Brazing is a versatile joining process that involves melting a filler metal to bond two or more metal components without melting the base materials. There are five primary types of brazing processes, each suited to specific applications and requirements. These include torch brazing, furnace brazing, induction brazing, dip brazing, and resistance brazing. Each method has unique advantages, such as precision, scalability, and suitability for different materials. Understanding these processes helps in selecting the most appropriate technique for achieving strong, durable, and high-quality joints in various industrial and manufacturing contexts.
Key Points Explained:
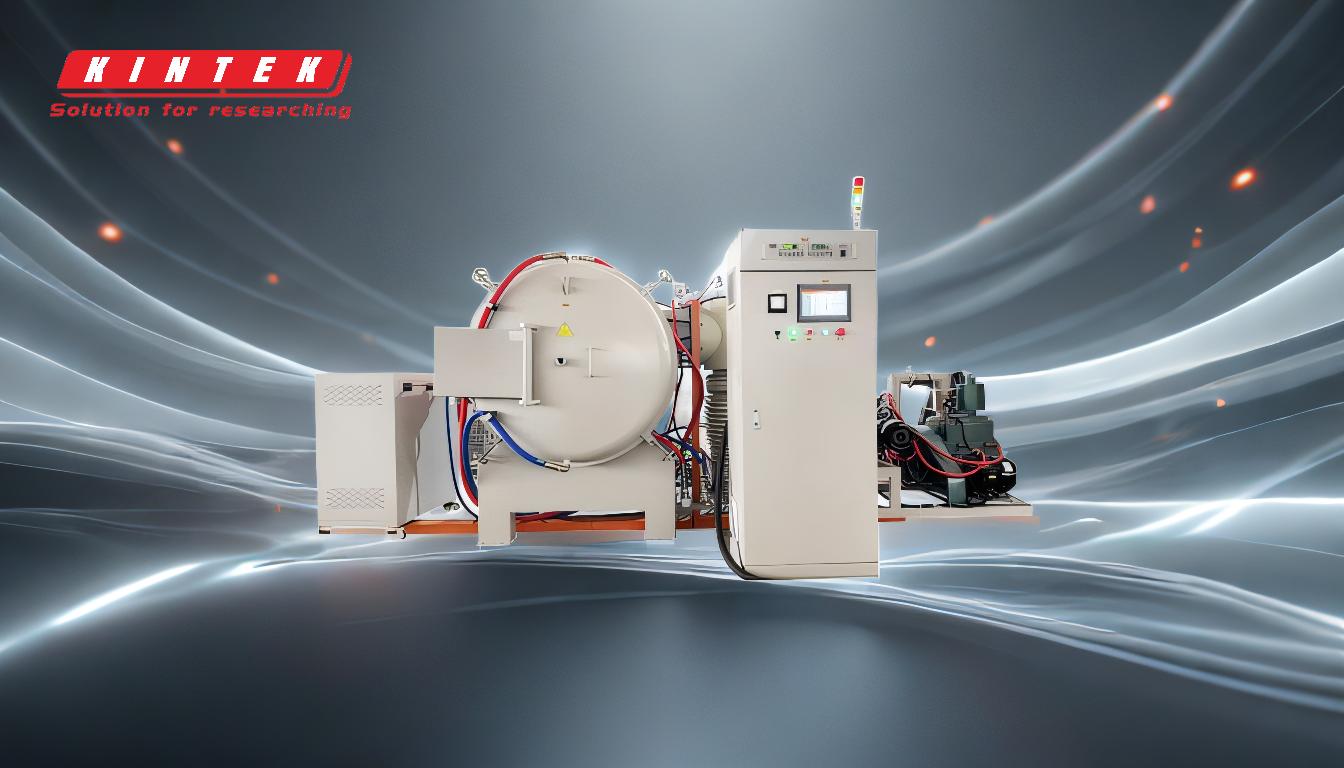
-
Torch Brazing
- Process Overview: Torch brazing uses a gas flame to heat the filler metal and base materials. The heat is applied directly to the joint area, and the filler metal is manually or automatically fed into the joint.
- Applications: This method is ideal for small-scale production, repairs, and assemblies where portability and flexibility are required.
-
Advantages:
- High precision and control over the heating process.
- Suitable for a wide range of materials, including copper, brass, and stainless steel.
-
Limitations:
- Requires skilled operators to ensure proper heat distribution.
- Not ideal for large-scale or automated production.
-
Furnace Brazing
- Process Overview: Furnace brazing involves placing the assembled components into a furnace, where the entire assembly is heated uniformly. The filler metal melts and flows into the joint due to capillary action.
- Applications: Commonly used in mass production of components, such as automotive parts, aerospace components, and electronics.
-
Advantages:
- Consistent and uniform heating ensures high-quality joints.
- Suitable for complex assemblies and large batches.
-
Limitations:
- High initial setup cost for furnaces.
- Limited flexibility for small-scale or custom projects.
-
Induction Brazing
- Process Overview: Induction brazing uses electromagnetic induction to generate heat in the base materials. The filler metal is pre-placed or fed into the joint, and the heat is localized to the joint area.
- Applications: Ideal for precision components, such as electrical contacts, sensors, and medical devices.
-
Advantages:
- Rapid heating and cooling cycles improve efficiency.
- Minimal distortion of the base materials due to localized heating.
-
Limitations:
- Requires specialized equipment and setup.
- Limited to materials that can be heated by induction.
-
Dip Brazing
- Process Overview: Dip brazing involves immersing the assembled components into a molten salt bath or a bath of molten filler metal. The heat from the bath melts the filler metal, which flows into the joint.
- Applications: Suitable for joining aluminum and other non-ferrous metals, often used in heat exchangers and automotive radiators.
-
Advantages:
- Uniform heating ensures strong and reliable joints.
- Efficient for large-scale production.
-
Limitations:
- Requires careful handling of molten materials.
- Limited to specific materials and joint designs.
-
Resistance Brazing
- Process Overview: Resistance brazing uses electrical resistance to generate heat at the joint interface. The filler metal is pre-placed, and the heat is localized to the joint area.
- Applications: Commonly used for joining small components, such as electrical contacts and connectors.
-
Advantages:
- Fast and efficient process with minimal heat-affected zones.
- Suitable for high-volume production.
-
Limitations:
- Requires precise control of electrical parameters.
- Limited to materials with good electrical conductivity.
By understanding these five brazing processes, manufacturers and engineers can select the most appropriate method based on the specific requirements of their projects, ensuring optimal performance and cost-effectiveness.
Summary Table:
Brazing Process | Applications | Advantages | Limitations |
---|---|---|---|
Torch Brazing | Small-scale production, repairs | High precision, wide material compatibility | Requires skilled operators, not for large-scale production |
Furnace Brazing | Mass production (automotive, aerospace) | Uniform heating, ideal for complex assemblies | High setup cost, limited flexibility |
Induction Brazing | Precision components (electrical, medical) | Rapid heating, minimal distortion | Specialized equipment required |
Dip Brazing | Aluminum and non-ferrous metals | Uniform heating, efficient for large-scale | Handling molten materials, limited material compatibility |
Resistance Brazing | Small components (electrical contacts) | Fast, minimal heat-affected zones | Requires precise control, limited to conductive materials |
Need help choosing the right brazing process for your project? Contact our experts today for tailored solutions!