Heat treatment is a critical process in metallurgy and manufacturing, offering significant advantages such as altering mechanical properties, enhancing material performance, and supporting sustainability. However, it also comes with challenges, including energy consumption, potential material distortion, and the need for precise control. By understanding the advantages and disadvantages of heat treatment, manufacturers can optimize their processes to achieve desired material characteristics while minimizing drawbacks.
Key Points Explained:
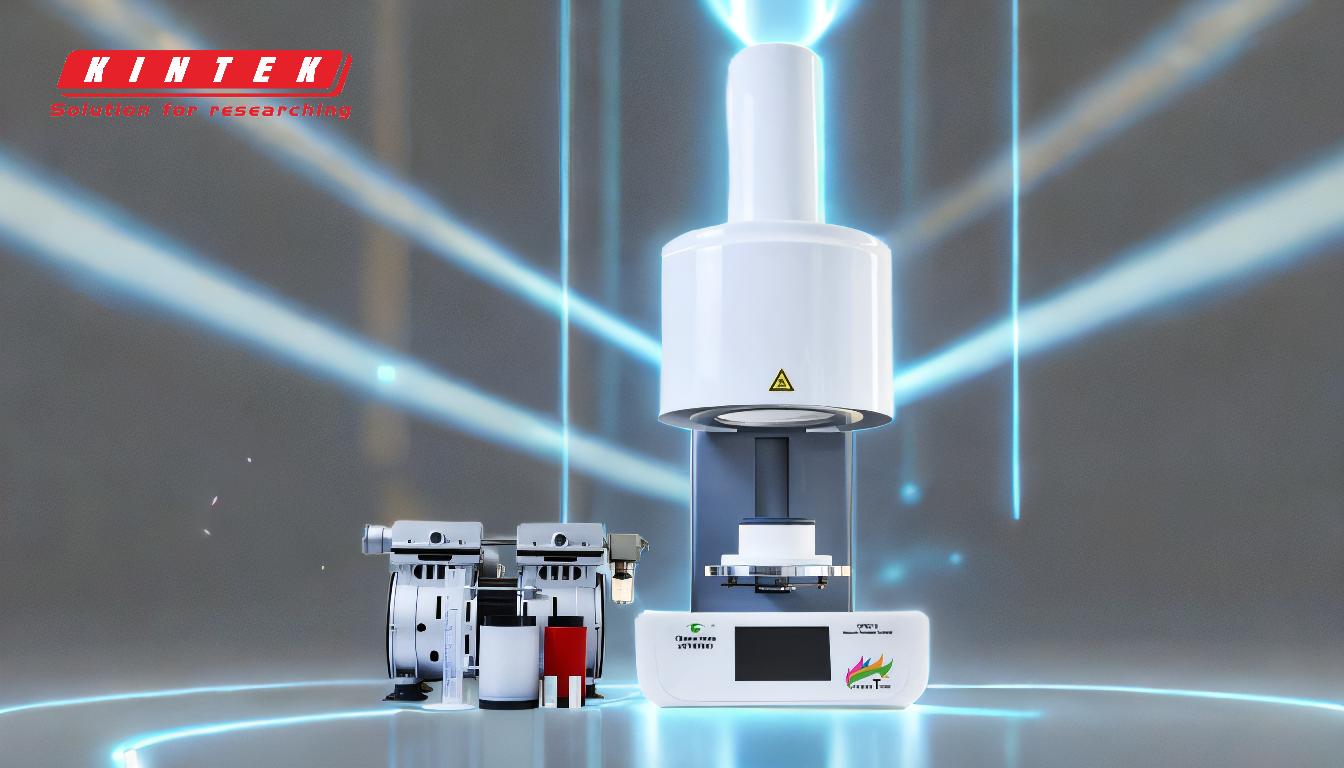
-
Advantages of Heat Treatment:
- Enhanced Mechanical Properties: Heat treatment can significantly alter the mechanical properties of metallic alloys, such as hardness, strength, toughness, ductility, and elasticity. This is achieved by controlling the rate of diffusion and cooling within the metal's microstructure. For example, processes like quenching and tempering can increase the strength and durability of steel, making it suitable for demanding applications.
- Stress Relief and Improved Machinability: Heat treatment can relieve internal stresses in materials, making them easier to machine or weld. This is particularly beneficial for parts that undergo complex manufacturing processes, as it reduces the risk of cracking or deformation during fabrication.
- Introduction of Wear-Resistant Characteristics: Certain heat treatment processes, such as case hardening, can introduce wear-resistant properties to the surface of a material. This is essential for components subjected to high friction or abrasion, such as gears and bearings.
- Sustainability and Energy Efficiency: Vacuum heat treatment, in particular, is more energy-efficient compared to traditional methods. It eliminates the need for combustion and reduces post-treatment cleaning, aligning with eco-conscious practices and supporting sustainability in manufacturing.
-
Disadvantages of Heat Treatment:
- Energy Consumption: While vacuum heat treatment is energy-efficient, other heat treatment methods can be energy-intensive. High temperatures and prolonged heating cycles may lead to increased operational costs and environmental impact.
- Material Distortion: Heat treatment can cause distortion or warping in materials, especially if the process is not carefully controlled. This can result in dimensional inaccuracies, requiring additional machining or corrective measures.
- Precision and Control Requirements: Achieving the desired material properties through heat treatment requires precise control over temperature, cooling rates, and other parameters. Any deviation can lead to inconsistent results, affecting the quality and performance of the treated components.
- Cost and Complexity: Advanced heat treatment processes, such as vacuum or controlled atmosphere treatments, can be costly and require specialized equipment. This may limit their accessibility for smaller manufacturers or those with budget constraints.
-
Applications and Considerations:
- Heat treatment is widely used in industries such as automotive, aerospace, and tool manufacturing, where material performance is critical. For example, heat-treated steel is essential for producing high-strength components like crankshafts, gears, and cutting tools.
- Manufacturers must carefully consider the specific requirements of their application when selecting a heat treatment method. Factors such as material type, desired properties, and production volume play a crucial role in determining the most suitable approach.
By weighing the advantages and disadvantages of heat treatment, manufacturers can make informed decisions to optimize their processes and achieve the desired material characteristics while minimizing potential drawbacks.
Summary Table:
Aspect | Advantages | Disadvantages |
---|---|---|
Mechanical Properties | Improves hardness, strength, toughness, ductility, and elasticity. | Requires precise control to avoid inconsistent results. |
Stress Relief | Reduces internal stresses, improving machinability and weldability. | Can cause material distortion if not carefully controlled. |
Wear Resistance | Introduces wear-resistant properties (e.g., case hardening). | Advanced methods like vacuum treatment can be costly. |
Sustainability | Vacuum heat treatment is energy-efficient and eco-friendly. | Traditional methods are energy-intensive and increase operational costs. |
Want to optimize your heat treatment process? Contact our experts today for tailored solutions!