Twin-screw granulation (TSG) is an advanced granulation technique that offers several advantages over traditional methods, particularly in the context of continuous manufacturing. By densifying materials, TSG reduces storage and transportation costs, improves material handling, and enhances fluidity. Its continuous operation ensures consistent product quality, scalability, and reduced production time, making it a preferred choice in modern pharmaceutical and chemical manufacturing processes.
Key Points Explained:
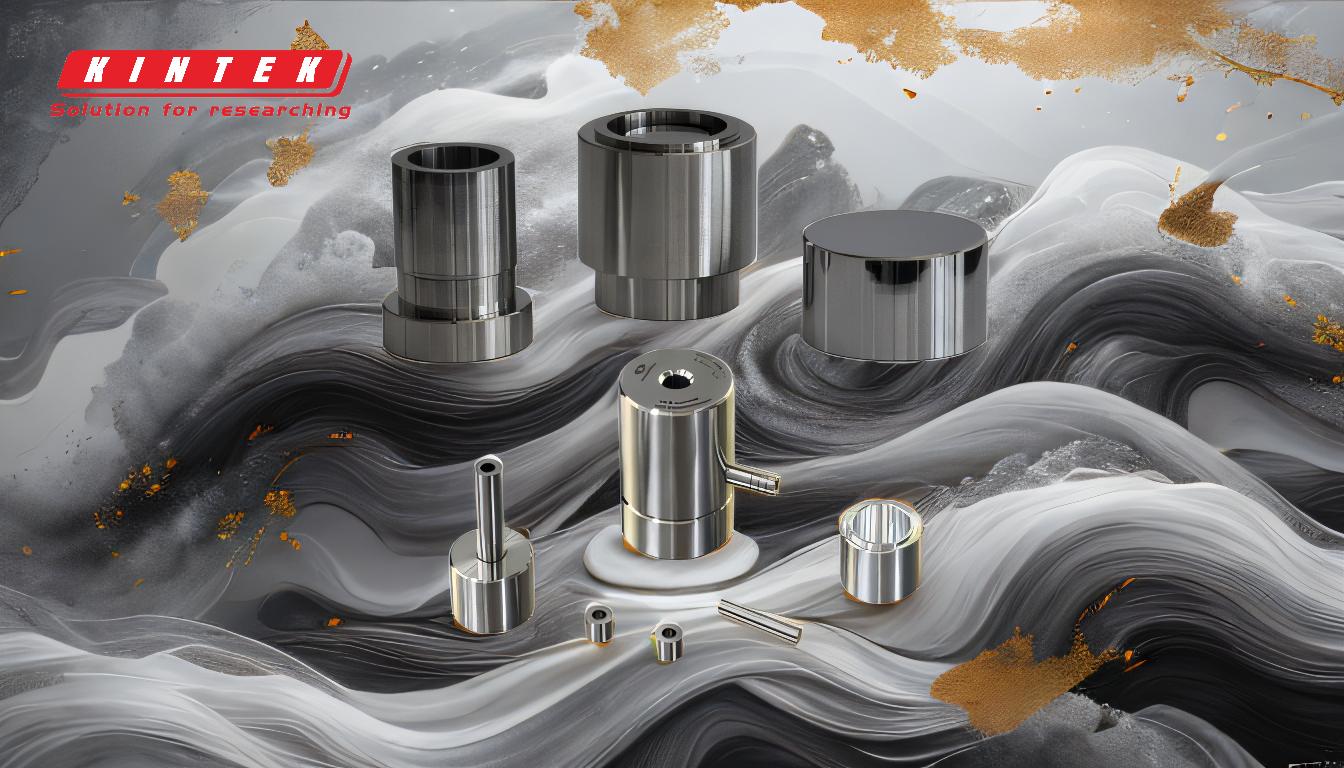
-
Continuous Manufacturing Capability:
- TSG enables continuous manufacturing, which is a significant improvement over batch processing. This ensures a steady and uninterrupted production flow, reducing downtime and increasing efficiency.
- Continuous manufacturing also allows for real-time monitoring and control, leading to consistent product quality and reduced variability.
-
Densification of Materials:
- TSG densifies materials, making them more compact. This reduces the volume of the final product, leading to lower storage and transportation costs.
- Densification also improves the handling characteristics of the material, making it easier to transport and process further.
-
Improved Material Fluidity:
- The granulation process enhances the fluidity of the material, which is crucial for downstream processes such as tableting or capsule filling.
- Improved fluidity ensures uniform distribution and flow, leading to better product consistency and quality.
-
Scalability and Flexibility:
- TSG systems are highly scalable, allowing for easy adjustment of production rates to meet varying demands.
- The flexibility of TSG systems enables the processing of a wide range of materials, including those with different particle sizes and properties.
-
Reduced Production Time:
- Continuous operation of TSG systems reduces the overall production time compared to traditional batch processes.
- This leads to faster turnaround times and the ability to respond quickly to market demands.
-
Enhanced Product Quality:
- The controlled and continuous nature of TSG ensures uniform granule size and distribution, leading to higher product quality.
- Consistent granule properties improve the performance of the final product, whether in pharmaceuticals or other industries.
-
Cost Efficiency:
- By reducing storage, transportation, and production costs, TSG offers significant cost savings over traditional granulation methods.
- The efficiency of continuous manufacturing also reduces labor and energy costs, contributing to overall cost efficiency.
-
Environmental Benefits:
- Continuous manufacturing processes like TSG generate less waste and require fewer resources, making them more environmentally friendly.
- The reduction in material handling and transportation also contributes to a lower carbon footprint.
In summary, twin-screw granulation provides a modern, efficient, and cost-effective solution for material processing, offering numerous advantages over traditional granulation methods. Its continuous manufacturing capability, combined with improved material properties and operational flexibility, makes it an ideal choice for industries seeking to enhance their production processes and product quality.
Summary Table:
Advantage | Description |
---|---|
Continuous Manufacturing | Ensures steady production flow, real-time monitoring, and consistent quality. |
Densification of Materials | Reduces storage and transportation costs, improves material handling. |
Improved Material Fluidity | Enhances downstream processes like tablet punching machine and capsule filling. |
Scalability and Flexibility | Adjust production rates and process diverse materials with ease. |
Reduced Production Time | Faster turnaround times compared to traditional batch processes. |
Enhanced Product Quality | Uniform granule size and distribution for higher-quality products. |
Cost Efficiency | Lowers storage, transportation, labor, and energy costs. |
Environmental Benefits | Generates less waste, reduces carbon footprint, and saves resources. |
Ready to transform your manufacturing process? Contact us today to learn more about twin-screw granulation!