Heat treatment is a critical process in metallurgy that alters the physical and sometimes chemical properties of steel to achieve desired characteristics such as increased hardness, improved ductility, or enhanced strength. The four primary types of heat treatment for steel are annealing, normalizing, hardening, and tempering. Each method involves heating the steel to a specific temperature, holding it at that temperature for a certain period, and then cooling it at a controlled rate. These processes are essential for tailoring the mechanical properties of steel to meet the demands of various applications, from construction to manufacturing.
Key Points Explained:
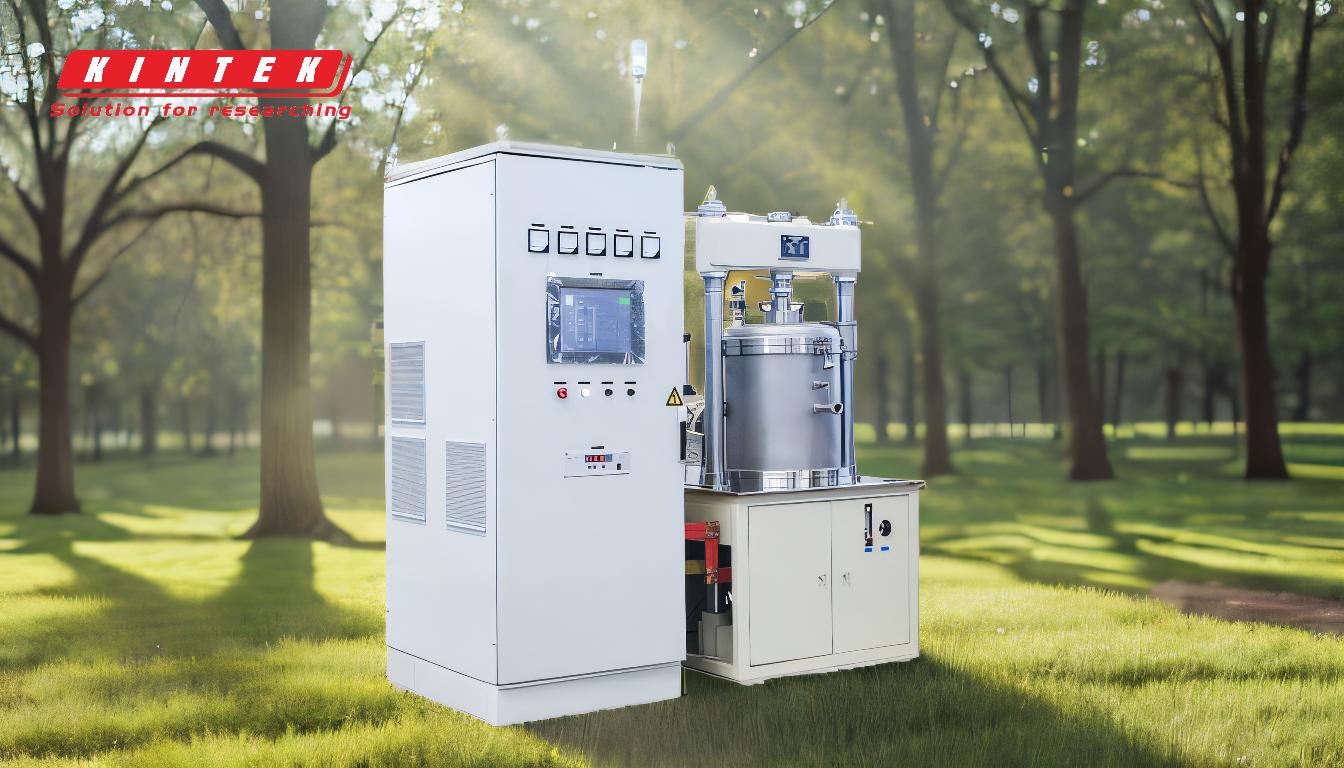
-
Annealing:
- Process: Annealing involves heating steel to a temperature above its critical point (typically between 700°C and 900°C), holding it at that temperature to allow the microstructure to become uniform, and then slowly cooling it in the furnace.
- Purpose: The primary goal of annealing is to soften the steel, improve its ductility, and reduce internal stresses. This makes the steel easier to machine or form.
- Applications: Annealing is commonly used in the manufacturing of components that require extensive machining or cold working, such as gears, shafts, and structural components.
-
Normalizing:
- Process: Normalizing is similar to annealing but involves heating the steel to a higher temperature (typically above 900°C) and then allowing it to cool in air. This faster cooling rate results in a finer grain structure compared to annealing.
- Purpose: Normalizing is used to refine the grain structure of the steel, improve its mechanical properties, and achieve a more uniform microstructure.
- Applications: This process is often applied to steel components that need to have a balance of strength and toughness, such as structural beams and plates.
-
Hardening:
- Process: Hardening involves heating the steel to a temperature above its critical point, holding it at that temperature, and then rapidly cooling it (quenching) in water, oil, or air. This rapid cooling transforms the microstructure into martensite, which is very hard but brittle.
- Purpose: The main objective of hardening is to increase the hardness and strength of the steel. However, this process also makes the steel more brittle.
- Applications: Hardening is used for components that require high wear resistance, such as cutting tools, dies, and bearings.
-
Tempering:
- Process: Tempering is performed after hardening to reduce the brittleness of the steel. It involves reheating the hardened steel to a temperature below its critical point (typically between 150°C and 650°C) and then cooling it at a controlled rate.
- Purpose: Tempering reduces the brittleness introduced during hardening while maintaining a significant portion of the hardness. It also improves the toughness and ductility of the steel.
- Applications: Tempering is essential for components that need to withstand impact or fatigue, such as springs, gears, and structural parts.
Each of these heat treatment processes plays a vital role in modifying the properties of steel to meet specific engineering requirements. By carefully selecting and controlling the temperature, time, and cooling rate, manufacturers can produce steel components with tailored mechanical properties, ensuring optimal performance in their intended applications.
Summary Table:
Heat Treatment | Process | Purpose | Applications |
---|---|---|---|
Annealing | Heat to 700°C–900°C, hold, then slowly cool in furnace. | Softens steel, improves ductility, reduces internal stresses. | Gears, shafts, structural components. |
Normalizing | Heat above 900°C, then cool in air. | Refines grain structure, improves mechanical properties. | Structural beams, plates. |
Hardening | Heat above critical point, then rapidly cool (quench). | Increases hardness and strength, but makes steel brittle. | Cutting tools, dies, bearings. |
Tempering | Reheat hardened steel to 150°C–650°C, then cool at controlled rate. | Reduces brittleness, maintains hardness, improves toughness and ductility. | Springs, gears, structural parts. |
Optimize your steel components with the right heat treatment—contact our experts today for tailored solutions!