Continuous furnaces, particularly continuous vacuum furnaces, offer several advantages that make them highly suitable for specific industrial applications. These advantages include enhanced production efficiency, reduced operating costs, and the ability to handle high-volume manufacturing. However, they also come with certain complexities and maintenance requirements. Below, we explore the key advantages of continuous furnaces in detail.
Key Points Explained:
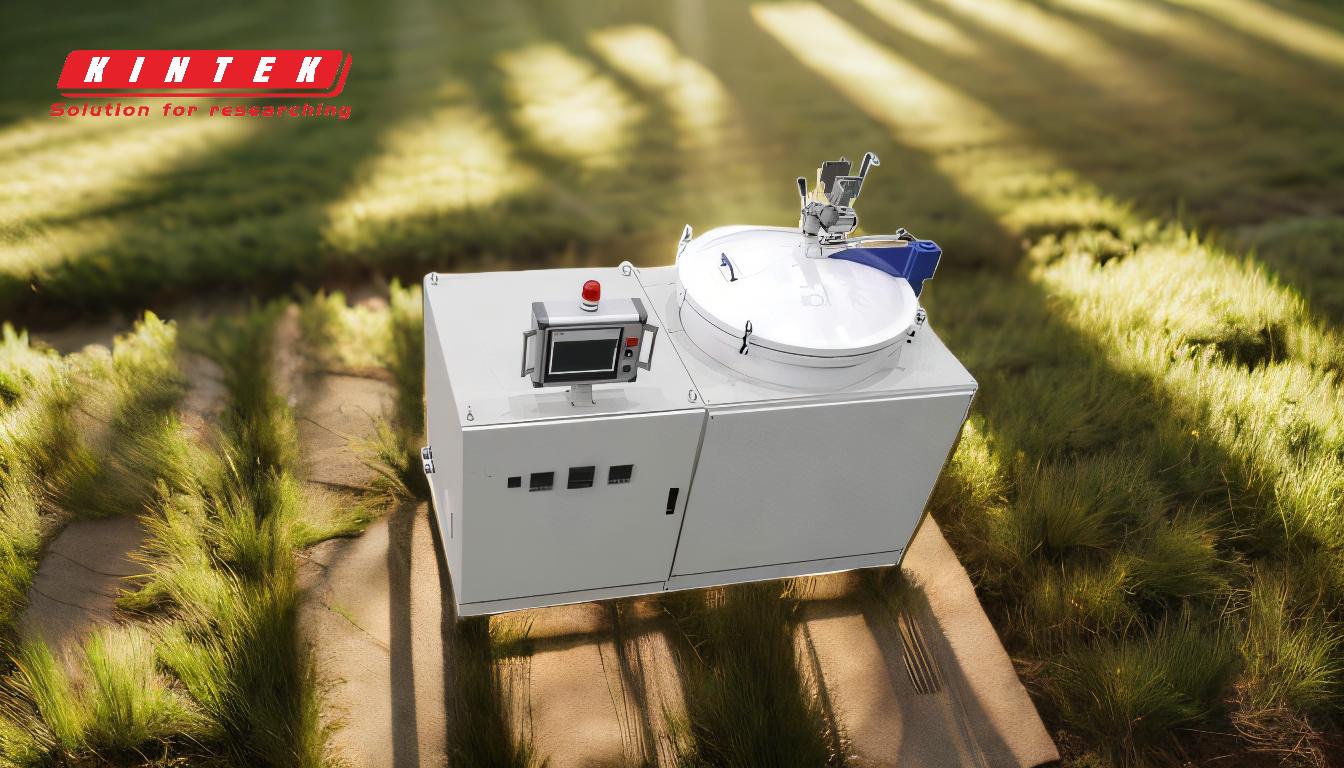
-
High Production Efficiency:
- Short Production Cycles: Continuous furnaces are designed for rapid processing, which significantly reduces the time required for each production cycle. This is particularly beneficial in high-volume manufacturing environments where time is a critical factor.
- Continuous Operation: Unlike batch furnaces, continuous furnaces operate without interruption, allowing for a steady flow of materials through the furnace. This continuous operation minimizes downtime and maximizes throughput.
-
Cost-Effectiveness:
- Low Operating Costs: Continuous furnaces are generally more energy-efficient than batch furnaces because they maintain a constant temperature, reducing the energy required to heat up and cool down the furnace between batches.
- Simple Brazing Fixtures: The use of simple brazing fixtures in continuous vacuum brazing furnaces eliminates the need for expensive specialized fixtures, further reducing operational costs.
-
Environmental Benefits:
- No Pollution: Continuous vacuum furnaces operate in a controlled environment, which prevents contamination and pollution. This is particularly important in industries where cleanliness and environmental compliance are critical.
-
Versatility in Processing:
- Debinding and Sintering in One Step: Continuous furnaces can perform multiple processes, such as debinding and sintering, in a single step. This capability not only saves time but also ensures a more consistent and uniform treatment of materials.
- High-Temperature Capabilities: These furnaces can reach temperatures close to the melting point of the base metal, making them ideal for processes that require extreme heat.
-
Ideal for High-Volume Manufacturing:
- Consistent Temperature: Continuous furnaces operate at a constant temperature, which is ideal for processing large quantities of materials uniformly. This consistency is crucial for maintaining product quality in high-volume production settings.
-
Complexity and Maintenance:
- Higher Complexity and Cost: While continuous furnaces offer numerous advantages, they are generally more complex and expensive to install and maintain compared to batch furnaces. The initial investment and ongoing maintenance costs can be higher.
- Frequent Maintenance: Due to their continuous operation, these furnaces require more frequent maintenance to ensure they remain in optimal working condition. Regular maintenance is essential to prevent downtime and maintain production efficiency.
In summary, continuous furnaces provide significant advantages in terms of production efficiency, cost-effectiveness, and environmental benefits. They are particularly well-suited for high-volume manufacturing and processes that require consistent high temperatures. However, potential users must also consider the higher complexity, cost, and maintenance requirements associated with these furnaces.
Summary Table:
Advantage | Key Benefits |
---|---|
High Production Efficiency | Short production cycles, continuous operation, minimized downtime |
Cost-Effectiveness | Low operating costs, simple brazing fixtures, reduced energy consumption |
Environmental Benefits | No pollution, controlled environment, compliance with cleanliness standards |
Versatility in Processing | Debinding and sintering in one step, high-temperature capabilities |
High-Volume Manufacturing | Consistent temperature, uniform processing, ideal for large-scale production |
Complexity and Maintenance | Higher initial cost, frequent maintenance required for optimal performance |
Ready to enhance your production process? Contact us today to learn more about continuous furnaces!