Double layer sintering, a specialized form of the sintering process, offers several unique advantages that make it a preferred method in various industrial applications. This process involves sintering two distinct layers of material, which can be of the same or different compositions, to create a final product with enhanced properties. The benefits of double layer sintering include improved mechanical strength, tailored material properties, cost-effectiveness, and the ability to produce complex shapes with high precision. These advantages stem from the fundamental principles of sintering, such as the reduction of porosity, the development of sintered necks between particles, and the diffusion of alloying elements. Additionally, double layer sintering allows for the integration of different materials, enabling the creation of components with specific functional requirements, such as improved thermal or electrical conductivity, or enhanced wear resistance. This method is particularly useful in applications where the final product needs to exhibit a combination of properties that cannot be achieved with a single material.
Key Points Explained:
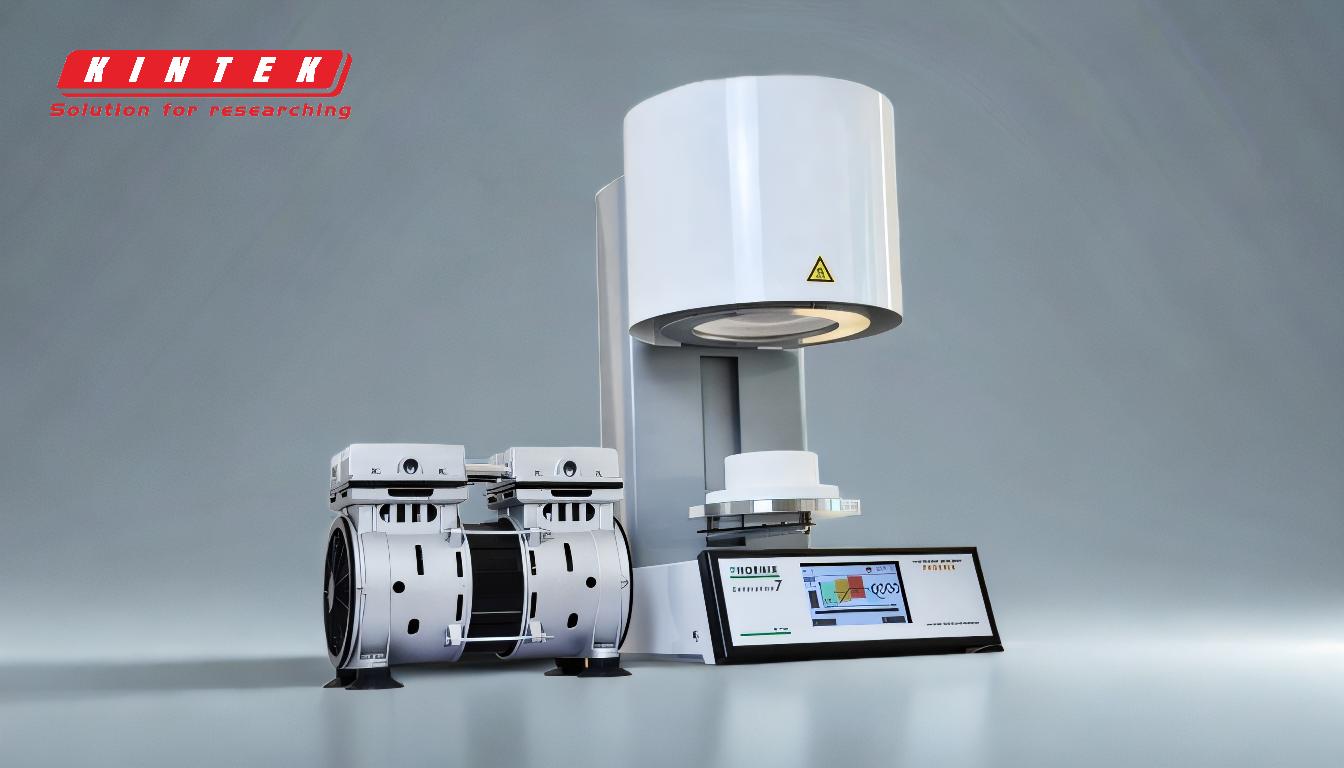
-
Enhanced Mechanical Properties:
- Reduction of Porosity: Double layer sintering significantly reduces porosity by developing sintered necks between particles, which leads to a denser and stronger final product. This is particularly beneficial in applications requiring high structural integrity.
- Increased Strength: The diffusion of alloying elements like nickel, copper, and graphite during sintering enhances the material's strength and durability, making it suitable for demanding applications.
-
Tailored Material Compositions:
- Customizable Properties: By sintering two different materials together, it is possible to create components with tailored properties. For example, one layer could provide high strength, while the other could offer improved thermal or electrical conductivity.
- Functional Gradients: Double layer sintering allows for the creation of functionally graded materials, where the properties change gradually from one layer to the next, offering unique performance characteristics.
-
Cost-Effectiveness:
- Material Efficiency: This process minimizes material waste by allowing the use of different materials only where needed, reducing overall costs.
- Production Efficiency: The ability to produce complex shapes in a single sintering step reduces the need for additional machining or assembly, further lowering production costs.
-
Versatility in Material Selection:
- Wide Range of Materials: Double layer sintering is compatible with a variety of materials, including metals, ceramics, and composites, making it versatile for different industrial applications.
- High Melting Point Materials: The process is particularly advantageous for materials with high melting points, as it allows for the integration of such materials without the need for melting.
-
Complex Shape Production:
- High Precision: The use of molds and dies made by wire EDM with centesimal tolerances enables the production of components with complex external and internal shapes.
- Net-Shaped Objects: Double layer sintering can produce nearly net-shaped objects, reducing the need for post-processing and ensuring high dimensional accuracy.
-
Improved Functional Properties:
- Thermal and Electrical Conductivity: The process can enhance the thermal and electrical conductivity of materials, making it suitable for applications like heat pipes and electrical contacts.
- Wear Resistance: By combining materials with different wear properties, double layer sintering can produce components with enhanced wear resistance, extending their service life.
-
Consistency and Control:
- Uniform Porosity: The process allows for uniform and controlled porosity, which is crucial for applications like filters or catalysts where gas absorbency is required.
- Repeatable Operations: Double layer sintering offers highly repeatable operations due to controlled grain size and uniform material properties, ensuring consistent quality in mass production.
In summary, double layer sintering is a highly advantageous process that combines the benefits of traditional sintering with the ability to create components with tailored properties and complex geometries. Its versatility, cost-effectiveness, and ability to enhance material properties make it an essential technique in modern manufacturing.
Summary Table:
Advantage | Description |
---|---|
Enhanced Mechanical Properties | Reduces porosity and increases strength through sintered necks and alloy diffusion. |
Tailored Material Compositions | Combines materials for customized properties like strength, conductivity, or wear resistance. |
Cost-Effectiveness | Minimizes material waste and reduces production costs with efficient sintering. |
Versatility in Material Selection | Compatible with metals, ceramics, and composites, including high melting point materials. |
Complex Shape Production | Produces high-precision, net-shaped objects with minimal post-processing. |
Improved Functional Properties | Enhances thermal/electrical conductivity and wear resistance for specialized applications. |
Consistency and Control | Ensures uniform porosity and repeatable operations for consistent quality. |
Ready to enhance your manufacturing process? Contact us today to learn more about double layer sintering!