Ball milling is a highly advantageous technique in nanotechnology due to its ability to produce ultra-fine powders with particle sizes as small as 10 microns or less. It is particularly effective for milling toxic, abrasive, and high-hardness materials, making it versatile across various applications. The process is efficient, with high grinding precision and the ability to achieve sub-micron level fineness. Ball mills are also easy to operate, maintain, and clean, with low energy consumption and minimal space requirements. Additionally, they support both wet and dry grinding processes, maintain sterility, and are cost-effective, making them ideal for preparing nano-sized samples with uniform size and high purity.
Key Points Explained:
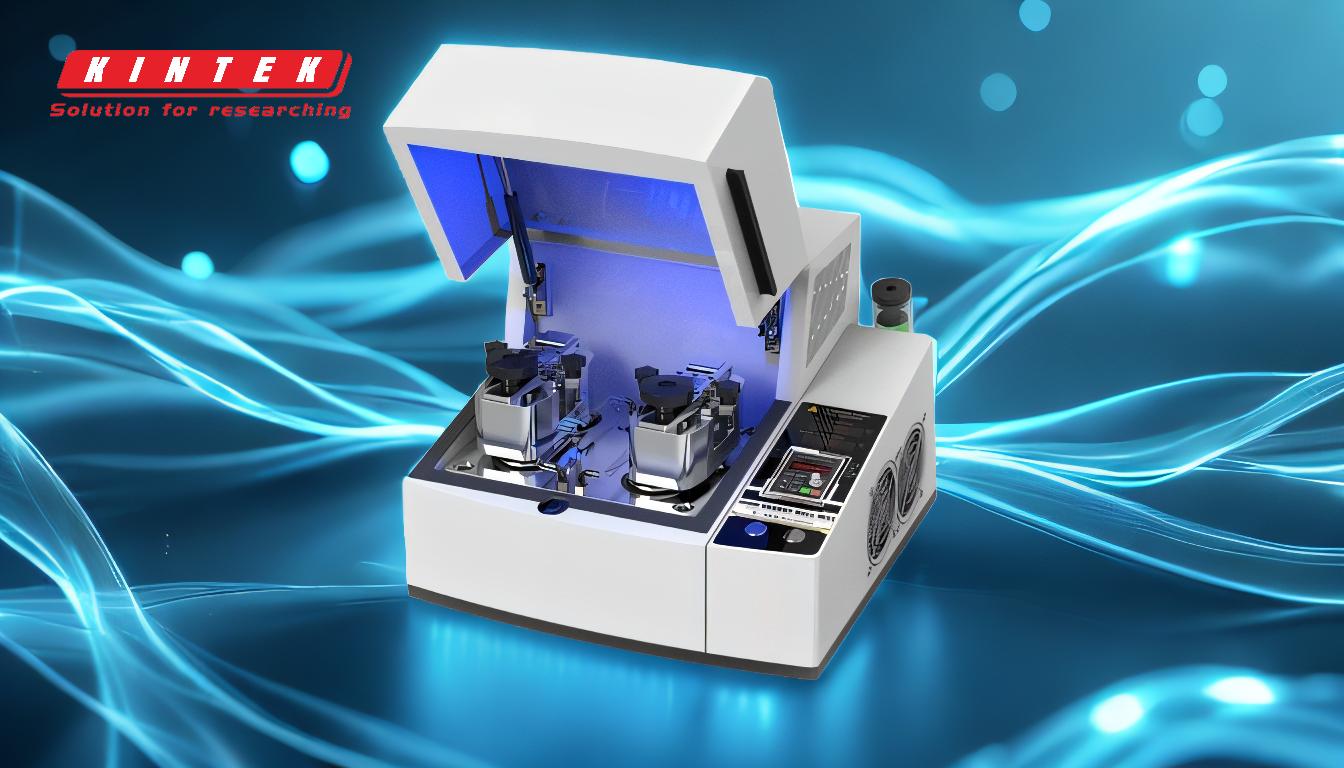
-
Production of Ultra-Fine Powder:
- Ball milling can produce powders with particle sizes ≤10 microns, which is critical in nanotechnology for creating materials with specific properties.
- Sub-micron level fineness is achievable, enabling the preparation of nano-sized samples with uniform size and high purity.
-
Versatility in Material Processing:
- Suitable for milling toxic, abrasive, and high-hardness materials, making it applicable across a wide range of industries.
- Can process various materials, including magnetic, inorganic non-metallic, organic chemical, and biomedical materials.
-
High Grinding Efficiency and Precision:
- Offers rapid grinding, especially for materials with high hardness and viscosity.
- Ensures high precision in the grinding process, which is essential for nanotechnology applications.
-
Ease of Operation and Maintenance:
- Simple structure and operation, requiring only basic maintenance.
- High automation levels improve efficiency and safety in experiments.
-
Environmental and Safety Benefits:
- Enclosed system prevents contamination and maintains sterility, which is crucial for handling toxic materials.
- Low energy consumption and minimal space requirements make it an environmentally friendly option.
-
Cost-Effectiveness:
- Inexpensive to perform and maintain, with low operational costs.
- Produces crystal defects, which can be beneficial for certain applications, such as enhancing catalytic properties.
-
Flexibility in Grinding Processes:
- Supports both wet and dry grinding, providing flexibility based on material requirements.
- Continuous operation capability ensures consistent results over extended periods.
-
Application in Nanotechnology:
- Enables the preparation of nano samples with uniform size and high purity, which is essential for advanced material research and development.
- High grinding efficiency and precision make it a preferred method for producing nanomaterials with specific characteristics.
By leveraging these advantages, ball milling has become a cornerstone technique in nanotechnology, offering a reliable and efficient method for producing high-quality nanomaterials.
Summary Table:
Advantage | Description |
---|---|
Ultra-Fine Powder Production | Produces powders ≤10 microns, enabling nano-sized samples with high purity. |
Versatility in Material Processing | Handles toxic, abrasive, and high-hardness materials across industries. |
High Grinding Efficiency | Rapid grinding with sub-micron precision, ideal for nanotechnology. |
Ease of Operation | Simple structure, low maintenance, and high automation for safety. |
Environmental Benefits | Enclosed system, low energy use, and minimal space requirements. |
Cost-Effectiveness | Low operational costs and ability to produce crystal defects for catalysis. |
Flexibility in Grinding | Supports wet and dry grinding, with continuous operation for consistent results. |
Nanotechnology Applications | Prepares uniform, high-purity nano samples for advanced material research. |
Interested in leveraging ball milling for your nanotechnology needs? Contact us today to learn more!