Hot pressing, cold compacting, and sintering are all widely used methods in powder metallurgy, each with its own set of advantages and disadvantages. Hot pressing combines the processes of pressing and sintering under high temperature and pressure, which can lead to denser and stronger materials with finer grain structures. However, it is often more expensive and less productive compared to cold compacting and sintering. Cold compacting and sintering, on the other hand, are simpler and more cost-effective but may result in materials with higher porosity and less mechanical strength. Understanding the trade-offs between these methods is crucial for selecting the appropriate process based on the desired material properties and production requirements.
Key Points Explained:
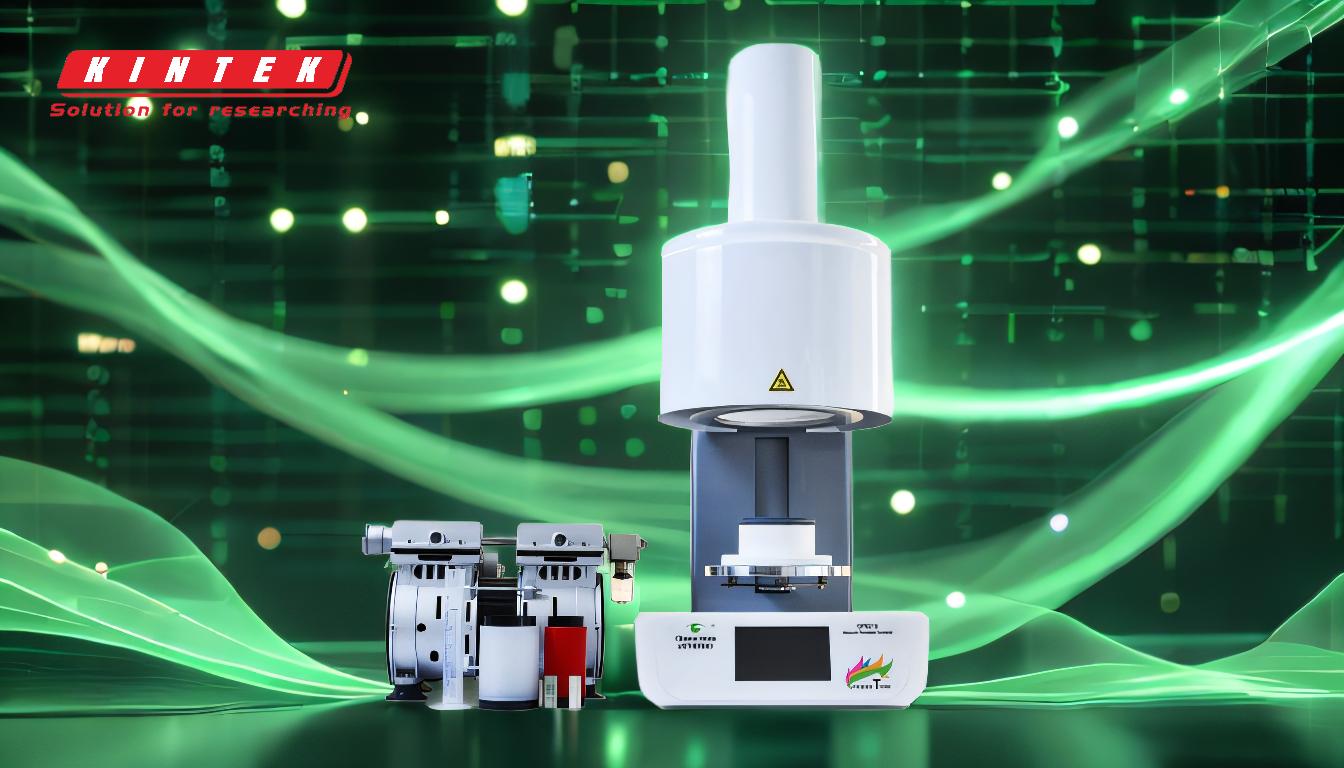
-
Advantages of Hot Pressing:
- Lower Deformation Resistance: Hot pressing takes advantage of the thermoplastic state of the powder, requiring only about 1/10 of the pressure needed for cold pressing. This reduces the mechanical stress on the equipment and allows for easier shaping of complex geometries.
- Lower Sintering Temperature and Time: The simultaneous application of heat and pressure during hot pressing aids in mass transfer, significantly reducing the required sintering temperature and time. This also helps in inhibiting grain growth, leading to finer grains and improved mechanical properties.
- High Density and Fine Grain Structure: Hot pressing can achieve sintered bodies with near-theoretical density, fine grain structures, and excellent mechanical and electrical properties. This is particularly beneficial for applications requiring high strength and durability.
- Complex Shapes and Accurate Sizes: The process allows for the production of complex-shaped and accurately sized products, which can be difficult to achieve with cold compacting and sintering.
-
Disadvantages of Hot Pressing:
- Low Productivity: Hot pressing is generally slower than cold compacting and sintering due to the need for simultaneous heating and pressing. This can lead to lower throughput in a production setting.
- High Cost: The equipment required for hot pressing is more complex and expensive, and the process consumes more energy, making it a less cost-effective option for large-scale production.
-
Advantages of Cold Compacting and Sintering:
- Simplicity and Low Cost: Cold compacting and sintering are simpler processes that require less sophisticated equipment. This makes them more cost-effective, especially for large-scale production.
- Shorter Processing Time: Since cold compacting and sintering are separate processes, they can be optimized independently, potentially leading to shorter overall processing times compared to hot pressing.
-
Disadvantages of Cold Compacting and Sintering:
- Higher Porosity: Materials produced through cold compacting and sintering often have higher porosity, which can negatively impact their mechanical strength and durability.
- Coarser Grain Structure: The higher sintering temperatures required in cold compacting and sintering can lead to coarser grain structures, which may reduce the mechanical properties of the final product.
-
Comparison with Other Methods:
- Hot Isostatic Pressing (HIP): Similar to hot pressing but performed at much higher pressures, HIP can achieve even higher densities and better mechanical properties. However, it is even more expensive and less productive than hot pressing.
- Field-Assisted Sintering (FAST): This method offers advantages such as shorter sintering times, lower furnace temperatures, and the ability to inhibit grain growth. It is also simpler and more cost-effective in terms of equipment compared to hot pressing.
In conclusion, the choice between hot pressing, cold compacting, and sintering depends on the specific requirements of the application, including the desired material properties, production scale, and cost considerations. Hot pressing is ideal for producing high-density, fine-grained materials with excellent mechanical properties, but it comes at a higher cost and lower productivity. Cold compacting and sintering, while more cost-effective and simpler, may not achieve the same level of material performance.
Summary Table:
Aspect | Hot Pressing | Cold Compacting & Sintering |
---|---|---|
Advantages | - Lower deformation resistance - High density & fine grain structure - Complex shapes & accurate sizes |
- Simplicity & low cost - Shorter processing time |
Disadvantages | - Low productivity - High cost |
- Higher porosity - Coarser grain structure |
Best For | High-density, fine-grained materials with excellent mechanical properties | Cost-effective, large-scale production with simpler requirements |
Comparison with HIP/FAST | More expensive & less productive than HIP/FAST | Simpler & more cost-effective than HIP/FAST |
Need help choosing the right powder metallurgy method? Contact our experts today for tailored solutions!