Ceramic sintering is a critical process in materials science that transforms powdered ceramics into dense, strong, and functional components. This process involves heating ceramic powders below their melting point, allowing particles to bond and densify, which enhances their mechanical, thermal, and electrical properties. The advantages of ceramic sintering include improved strength, reduced porosity, enhanced thermal and electrical conductivity, and the ability to work with high-melting-point materials. Additionally, sintering offers precise control over material properties, making it a versatile and efficient manufacturing method. Below, we explore the key advantages of ceramic sintering in detail.
Key Points Explained:
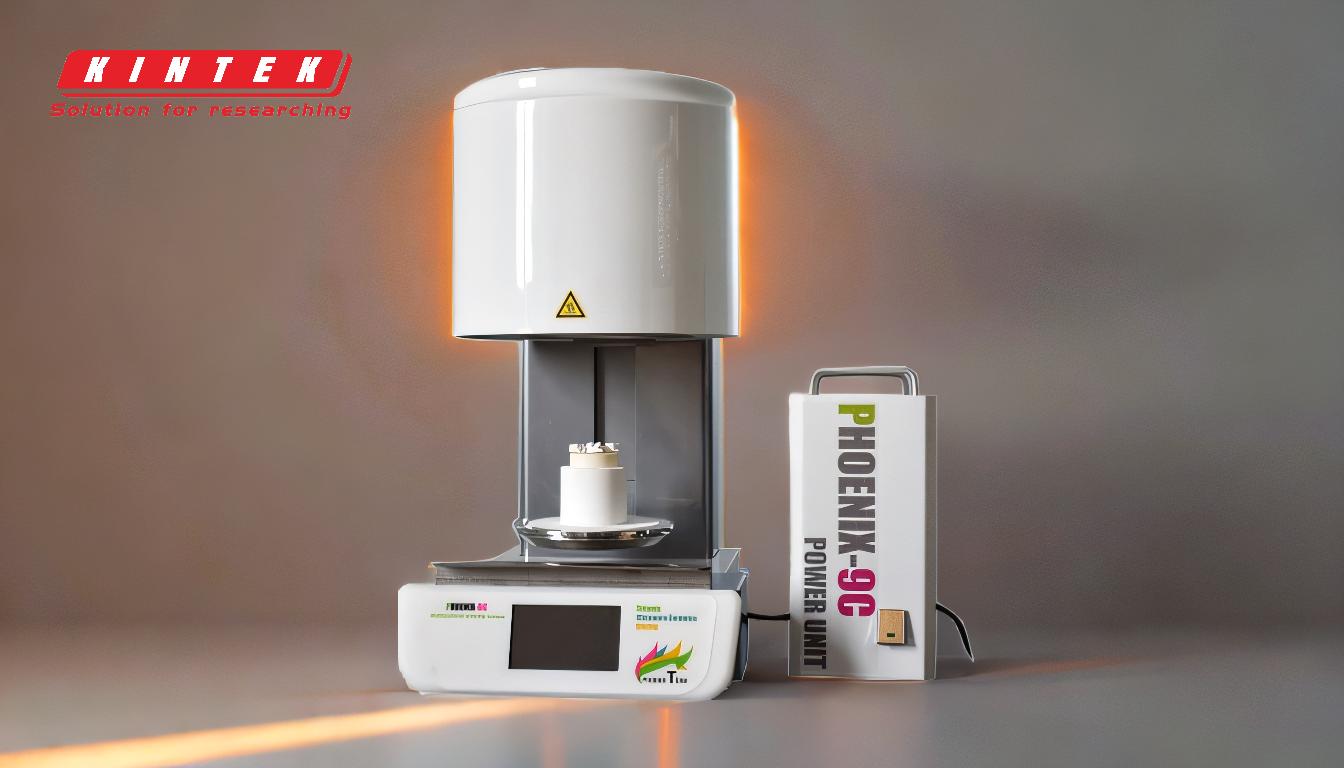
-
Enhanced Mechanical Properties
- Sintering significantly improves the strength, hardness, and wear resistance of ceramic materials.
- During sintering, particles bond through diffusion mechanisms, creating a dense and cohesive structure.
- This results in components with superior mechanical integrity, making them suitable for high-performance applications such as turbine blades and bearings.
-
Reduced Porosity
- Sintering minimizes the porosity of ceramic materials, leading to denser and more durable components.
- Reduced porosity enhances properties like strength, thermal conductivity, and electrical conductivity.
- Controlled porosity can also be achieved for specific applications, such as filters or catalysts, where gas absorbency is required.
-
Improved Thermal and Electrical Conductivity
- The densification process during sintering enhances the thermal and electrical conductivity of ceramics.
- This is particularly beneficial for applications like heat pipes, electronic components, and thermal management systems.
-
Ability to Work with High-Melting-Point Materials
- Sintering allows for the processing of ceramics with extremely high melting points, which are difficult to work with using traditional melting methods.
- This makes sintering an ideal method for manufacturing components from advanced ceramics like alumina, zirconia, and silicon carbide.
-
Precision and Control in Manufacturing
- Sintering offers high levels of control over material properties, including grain size, porosity, and density.
- This ensures consistent and repeatable production of high-quality components.
- The process also enables the creation of nearly net-shaped objects, reducing the need for additional machining.
-
Energy Efficiency and Environmental Benefits
- Sintering requires less energy compared to melting processes, making it a more environmentally friendly option.
- The process eliminates the need for lubricants and reduces surface oxygen, further contributing to its sustainability.
-
Versatility in Applications
- Sintered ceramics are used in a wide range of applications, including jewelry, bearings, heat pipes, and shotgun shells.
- The ability to tailor material properties makes sintering suitable for both structural and functional applications.
-
Creation of Complex Shapes
- Sintering enables the production of complex shapes with high precision, which is difficult to achieve with other manufacturing methods.
- This is particularly advantageous for industries requiring intricate components, such as aerospace and medical devices.
-
Improved Translucency
- For certain ceramics, sintering can enhance translucency, making them suitable for applications like optical components and dental prosthetics.
-
Cost-Effectiveness
- By reducing the need for post-processing and enabling near-net-shape manufacturing, sintering lowers production costs.
- The ability to work with difficult materials and achieve high-performance properties further adds to its cost-effectiveness.
In summary, ceramic sintering is a highly advantageous process that enhances material properties, offers precision in manufacturing, and supports a wide range of applications. Its ability to improve strength, reduce porosity, and work with high-melting-point materials makes it indispensable in advanced manufacturing and materials science.
Summary Table:
Advantage | Description |
---|---|
Enhanced Mechanical Properties | Improves strength, hardness, and wear resistance for high-performance components. |
Reduced Porosity | Minimizes porosity, enhancing durability and conductivity. |
Improved Thermal/Electrical Conductivity | Enhances performance in heat pipes and electronic components. |
High-Melting-Point Materials | Enables processing of advanced ceramics like alumina and silicon carbide. |
Precision in Manufacturing | Offers control over grain size, porosity, and density for consistent results. |
Energy Efficiency | Requires less energy and reduces environmental impact compared to melting. |
Versatility in Applications | Suitable for jewelry, bearings, heat pipes, and more. |
Complex Shape Creation | Produces intricate components for aerospace and medical industries. |
Improved Translucency | Enhances translucency for optical and dental applications. |
Cost-Effectiveness | Reduces post-processing and lowers production costs. |
Unlock the potential of ceramic sintering for your projects—contact our experts today to learn more!