when powdered materials are heated below their melting point, allowing atoms to diffuse across particle boundaries and bond together. This process relies on solid-state diffusion and does not involve a liquid phase.
- Applications: It is commonly used for ceramics, metals, and composites where maintaining the material's purity and structural integrity is crucial. For example, it is widely used in the production of refractory materials and certain metal components.
- Advantages: This process results in minimal shrinkage and distortion, making it ideal for precision components. It also avoids the complications associated with liquid phases, such as uneven densification.
-
Liquid Phase Sintering:
- Mechanism: Liquid phase sintering involves the presence of a liquid phase during the sintering process. The liquid phase forms when a small amount of additive or binder melts at the sintering temperature, facilitating particle rearrangement and densification.
- Applications: This method is particularly useful for materials that are difficult to sinter in the solid state, such as tungsten carbide and certain ceramics. It is also used in the production of cemented carbides and heavy alloys.
- Advantages: The liquid phase accelerates densification and improves bonding between particles, resulting in higher density and better mechanical properties. However, it requires careful control of temperature and composition to avoid defects.
-
Viscous Sintering:
- Mechanism: Viscous sintering occurs in materials that exhibit viscous flow at high temperatures, such as glasses and certain polymers. The material softens and flows, filling pores and bonding particles together.
- Applications: This process is used in the production of glass ceramics, optical fibers, and certain polymer composites. It is also employed in the manufacturing of advanced ceramics and coatings.
- Advantages: Viscous sintering allows for the creation of complex shapes and fine microstructures. It is particularly effective for materials that require high transparency or specific optical properties.
-
Pressurized vs. Unpressurized Sintering:
- Pressurized Sintering: This involves applying external pressure during the sintering process, often combined with high temperatures. It is used to achieve higher densities and better mechanical properties in materials that are difficult to densify through conventional sintering.
- Unpressurized Sintering: This is the more common method, where sintering occurs without external pressure. It is suitable for a wide range of materials and applications, offering a balance between cost and performance.
-
Special Sintering Techniques:
- Direct Metal Laser Sintering (DMLS): An advanced 3D printing technique that uses a laser to sinter metal powder layer by layer, creating complex metal components with high precision.
- Hot Pressing Sintering: Combines heat and pressure in a single step, often used for advanced ceramics and composites to achieve near-theoretical density.
Understanding these sintering processes and their applications is crucial for selecting the appropriate sintering furnace and consumables for specific manufacturing needs. Each process has unique requirements and benefits, making it essential to match the sintering method with the material properties and desired outcomes.
Summary Table:
Sintering Process | Mechanism | Applications | Advantages |
---|---|---|---|
Solid-State Sintering | Atoms diffuse across particle boundaries without a liquid phase. | Ceramics, metals, composites, refractory materials. | Minimal shrinkage, avoids liquid-phase complications. |
Liquid Phase Sintering | A liquid phase forms to facilitate particle bonding. | Tungsten carbide, cemented carbides, heavy alloys. | Accelerates densification, improves mechanical properties. |
Viscous Sintering | Material softens and flows to fill pores and bond particles. | Glass ceramics, optical fibers, polymer composites. | Enables complex shapes, fine microstructures, and high transparency. |
Need help selecting the right sintering process for your materials? Contact our experts today for personalized guidance!