Physical Vapor Deposition (PVD) is a widely used coating technology with numerous advantages, such as environmental friendliness, high durability, and precise control over coating properties. However, it also has limitations, including line-of-sight constraints, high operational temperatures, and the need for specialized equipment. PVD is suitable for applications requiring thin, durable, and corrosion-resistant coatings, such as in semiconductors, food packaging, and metalworking tools. Despite its limitations, PVD remains a preferred choice for many industries due to its ability to produce high-quality, long-lasting coatings.
Key Points Explained:
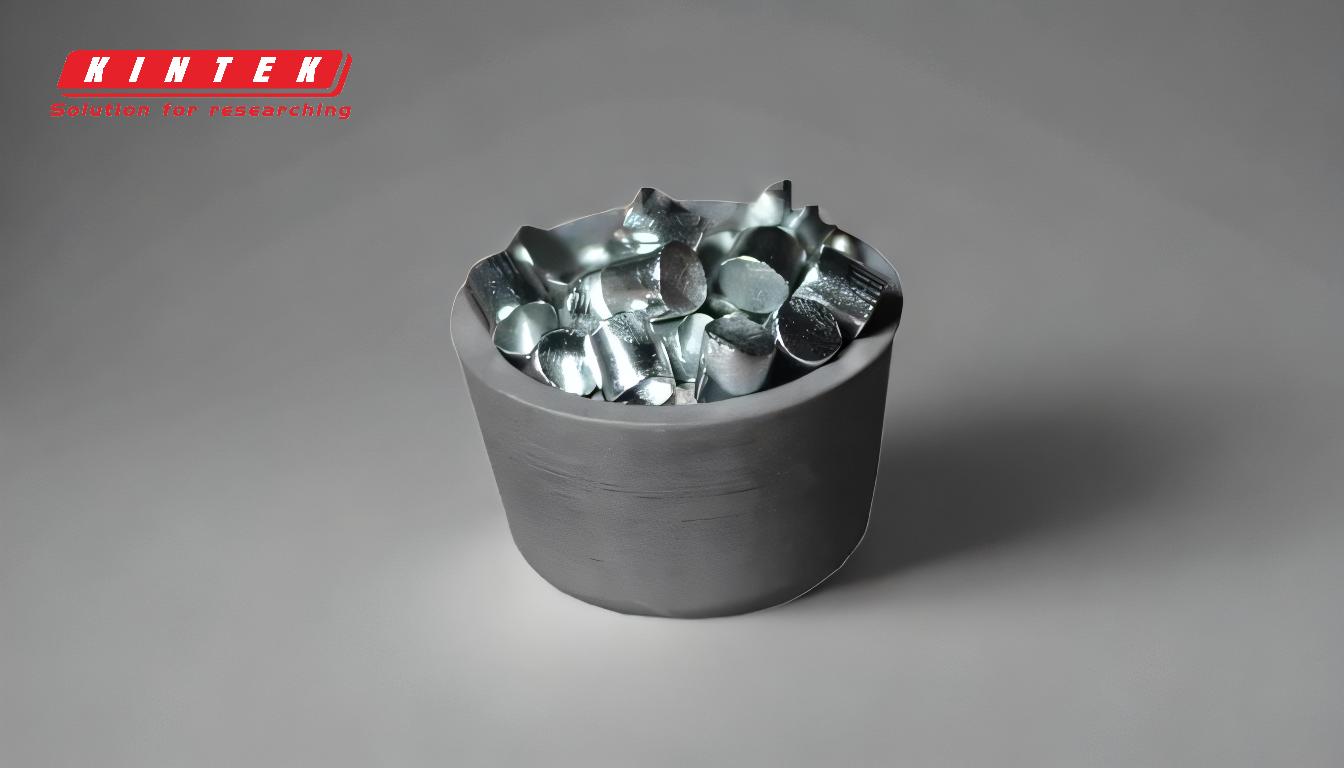
-
Advantages of PVD:
- Environmental Friendliness: PVD does not require chemical reagents or post-treatment cleaning, making it an eco-friendly process. It produces minimal waste and avoids harmful byproducts.
- Versatility: PVD can be applied to a wide range of inorganic materials and some organic materials, making it suitable for diverse applications.
- Durability and Resistance: PVD coatings are known for their excellent adhesion, corrosion resistance, and wear resistance. They enhance the lifespan of products and reduce the need for frequent maintenance.
- Precision and Control: PVD allows for precise control over the composition, thickness, and uniformity of coatings, ensuring high-quality results.
- Aesthetic and Functional Benefits: PVD coatings can be applied in various colors and finishes, offering both aesthetic and functional advantages, such as improved surface quality and abrasion resistance.
-
Limitations of PVD:
- Line-of-Sight Constraints: Most PVD techniques are line-of-sight processes, meaning they coat only the surfaces directly exposed to the vapor source. This can limit the ability to coat complex geometries uniformly.
- High Operational Temperatures: PVD processes often require high temperatures (320 to 900 degrees Fahrenheit) and vacuum conditions, which can be challenging to maintain and may limit the types of substrates that can be coated.
- Specialized Equipment and Expertise: PVD requires specialized equipment, including vacuum chambers and cooling systems, as well as skilled personnel to operate and maintain the systems.
- Cost and Complexity: The initial setup and operational costs of PVD can be high, and the process may require additional steps, such as substrate preparation, to achieve optimal results.
-
Applications of PVD:
- Semiconductor Industry: PVD is used to create thin films for semiconductor devices, such as thin-film solar panels, where precise control over coating properties is essential.
- Food Packaging: Aluminized PET film, produced using PVD, is used in food packaging and balloons due to its barrier properties and durability.
- Metalworking Tools: Titanium nitride coatings applied via PVD enhance the hardness and wear resistance of cutting tools, extending their lifespan and improving performance.
-
Comparison with Other Coating Techniques:
- PVD vs. Electroplating: PVD coatings are generally more durable, corrosion-resistant, and environmentally friendly compared to electroplating. PVD also offers better control over coating properties and does not require harmful chemicals.
- PVD vs. Painting: PVD provides a more durable and long-lasting finish than traditional painting, with better resistance to wear, corrosion, and environmental factors.
In summary, PVD offers significant advantages in terms of environmental impact, durability, and precision, making it a preferred choice for many industrial applications. However, its limitations, such as line-of-sight constraints and high operational costs, must be carefully considered when selecting a coating technology.
Summary Table:
Aspect | Details |
---|---|
Advantages | - Eco-friendly, durable, precise control, versatile, aesthetic & functional |
Limitations | - Line-of-sight constraints, high temperatures, specialized equipment, cost |
Applications | - Semiconductors, food packaging, metalworking tools |
Comparison | - More durable than electroplating, longer-lasting than painting |
Discover how PVD can enhance your industrial processes—contact our experts today!