Sintering is a critical process in materials science, particularly in the production of ceramics, metals, and composites. The application of pressure during sintering, such as in hot pressing, offers several advantages that enhance the material's properties and efficiency of the process. Pressure accelerates the sintering process, reduces porosity, and improves mechanical and physical properties like strength, conductivity, and durability. It also helps in the fusion of materials that are otherwise difficult to sinter, making it a valuable technique in advanced material manufacturing.
Key Points Explained:
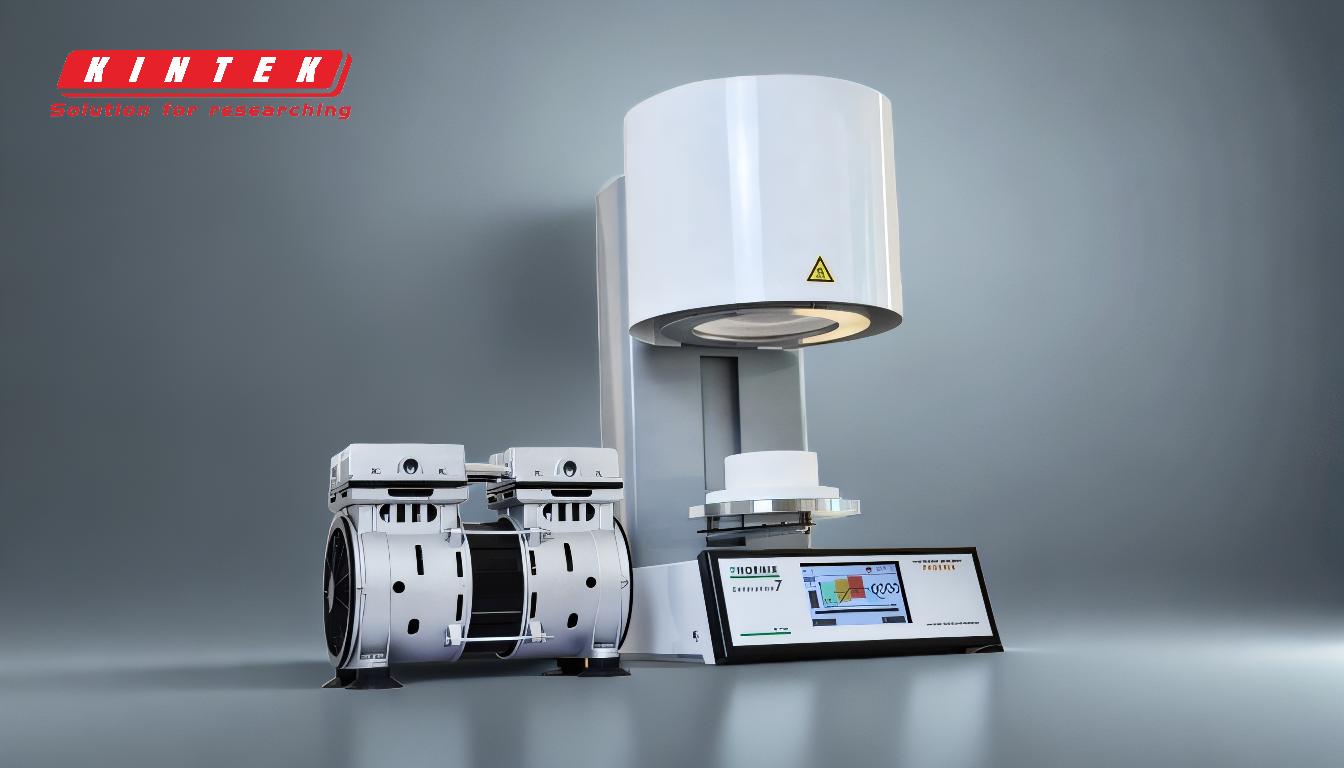
-
Enhanced Material Fusion and Reduced Sintering Time:
- Explanation: Applying pressure during sintering provides an additional driving force that facilitates the fusion of particles. This is particularly beneficial for materials that are difficult to sinter under normal conditions. The pressure helps to decrease the sintering time significantly, making the process more efficient.
- Impact: This reduction in time not only speeds up production but also reduces energy consumption, making the process more cost-effective and environmentally friendly.
-
Reduction in Porosity and Improvement in Material Density:
- Explanation: One of the primary effects of applying pressure during sintering is the reduction in porosity. Pressure compacts the material more effectively, leading to a denser final product with fewer voids.
- Impact: Lower porosity enhances the material's mechanical properties, such as tensile strength and durability, and improves its physical properties, including electrical and thermal conductivity.
-
Improvement in Mechanical and Physical Properties:
- Explanation: The application of pressure influences the microstructure of the material, particularly the grain size, pore size, and grain boundary distribution. These changes lead to improvements in the material's strength, hardness, and resistance to wear and tear.
- Impact: Enhanced mechanical properties make the material suitable for more demanding applications, such as in aerospace, automotive, and structural engineering.
-
Development of Sintered Necks and Enhanced Strength:
- Explanation: Pressure facilitates the development of sintered necks between particles, which are crucial for reducing pores and increasing the overall strength of the material. It also aids in the diffusion of elements like nickel, copper, and graphite, which further enhance the material's properties.
- Impact: The formation of strong sintered necks leads to a more cohesive and robust material structure, which is essential for high-performance applications.
-
Elimination of Lubricants and Reduction of Surface Oxygen:
- Explanation: The sintering process under pressure helps in eliminating lubricants that are often used in the compaction of powders. It also reduces the presence of surface oxygen, which can be detrimental to the material's properties.
- Impact: This results in a cleaner and more homogeneous material, which is crucial for applications requiring high purity and consistency.
-
Versatility in Material Applications:
- Explanation: The ability to apply pressure during sintering makes it possible to process a wide range of materials, including those that are typically challenging to sinter. This versatility opens up new possibilities for material design and application.
- Impact: Manufacturers can produce advanced materials with tailored properties for specific applications, such as filters, catalysts, and high-strength components.
In summary, the application of pressure during sintering offers numerous advantages, including faster processing times, reduced porosity, enhanced mechanical and physical properties, and the ability to process difficult materials. These benefits make pressure-assisted sintering a valuable technique in the production of high-performance materials for various industrial applications.
Summary Table:
Advantage | Impact |
---|---|
Enhanced Material Fusion | Faster sintering, reduced energy consumption, and cost-effectiveness |
Reduced Porosity | Improved density, strength, and conductivity |
Improved Mechanical Properties | Higher strength, hardness, and wear resistance for demanding applications |
Formation of Sintered Necks | Stronger material structure and enhanced durability |
Elimination of Lubricants | Cleaner, more homogeneous materials for high-purity applications |
Versatility in Material Applications | Ability to process challenging materials for advanced industrial uses |
Unlock the potential of pressure-assisted sintering for your materials—contact our experts today!