Graphite electrodes are highly valued in various industries due to their unique properties and versatility. They are particularly advantageous in high-temperature applications, such as steel production, where they serve as conductive materials in electric arc furnaces. Their thermal stability, electrical conductivity, and resistance to chemical reactions make them indispensable in processes like smelting, degassing, and metal melting. Additionally, graphite electrodes are lightweight, durable, and cost-effective compared to alternatives, making them a preferred choice in industries ranging from automotive to electronics and even recreational activities.
Key Points Explained:
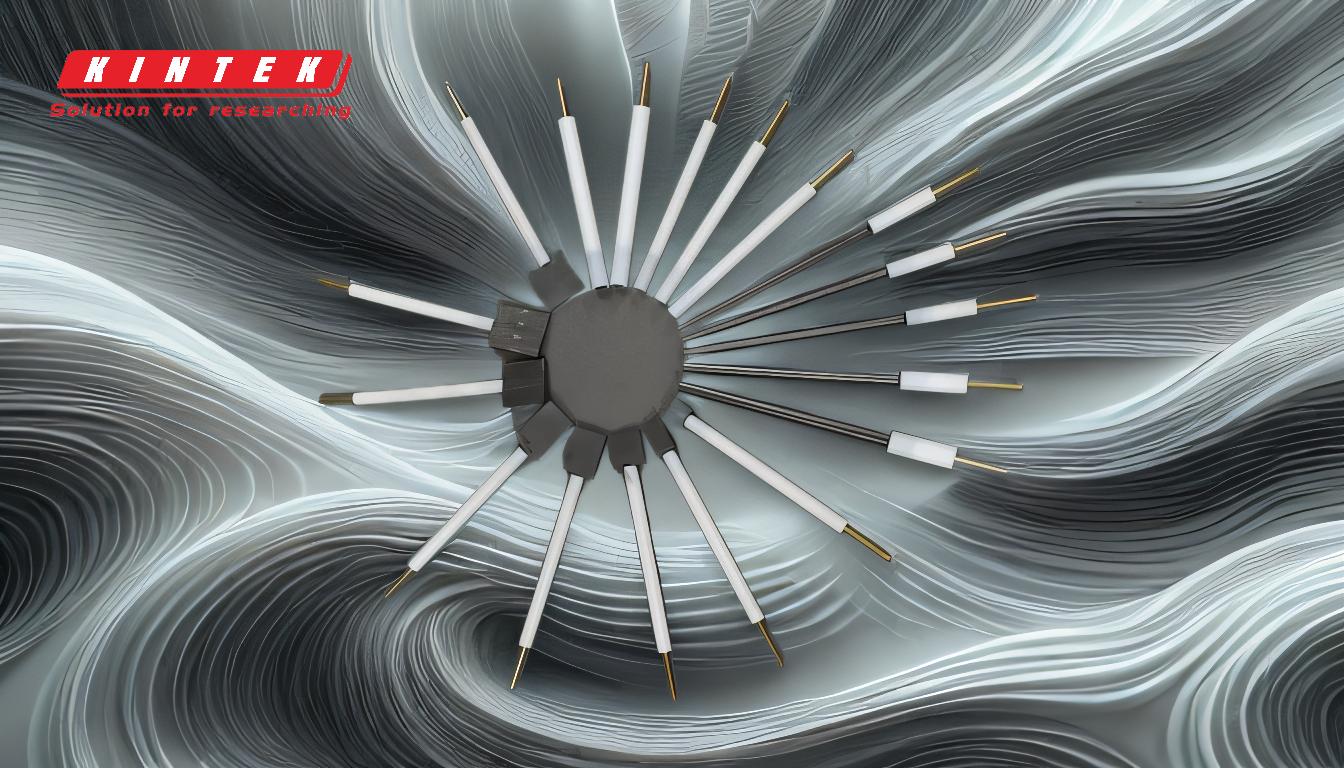
-
High Thermal Stability and Conductivity:
- Graphite electrodes can withstand extreme temperatures, up to 5000°F, without losing their structural integrity. This makes them ideal for high-temperature applications like electric arc furnaces in steel production.
- Their excellent electrical conductivity ensures efficient energy transfer, reducing energy consumption and improving process efficiency.
-
Chemical Resistance:
- Graphite is highly resistant to chemical reactions, even in corrosive environments. This property makes it suitable for use in processes like degassing, fluxing, and injection, where exposure to reactive substances is common.
-
Lightweight and Durable:
- Compared to other materials, graphite electrodes are lightweight, which simplifies handling and installation. Their durability ensures a longer lifespan, reducing the need for frequent replacements and lowering operational costs.
-
Cost-Effectiveness:
- Graphite electrodes are more economical than alternatives like copper or other conductive materials. Their cost-effectiveness, combined with their performance, makes them a preferred choice in industries such as steelmaking and metal smelting.
-
Versatility Across Industries:
- Graphite electrodes are used in a wide range of applications, including:
- Steel Production: As conductive elements in electric arc furnaces.
- Metal Smelting: For melting non-ferrous metals and alloys.
- Electronics: In the production of lithium-ion batteries and other high-tech components.
- Recreational Activities: In products like fishing rods, kite frames, and kayak handles.
- Graphite electrodes are used in a wide range of applications, including:
-
Applications in Specialized Processes:
- Graphite electrodes are essential in processes like:
- Degassing: Used in shafts and impellers to remove gases from molten metals.
- Fluxing: To improve the purity of metals during smelting.
- Injection Tubes: For precise material delivery in high-temperature environments.
- Graphite electrodes are essential in processes like:
-
Environmental and Energy Efficiency:
- The use of graphite electrodes contributes to energy efficiency in industrial processes, reducing carbon emissions and supporting sustainable manufacturing practices.
In summary, graphite electrodes offer a combination of thermal stability, chemical resistance, durability, and cost-effectiveness, making them indispensable in high-temperature and high-performance applications across multiple industries. Their versatility and efficiency ensure they remain a critical component in modern manufacturing and industrial processes.
Summary Table:
Advantage | Description |
---|---|
High Thermal Stability | Withstands extreme temperatures (up to 5000°F), ideal for electric arc furnaces. |
Excellent Conductivity | Ensures efficient energy transfer, reducing energy consumption. |
Chemical Resistance | Resists corrosion, ideal for degassing, fluxing, and injection processes. |
Lightweight & Durable | Easy to handle, long lifespan, and reduces operational costs. |
Cost-Effective | More economical than alternatives like copper. |
Versatile Applications | Used in steel production, metal smelting, electronics, and recreational products. |
Energy Efficiency | Supports sustainable manufacturing by reducing carbon emissions. |
Ready to enhance your industrial processes with graphite electrodes? Contact us today to learn more!