Selective Heat Sintering (SHS) is a 3D printing technology that uses a thermal printhead to selectively fuse powdered material layer by layer. It shares similarities with Selective Laser Sintering (SLS) but differs in the heat source. SHS offers advantages such as cost-effectiveness, faster production, and the ability to create complex geometries. However, it also has limitations, including material restrictions, lower resolution compared to other methods, and potential concerns about material strength and density. Below, we explore the key advantages and disadvantages of SHS in detail.
Key Points Explained:
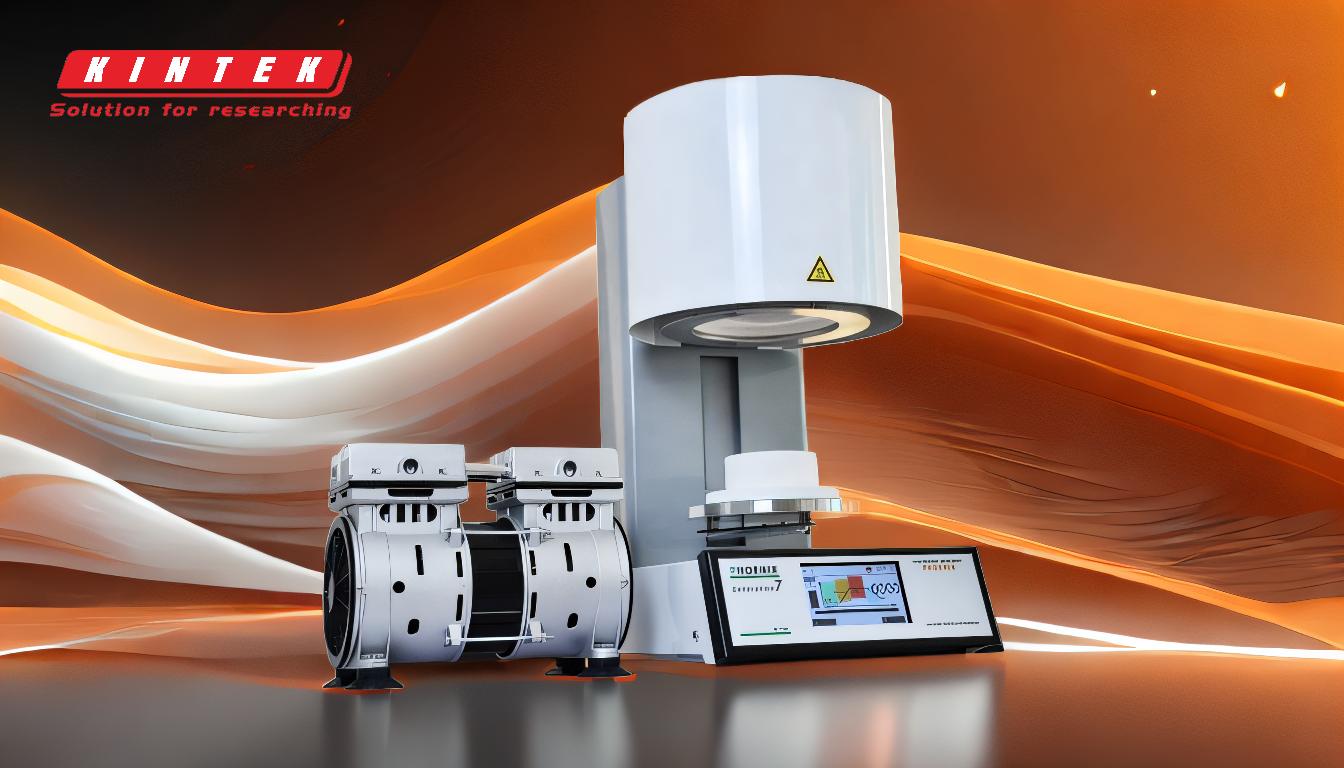
-
Advantages of Selective Heat Sintering (SHS):
-
Cost-Effectiveness:
- SHS is generally more affordable than SLS because it uses a thermal printhead instead of an expensive laser. This reduces both the initial investment and operational costs.
- The materials used in SHS are often less expensive than those required for SLS, making it a more budget-friendly option for small to medium-scale production.
-
Faster Production:
- The thermal printhead in SHS can cover larger areas simultaneously compared to a laser, enabling faster layer-by-layer sintering. This makes SHS suitable for rapid prototyping and small-batch production.
-
Complex Geometries:
- Like SLS, SHS can produce intricate and functional shapes that are difficult or impossible to achieve with traditional manufacturing methods. This is particularly beneficial for industries requiring customized or complex parts.
-
Ease of Use:
- SHS systems are often simpler to operate than SLS machines, reducing the need for highly skilled operators. This lowers labor costs and makes the technology more accessible to smaller businesses.
-
Cost-Effectiveness:
-
Disadvantages of Selective Heat Sintering (SHS):
-
Material Limitations:
- SHS is typically limited to specific thermoplastic materials, such as nylon-based powders. This restricts its application compared to SLS, which can work with a wider range of materials, including metals and ceramics.
- Not all material suppliers endorse SHS, which may indicate concerns about material compatibility, strength, or density.
-
Lower Resolution:
- SHS generally produces parts with lower resolution and surface finish compared to SLS. This is due to the larger spot size of the thermal printhead compared to a laser beam.
- Post-processing, such as sanding or polishing, may be required to achieve a smoother finish, adding time and cost to the production process.
-
Strength and Density Concerns:
- Some studies suggest that parts produced by SHS may have slightly lower density and strength compared to those made with SLS or high-speed sintering. This could limit their use in high-stress applications.
-
Limited Industry Adoption:
- SHS is not as widely adopted as SLS or other 3D printing technologies, which may result in fewer resources, support, and material options for users.
-
Material Limitations:
-
Comparison with Other Sintering Methods:
-
Selective Laser Sintering (SLS):
- SLS offers higher resolution and the ability to work with a broader range of materials, including metals and ceramics. However, it is significantly more expensive and requires skilled operators.
-
High-Speed Sintering:
- High-speed sintering can achieve slightly higher density and strength compared to SHS. However, it is not universally endorsed by material suppliers, suggesting potential limitations or concerns.
-
Powder Metallurgy:
- Powder metallurgy is more cost-effective for large-scale production of medium-complexity parts but may result in non-uniform components due to friction between the powder and tooling.
-
Selective Laser Sintering (SLS):
-
Applications and Suitability:
- SHS is well-suited for rapid prototyping, small-batch production, and applications where cost and speed are prioritized over high resolution or material versatility.
- It may not be ideal for industries requiring high-strength, high-density parts or those needing a wide variety of material options.
In summary, Selective Heat Sintering offers a cost-effective and efficient solution for producing complex geometries, particularly in prototyping and small-scale manufacturing. However, its material limitations, lower resolution, and potential concerns about part strength and density may restrict its use in certain applications. Understanding these trade-offs is essential for selecting the right sintering method for specific needs.
Summary Table:
Aspect | Advantages | Disadvantages |
---|---|---|
Cost | More affordable than SLS; lower initial and operational costs. | Limited to specific materials; higher post-processing costs. |
Speed | Faster production due to larger thermal printhead coverage. | Lower resolution compared to SLS; requires post-processing for smoother finishes. |
Complexity | Capable of producing intricate and functional shapes. | Parts may have lower density and strength, limiting high-stress applications. |
Ease of Use | Simpler operation; reduced need for skilled labor. | Limited industry adoption; fewer material and support options. |
Looking for the right 3D printing solution for your needs? Contact us today to learn more about Selective Heat Sintering!