Induction furnaces, particularly coreless induction furnaces, offer numerous advantages over traditional melting methods, making them a preferred choice in modern foundries. They are highly efficient, environmentally friendly, and provide precise control over the melting process. Coreless induction furnaces are compact, lightweight, and capable of fast heating, which enhances production efficiency. They also minimize oxidation and decarburization, reduce energy consumption, and improve working conditions by eliminating pollutants like dust and smoke. These features make them ideal for melting a wide range of metals, including cast iron, while ensuring high-quality output and operational safety.
Key Points Explained:
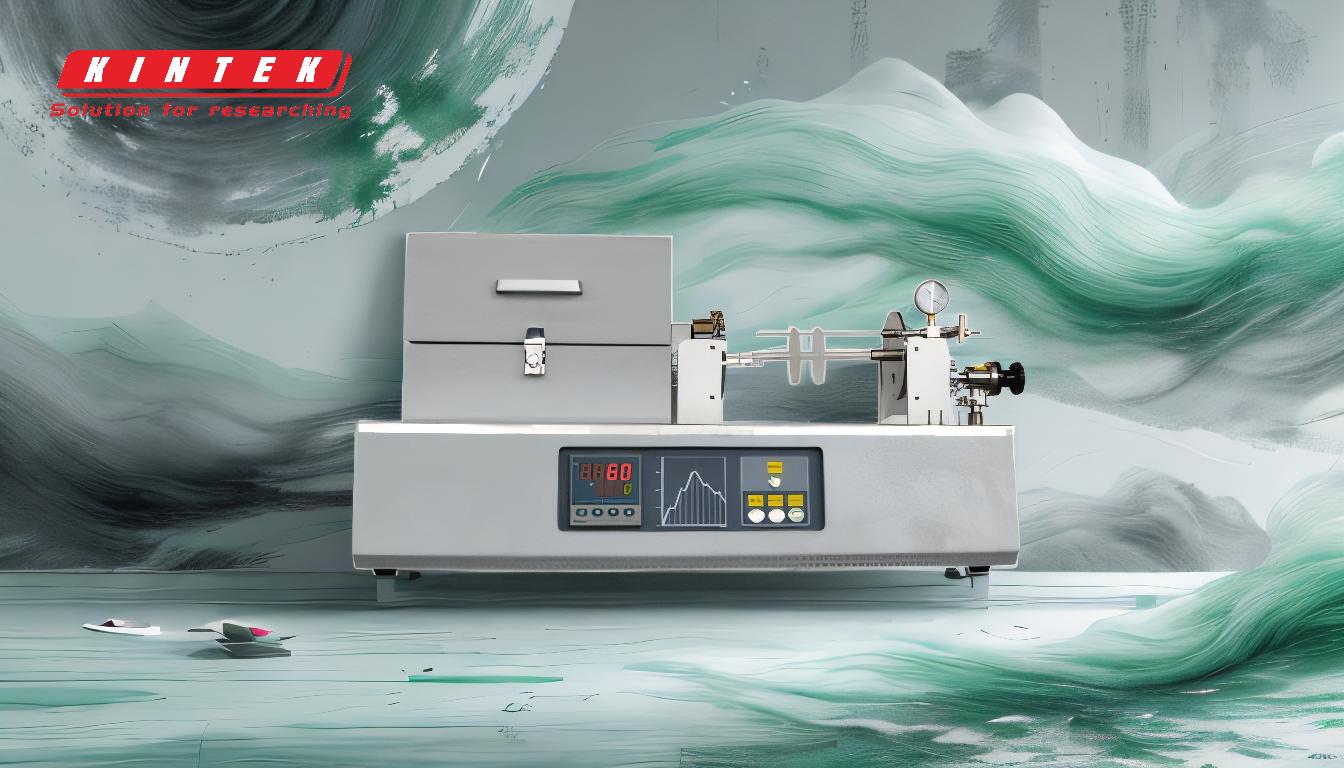
-
High Efficiency and Fast Heating
- Coreless induction furnaces are designed for rapid heating and melting, significantly reducing processing time.
- Their high efficiency translates to lower power consumption, making them cost-effective for industrial applications.
- The fast heating speed ensures high production rates, which is crucial for meeting demanding manufacturing schedules.
-
Environmental Benefits
- Unlike traditional furnaces, coreless induction furnaces produce minimal pollutants, such as dust and smoke.
- They operate without combustion, eliminating harmful byproducts and contributing to a cleaner working environment.
- The absence of slag and air pollution, as seen in vacuum induction furnaces, ensures a more sustainable melting process.
-
Precise Temperature Control
- Coreless induction furnaces offer superior temperature control, ensuring consistent and accurate melting conditions.
- The small temperature difference between the core and surface of the metal reduces the risk of defects and improves the quality of the final product.
- This precision is particularly beneficial for processes requiring strict thermal management, such as annealing and quenching.
-
Compact and Lightweight Design
- The small size and lightweight nature of coreless induction furnaces make them easy to install and operate in limited spaces.
- Their portability and flexibility allow for integration into various production setups, enhancing operational efficiency.
-
Improved Working Conditions
- The clean and pollution-free operation of coreless induction furnaces creates a safer and healthier environment for workers.
- Reduced exposure to harmful emissions and improved ergonomics contribute to better overall working conditions.
-
Cost Savings
- Coreless induction furnaces minimize material loss due to oxidation and decarburization, leading to significant cost savings.
- Their energy-efficient design reduces fuel consumption, lowering operational expenses over time.
- The extended lifespan of forging dies and reduced maintenance requirements further enhance their economic benefits.
-
Versatility in Applications
- Coreless induction furnaces are suitable for melting a wide range of metals, including cast iron, steel, and non-ferrous alloys.
- Their ability to handle diverse materials makes them a versatile choice for various industrial applications, from foundries to metalworking shops.
-
Stirring Action for Uniform Melting
- The electromagnetic stirring action in coreless induction furnaces ensures uniform heating and mixing of molten metal.
- This feature is particularly advantageous for producing high-quality alloys with consistent composition and properties.
In summary, coreless induction furnaces provide a combination of efficiency, environmental sustainability, precision, and cost-effectiveness, making them an ideal solution for modern metal melting and processing needs. Their advanced features and versatility ensure they remain a cornerstone of industrial manufacturing.
Summary Table:
Advantage | Key Benefits |
---|---|
High Efficiency | Fast heating, lower power consumption, high production rates |
Environmental Benefits | Minimal pollutants, no combustion, sustainable melting process |
Precise Temperature Control | Consistent melting, reduced defects, improved product quality |
Compact Design | Easy installation, lightweight, portable, and space-saving |
Improved Working Conditions | Clean operation, reduced emissions, safer environment for workers |
Cost Savings | Reduced material loss, lower energy consumption, extended equipment lifespan |
Versatility | Melts cast iron, steel, and non-ferrous alloys for diverse industrial uses |
Uniform Melting | Electromagnetic stirring ensures consistent alloy composition and properties |
Ready to enhance your metal melting process? Contact us today to learn more about coreless induction furnaces!