Pressure sintering, including hot pressing and high-pressure sintering, offers numerous advantages in material processing and fabrication. It enables the production of components with enhanced mechanical, thermal, and electrical properties, while also improving densification, reducing porosity, and controlling material quality. This method is particularly beneficial for advanced ceramics and specialized materials, as it allows for precise control over the sintering process, resulting in high-performance products with complex shapes and near-theoretical density. Below, the key advantages of pressure sintering are explained in detail.
Key Points Explained:
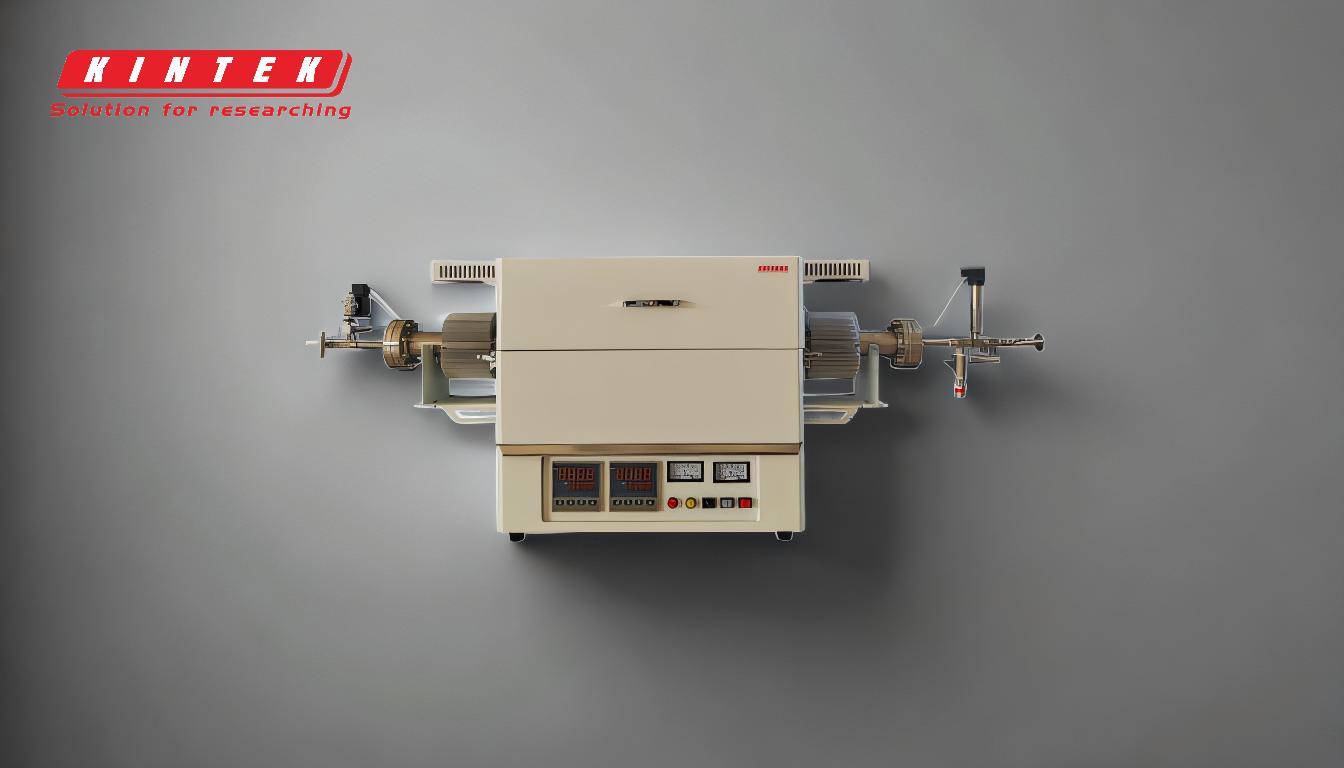
-
Improved Material Properties
- Pressure sintering enhances mechanical properties such as flexural strength, fracture toughness, and wear resistance.
- It improves thermal conductivity and electrical/dielectric properties, making it ideal for advanced materials like silicon nitride ceramics.
- The process reduces porosity, leading to higher density and better overall performance of the sintered material.
-
Enhanced Densification and Grain Structure
- Pressure sintering promotes densification by applying simultaneous heat and pressure, resulting in materials with near-theoretical density.
- The fine grain structure achieved through this process contributes to improved mechanical and electrical properties.
-
Control Over Sintering Process
- The combination of heating and pressurization enhances mass transfer, reducing sintering temperatures and shortening sintering times.
- Advanced technologies, such as IT systems, allow for precise control over the densification process and material quality.
-
Ability to Produce Complex Shapes and Accurate Sizes
- Pressure sintering enables the fabrication of components with intricate designs and complex geometries.
- The process ensures accurate dimensions, reducing the need for post-sintering machining.
-
Prevention of Nitrogen Volatilization and Oxidation
- High-pressure sintering is particularly advantageous for materials like silicon nitride, as it prevents nitrogen volatilization at high temperatures.
- It also minimizes oxidation and contamination, improving the purity and quality of the final product.
-
Cost-Effectiveness and Energy Efficiency
- Pressure sintering requires lower deformation resistance compared to cold pressing, reducing energy consumption.
- The ability to produce large-diameter materials and achieve high production efficiency makes it a cost-effective solution.
-
Versatility in Material Selection
- This method supports the use of exotic and specialized materials, allowing for tailored compositions to meet specific performance requirements.
- It is suitable for a wide range of applications, including filters, catalysts, and advanced ceramics.
-
Short Sintering Times and High Production Efficiency
- The simultaneous application of heat and pressure significantly reduces sintering time, enhancing production efficiency.
- The process yields excellent product performance, making it ideal for industrial-scale manufacturing.
In conclusion, pressure sintering is a highly advantageous method for producing advanced materials with superior properties. Its ability to enhance densification, control material quality, and produce complex shapes makes it a preferred choice for industries requiring high-performance components. Additionally, its cost-effectiveness and energy efficiency further solidify its role as a key technology in modern material processing.
Summary Table:
Advantage | Key Benefits |
---|---|
Improved Material Properties | Enhanced mechanical, thermal, and electrical properties; reduced porosity. |
Enhanced Densification | Near-theoretical density; fine grain structure for better performance. |
Control Over Sintering Process | Reduced sintering temperatures and times; precise material quality control. |
Complex Shapes & Accurate Sizes | Intricate designs; minimal post-sintering machining required. |
Prevention of Oxidation | Minimized nitrogen volatilization and oxidation; improved purity. |
Cost-Effectiveness | Lower energy consumption; high production efficiency. |
Versatility in Material Selection | Supports exotic and specialized materials for tailored applications. |
Short Sintering Times | Faster production; excellent product performance for industrial-scale use. |
Ready to elevate your material processing? Contact us today to learn how pressure sintering can transform your production!