Forging is a highly versatile manufacturing process that offers numerous advantages, such as superior part strength, custom shapes, and unique performance specifications. It is particularly beneficial for applications requiring high strength and durability. The process compresses the grain structure of the metal, enhancing its mechanical properties and reducing defects like porosity and alloy segregation. However, forging also has limitations, including higher initial tooling costs and limitations in producing highly complex geometries. Below, we explore the key advantages and limitations of the forging process in detail.
Key Points Explained:
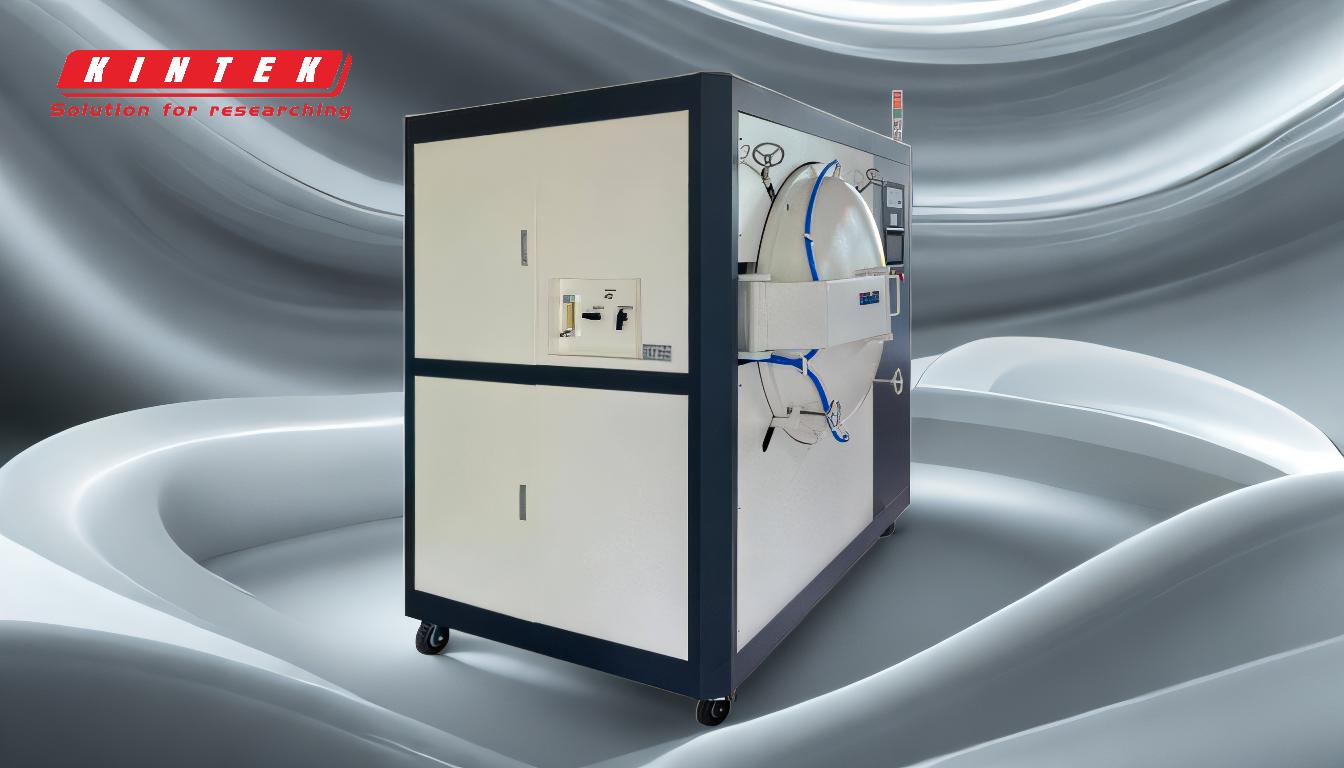
-
Advantages of Forging:
-
Superior Strength and Durability:
- Forging compresses the metal's grain structure, aligning it with the shape of the part. This grain flow enhances the material's strength, toughness, and resistance to fatigue, making forged parts ideal for high-stress applications.
-
Improved Metallurgical Properties:
- The process minimizes metallurgical defects such as porosity, voids, and alloy segregation. This results in a more uniform and defect-free material, which improves the part's response to heat treatment and reduces the risk of failure.
-
Custom Shapes and Sizes:
- Forging allows for the creation of custom shapes and sizes, making it suitable for specialized applications. The process can produce parts with unique performance specifications that are difficult to achieve with other manufacturing methods.
-
Reduced Machining Time:
- Forged parts often require less machining compared to cast or machined parts. The near-net shape produced by forging reduces material waste and machining time, leading to cost savings.
-
Cost-Effective for High-Volume Production:
- While the initial tooling costs for forging can be high, the process becomes cost-effective for high-volume production runs due to its efficiency and reduced material waste.
-
Superior Strength and Durability:
-
Limitations of Forging:
-
High Initial Tooling Costs:
- Forging requires specialized dies and tooling, which can be expensive to design and manufacture. This makes the process less economical for low-volume or prototype production.
-
Limited Geometric Complexity:
- Forging is less suitable for producing highly complex geometries or intricate details compared to processes like casting or additive manufacturing. The process is better suited for parts with relatively simple shapes.
-
Material Limitations:
- Not all materials are suitable for forging. Some alloys and materials may not respond well to the high temperatures and pressures involved in the process, limiting the range of applications.
-
Size Constraints:
- The size of forged parts is limited by the capacity of the forging equipment. Extremely large or heavy parts may require specialized equipment, increasing costs and complexity.
-
Surface Finish and Tolerances:
- Forged parts often require additional machining to achieve precise tolerances and surface finishes. While forging reduces machining time, it does not eliminate the need for secondary operations.
-
High Initial Tooling Costs:
In summary, forging is a highly effective manufacturing process for producing strong, durable, and custom-shaped parts. Its advantages in strength, metallurgical properties, and cost-effectiveness for high-volume production make it a preferred choice for many industries. However, its limitations in geometric complexity, initial tooling costs, and material suitability must be carefully considered when selecting the appropriate manufacturing method for a given application.
Summary Table:
Aspect | Advantages | Limitations |
---|---|---|
Strength & Durability | Enhanced strength, toughness, and fatigue resistance due to compressed grain structure. | High initial tooling costs, making it less economical for low-volume production. |
Metallurgical Properties | Minimized defects like porosity and alloy segregation, improving material uniformity. | Limited geometric complexity, unsuitable for highly intricate designs. |
Custom Shapes & Sizes | Ability to produce custom shapes and sizes for specialized applications. | Material limitations; not all alloys are suitable for forging. |
Reduced Machining Time | Near-net shape reduces material waste and machining time, saving costs. | Size constraints due to equipment capacity, requiring specialized tools. |
Cost-Effectiveness | Economical for high-volume production due to efficiency and reduced waste. | Additional machining needed for precise tolerances and surface finishes. |
Want to learn more about forging and how it can benefit your project? Contact our experts today for personalized advice!