Hot pressing is a manufacturing process that combines heat and pressure to produce high-density, high-strength materials. This technique is widely used in industries such as ceramics, metallurgy, and composites due to its ability to create materials with superior mechanical and thermal properties. The advantages of hot pressing include improved material density, enhanced mechanical strength, better control over microstructure, and the ability to produce complex shapes with minimal defects. Additionally, hot pressing can reduce processing time and energy consumption compared to traditional sintering methods. Below, we explore the key advantages of hot pressing in detail.
Key Points Explained:
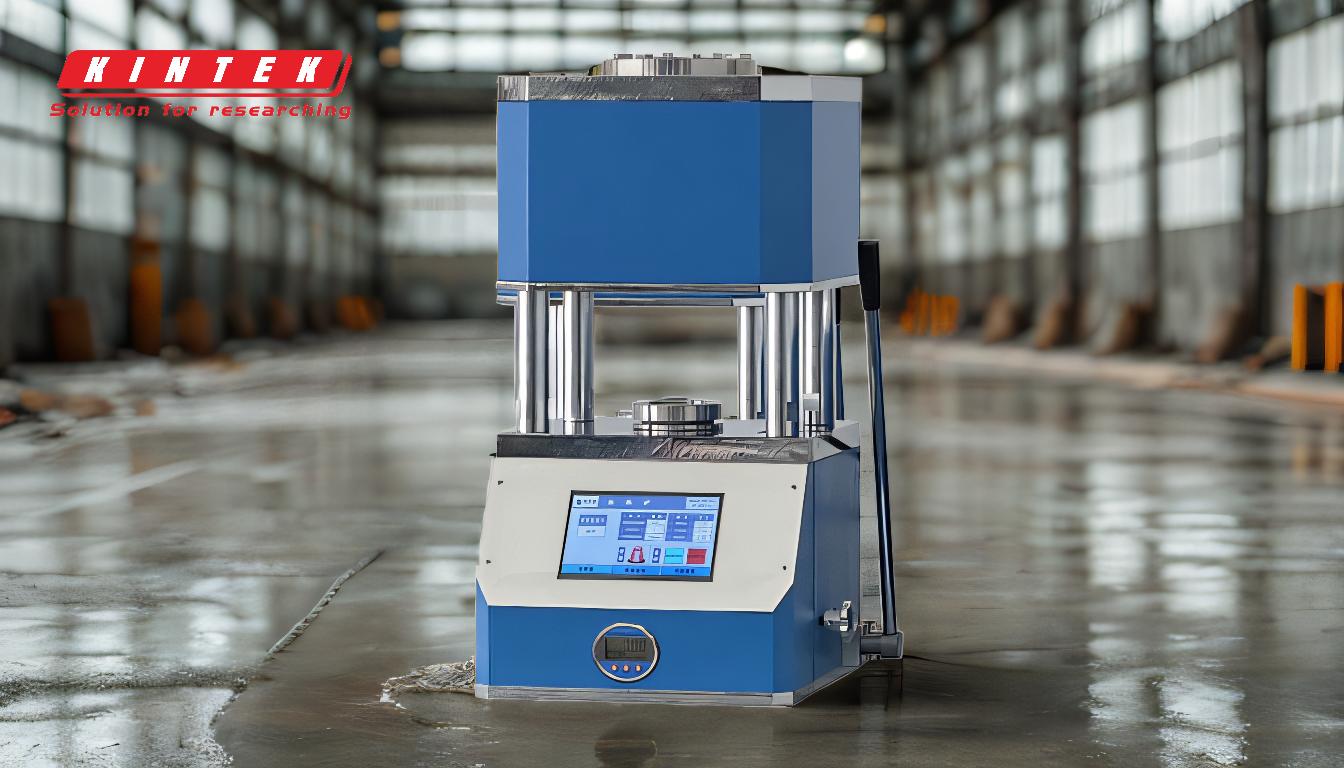
-
Improved Material Density
- Hot pressing applies both heat and pressure simultaneously, which helps in eliminating pores and voids within the material. This results in a denser final product with improved mechanical properties such as hardness, wear resistance, and fracture toughness.
- The high pressure ensures that particles are compacted tightly, while the heat facilitates diffusion and bonding between particles, leading to a more homogeneous structure.
-
Enhanced Mechanical Strength
- The combination of heat and pressure during hot pressing leads to stronger interparticle bonding, which enhances the overall strength of the material.
- This is particularly beneficial for applications requiring high load-bearing capacity, such as in aerospace components or cutting tools.
-
Better Control Over Microstructure
- Hot pressing allows for precise control over the microstructure of the material, including grain size and distribution. This control is critical for achieving desired properties such as thermal conductivity, electrical conductivity, and corrosion resistance.
- The ability to tailor the microstructure makes hot pressing suitable for advanced materials like ceramics and composites.
-
Production of Complex Shapes
- Hot pressing can be used to produce intricate shapes with minimal post-processing. The uniform application of pressure ensures that even complex geometries are formed without defects such as cracks or voids.
- This is particularly advantageous for manufacturing components with tight tolerances, such as turbine blades or medical implants.
-
Reduced Processing Time and Energy Consumption
- Compared to traditional sintering methods, hot pressing significantly reduces processing time by combining the heating and compaction steps into a single operation.
- The reduced processing time also translates to lower energy consumption, making hot pressing a more sustainable manufacturing option.
-
Minimized Defects and Improved Surface Finish
- The application of pressure during hot pressing helps in minimizing defects such as porosity and surface irregularities. This results in a smoother surface finish, reducing the need for additional machining or finishing processes.
- A defect-free surface is crucial for applications where surface integrity is critical, such as in optical components or semiconductor devices.
-
Versatility in Material Compatibility
- Hot pressing is compatible with a wide range of materials, including metals, ceramics, and composites. This versatility makes it a preferred choice for industries requiring diverse material properties.
- For example, it is used in the production of advanced ceramics for electronics, metal matrix composites for automotive applications, and carbon-carbon composites for aerospace.
-
Cost-Effectiveness in Large-Scale Production
- While the initial setup cost for hot pressing equipment may be high, the process becomes cost-effective in large-scale production due to its efficiency and reduced waste.
- The ability to produce high-quality components with minimal post-processing further contributes to cost savings.
In summary, hot pressing offers numerous advantages, including improved material properties, enhanced mechanical strength, and the ability to produce complex shapes with minimal defects. Its efficiency and versatility make it a valuable process in various industries, from aerospace to electronics. By understanding these benefits, equipment and consumable purchasers can make informed decisions when selecting manufacturing processes for their specific applications.
Summary Table:
Advantage | Description |
---|---|
Improved Material Density | Eliminates pores and voids, resulting in denser, stronger materials. |
Enhanced Mechanical Strength | Stronger interparticle bonding for high load-bearing applications. |
Better Microstructure Control | Precise grain size and distribution for tailored material properties. |
Complex Shape Production | Forms intricate geometries with minimal defects and post-processing. |
Reduced Processing Time | Combines heating and compaction, saving time and energy. |
Minimized Defects | Smooth surface finish, reducing the need for additional machining. |
Material Versatility | Compatible with metals, ceramics, and composites for diverse applications. |
Cost-Effectiveness | Efficient and low-waste process, ideal for large-scale production. |
Ready to enhance your manufacturing process? Contact us today to learn more about hot pressing solutions!